Heavy commercial vehicle enterprises continue to carry out structural optimization and material upgrading trial production of chassis support-balancing shaft support. The balance axle bracket is an important part of the balance suspension, which mainly plays a role in connecting the frame and the leaf spring, ensuring the real-time balance of the load of the double rear axle, and plays an important role in improving the driving performance and passing performance of the vehicle. It is proposed to use high-performance ductile iron QT800-5 to replace ordinary ductile iron QT500-7.
The mass before optimization is 51 kg. The original design scheme is shown in Figure 1. After redesign and mechanical performance simulation calculation, the mass is finally reduced to 36 kg, the mass of a single piece is reduced by 15 kg, and the weight reduction rate is up to 29%. The lightweight design is shown in Figure 2. The main indicators of mechanical properties are: tensile strength is 800 MPa, yield strength is 480 MPa, elongation is 5%, material hardness is 245~335 HBW 10/3000, material density is 7.3 kg/m3, and the main structural changes are: the main wall thickness is reduced from 14 mm and 16 mm to 12 mm.
In the design of the structure, the solidification characteristics of nodular cast iron are fully considered to reduce its section sensitivity, and the uniform wall thickness design is adopted as far as possible to maximize the material characteristics.
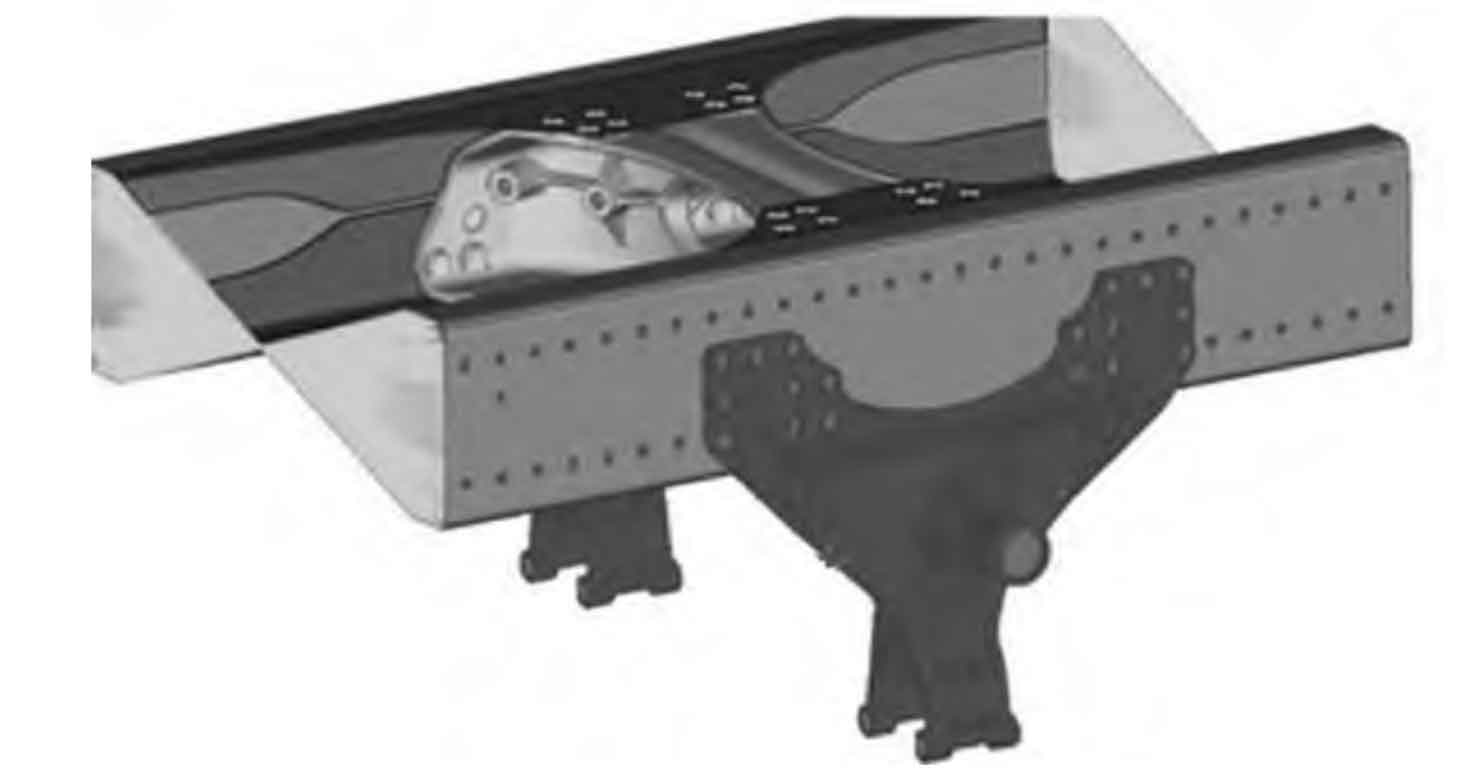
The design constraints are shown in Figure 3. The load of working condition is set as: 220 000 N in the Z direction of vertical working condition, 90 000 N in the Z direction of braking working condition, and 120 000 N in the X direction.
Edition | Mass/kg | Whether the maximum stress under vertical working condition meets the requirements | Whether the maximum stress under braking condition meets the requirements | Whether the safety factor meets the product requirements |
Original structure balance shaft support | 51 | yes | yes | yes |
Optimized rear balance shaft support | 36 | yes | yes | yes |
In order to compare the stress conditions of the new and the old two structural schemes, the original structure and the optimized design structure are constrained and simulated under the same load, and the comparative analysis is carried out. Through the analysis, it is found that the maximum stress of the two schemes are concentrated at the root of the circumference. It can be seen from the table that the weight of the optimized support is reduced by 15 kg.