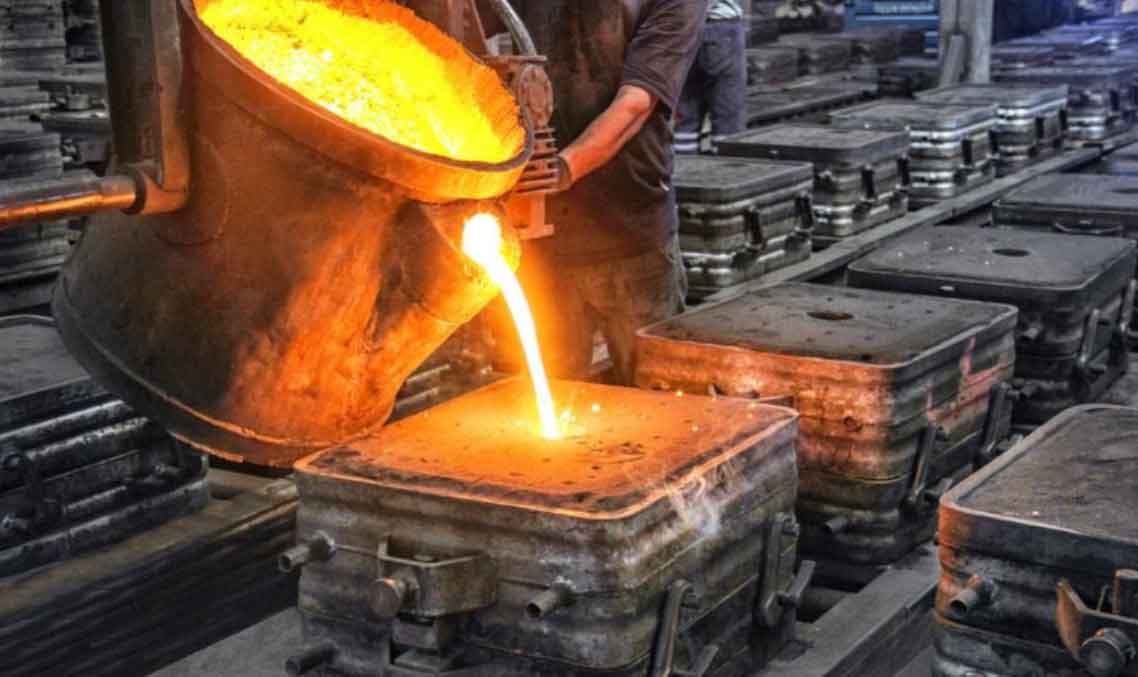
Introduction
Sand casting is a widely used manufacturing process for producing metal parts and components. It is a versatile and cost-effective method that allows for the production of complex shapes and sizes. In this comprehensive overview, I’ll explain the science behind sand casting, including the process steps, materials involved, and considerations for successful casting.
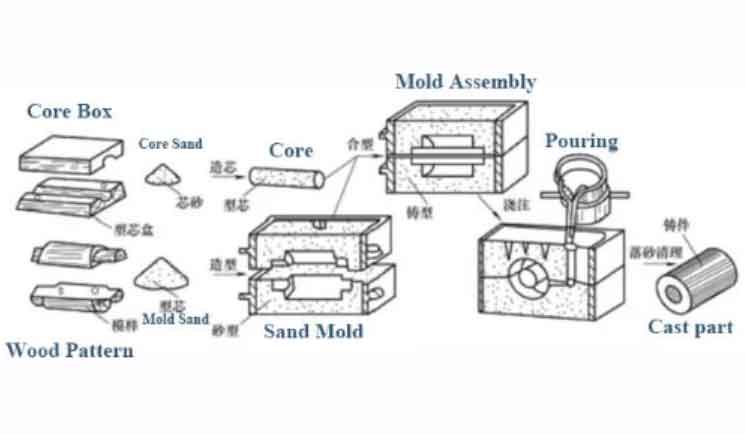
1.Introduction to Sand Casting Parts:
Sand casting parts are technique that involves pouring molten metal into a mold cavity formed in a mixture of sand and a binder material. Once the metal solidifies, the mold is removed, and the resulting casting is cleaned, finished, and prepared for use.
2.Mold Preparation:
The first step in sand casting parts are preparing the mold. A pattern, which is a replica of the desired part, is created using wood, plastic, or metal. The pattern is placed in a flask, which is a frame that holds the mold material. The flask is typically divided into two halves, called the cope and drag.
3.Sand Mixtures:
The mold material is a mixture of sand and a binder. The sand used is typically silica sand, which has good refractory properties and can withstand high temperatures. The binder, such as clay or resin, helps the sand particles stick together and maintain their shape.
4.Molding Process:
The molding process involves several steps:
- a. The pattern is placed in the drag half of the flask, and sand is packed around it.
- b. The cope half of the flask is placed on top, and more sand is added and packed to complete the mold.
- c. To create cavities and internal features, cores made of sand or other materials are placed in the mold.
- d. The mold is compacted to ensure proper density and to minimize defects.
5.Pouring and Solidification:
Once the mold is ready, it is opened, and the pattern is removed. Channels, called sprues and risers, are created to facilitate the flow of molten metal and compensate for shrinkage during solidification. The mold is then closed, and the molten metal is poured into the mold cavity.
6.Cooling and Removal:
The molten metal cools and solidifies inside the mold, taking the shape of the cavity and the core. Cooling times can vary depending on the size and complexity of the part. After solidification, the mold is opened, and the casting is removed.
7.Finishing and Cleaning:
The casting may have excess material, such as gates and risers, which need to be removed. Finishing operations, such as grinding, sanding, and machining, are performed to achieve the desired dimensions and surface finish. Heat treatment processes, such as annealing or tempering, may also be applied to enhance the mechanical properties of the casting.
8.Considerations for Successful Casting:
- a. Design: The part should have draft angles, fillets, and proper wall thickness to allow for easy mold removal and minimize defects.
- b. Material Selection: The choice of metal alloy should consider its fluidity, solidification characteristics, and compatibility with the sand mold.
- c. Mold Quality: The mold should be well-ventilated, have good dimensional accuracy, and be free from defects like air pockets, sand inclusions, and cracks.
- d. Pouring Parameters: Proper pouring temperature, gating system design, and pouring rate are essential to achieve good fillability and avoid defects.
- e. Shrinkage and Distortion: Compensating for shrinkage and distortion during solidification is crucial. The use of risers and proper feeding systems helps minimize these issues.
Sand casting parts are the versatile and widely used process for manufacturing metal parts. It offers the advantages of low tooling costs, adaptability to various part sizes, and the ability to cast complex geometries. By understanding the science behind sand casting parts and implementing best practices, manufacturers can produce high-quality castings for a wide range of applications.
Chapter 1: The Sand Casting parts Steps

Sand casting part is one of the oldest and most widely used casting processes for creating metal parts. It involves making a mold from compacted sand and then pouring molten metal into the mold cavity. Here are the basic steps of the sand casting parts:
1. Pattern Creation:
- A pattern, typically made from wood, metal, or plastic, is created in the shape of the desired final metal part.
- The pattern includes additional features such as gating and risers (channels for pouring molten metal and allowing air to escape).
2. Mold Preparation:
- A two-part mold is made by pressing the pattern into a sand mixture, forming an impression of the pattern.
- The mold is made in two halves, the cope (top half) and the drag (bottom half), which are separated to remove the pattern.
3. Core Production (Optional):
- Cores are inserts made of sand or a similar material that create hollow areas or complex internal shapes in the final casting.
- Cores are positioned within the mold to shape the internal features of the casting.
4. Mold Assembly:
- The cope and drag halves are assembled to create the complete mold cavity.
- Channels (gates, runners, and risers) are created in the sand to allow molten metal to flow into the mold cavity and gases to escape.
5. Molten Metal Pouring:
- Molten metal, heated in a furnace, is poured into the sprue (main pouring channel) and flows through the gating system into the mold cavity.
6. Solidification:
- The molten metal cools and solidifies as it comes into contact with the cooler mold surfaces.
- As the metal solidifies, it takes the shape of the mold cavity, including the external and internal features of the part.
7. Cooling and Solidification:
- The casting is allowed to cool until the metal has fully solidified and reached a temperature suitable for handling.
8. Mold Breakdown:
- The cope and drag halves are separated to reveal the solidified metal casting.
- Any sand adhering to the casting is removed through mechanical methods or cleaning processes.
9. Finishing Operations:
- Excess material, called “risers” or “feeders,” which were used to supply additional molten metal to compensate for shrinkage during solidification, are removed.
- The casting may undergo additional post-processing steps such as machining, grinding, polishing, heat treatment, and surface finishing.
10. Inspection:
- The finished casting is inspected to ensure it meets the desired specifications and quality standards.
- Defects such as porosity, cracks, and dimensional deviations are identified and addressed.
11. Final Product:
- Once the casting passes inspection, it becomes the final metal part, ready for assembly or integration into the intended application.
Sand casting parts are the versatile process used for a wide range of metal parts, from simple shapes to complex components. While it’s an effective method for producing parts with various sizes and configurations, it can have limitations in terms of dimensional accuracy and surface finish compared to more precise casting processes like investment casting or die casting.
Chapter 2: Sand mold preparation for sand casting parts
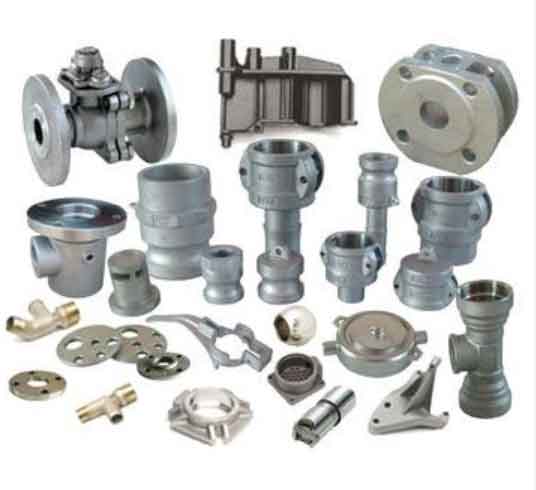
The preparation of sand molds is a crucial step in the sand casting parts. Properly preparing the mold ensures that it can withstand the pouring of molten metal and accurately replicate the desired shape of the final casting. Here are the steps involved in preparing sand molds for sand casting parts :
1. Pattern Placement:
- The first step is to place the pattern, which is a replica of the final part, into the molding box (also called the flask). The flask consists of two parts: the cope (top) and the drag (bottom).
2. Flask Preparation:
- The drag is placed on the bottom board, and the pattern is positioned in the drag. The drag is then filled with a layer of molding sand.
3. Ramming the Sand:
- The sand in the drag is compacted using a rammer or pneumatic tool to create a dense and uniform layer called the drag half of the mold.
4. Placing Cores (if needed):
- If the final part requires internal features or hollow sections, cores are positioned within the drag. Cores are made from sand mixed with binders that help them maintain their shape during handling and casting.
5. Parting Line and Core Print Placement:
- The parting line is a designated boundary where the cope and drag will separate to remove the pattern and form the mold cavity.
- Core prints, which are extensions of the pattern used to support the cores, are placed within the mold to position and secure the cores.
6. Cope Assembly:
- The cope is placed on top of the drag, enclosing the pattern and any cores. The two halves of the flask are aligned using alignment pins.
7. Sprue, Runner, and Gate Placement:
- Channels known as sprues, runners, and gates are formed within the sand to direct molten metal into the mold cavity and allow gases to escape.
- The sprue is a vertical channel connected to the pouring basin, which leads to the runners and gates that distribute the molten metal to the mold cavity.
8. Ramming the Cope:
- The sand in the cope is compacted using a rammer or pneumatic tool to create a dense and uniform layer called the cope half of the mold.
9. Venting and Parting Dust:
- Venting holes or channels are created in the sand to allow air and gases to escape as the molten metal enters the mold cavity.
- Parting dust (also called parting powder) is applied to the pattern and mold surfaces to prevent the sand from sticking to the pattern during separation.
10. Mold Removal and Pattern Extraction:
- The cope and drag are separated, and the pattern is removed, leaving behind cavities that replicate the pattern’s shape.
- The mold halves are carefully handled to prevent damage to the mold surfaces.
11. Final Inspection and Repair:
- The mold cavities are inspected for any defects or imperfections, such as sand inclusions or voids.
- Any defects are repaired using various techniques, such as patching or additional venting.
The prepared sand molds are now ready to receive the molten metal during the pouring phase of the sand casting parts. Proper mold preparation is crucial for producing high-quality castings with accurate dimensions and minimal defects.
Chapter 3: The Melting and Pouring of Sand Casting Parts
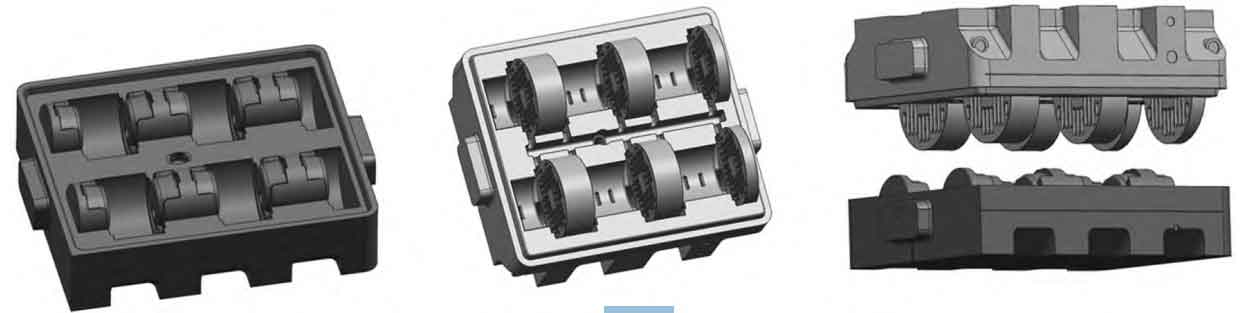
Melting and pouring are crucial steps in the sand casting parts, where molten metal is prepared and poured into a mold cavity to create the final casting. Sand casting parts are the versatile method used to produce a wide range of metal parts with varying sizes and complexities. Here’s an overview of the melting and pouring steps in sand casting parts:
Melting:
- Furnace Preparation: The first step involves preparing the furnace where the metal will be melted. Furnaces can be electric arc furnaces, induction furnaces, or other types, depending on the foundry’s capabilities and the type of metal being used.
- Metal Charge Preparation: The metal charge consists of the metal alloy to be melted. Scrap metal and alloying elements are measured and added to achieve the desired composition. The charge might include primary metals, recycled scrap, and fluxing agents.
- Charging the Furnace: The metal charge is loaded into the furnace through designated openings. The furnace is then closed and prepared for the melting process.
- Heating and Melting: The furnace is heated to the appropriate temperature to melt the metal charge. The melting temperature varies depending on the type of metal being used. As the metal melts, impurities rise to the surface and can be removed.
- Temperature Monitoring: During melting, temperature sensors are used to monitor the temperature of the molten metal. Maintaining the correct temperature is crucial for achieving the desired properties of the casting.
- Chemical Analysis: Samples of the molten metal are periodically taken for chemical analysis to ensure that the composition meets the required specifications.
Pouring:
- Mold Preparation: While the metal is being melted, the mold cavity is prepared. The mold is created by packing sand around a pattern, and any necessary cores are inserted to form internal features.
- Mold Venting: Proper venting is important to allow gases to escape from the mold during pouring. Venting channels are created in the sand to prevent gas-related defects.
- Mold Coating (Optional): Some molds may be coated with a refractory material to improve surface finish, reduce mold erosion, and aid in the separation of the casting from the mold.
- Sprue and Riser Placement: A sprue (main channel) and risers (feeders) are added to the mold to facilitate metal flow and compensate for shrinkage during solidification.
- Ladle Filling: The molten metal is transferred from the furnace to a pouring ladle. The ladle is equipped with a stopper mechanism that controls the flow of metal into the mold.
- Pouring Sequence: The pouring sequence is crucial to ensure proper metal flow, minimize turbulence, and prevent defects. Molten metal is poured from the ladle into the sprue, which feeds the mold cavity and risers.
- Solidification: As the molten metal enters the mold cavity, it starts to cool and solidify, taking on the shape of the pattern and internal cores.
- Cooling and Mold Breakout: After pouring, the casting is allowed to cool and solidify fully within the mold. Once cooled, the mold is broken away to reveal the solidified casting.
- Casting Cleaning and Finishing: The casting is removed from the mold, and any excess sand, gating systems, and risers are removed. Depending on the casting’s requirements, additional finishing processes like machining, grinding, and surface treatment may be performed.
Melting and pouring require precise control of temperature, composition, and pouring techniques to achieve high-quality castings. Proper planning, monitoring, and skilled operators are essential to ensure successful outcomes in the sand casting parts.
Chapter 4: The Quality Control of Sand Casting parts
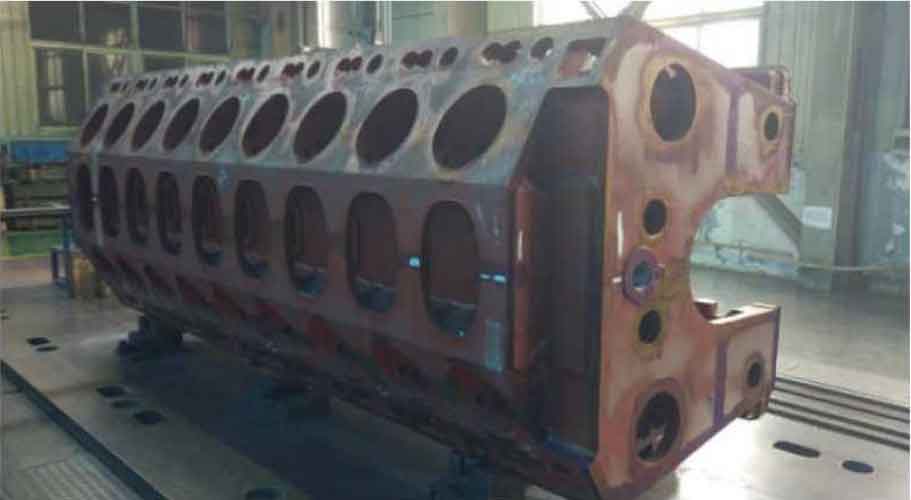
Quality control is crucial in sand casting parts to ensure that the final castings meet the desired specifications, structural integrity, and surface finish. Effective quality control measures help identify and address any issues that might arise during the casting process. Here’s an overview of quality control steps in sand casting parts:
Pattern and Mold Preparation:
- Pattern Inspection: Check the foam or other pattern material for accuracy, completeness, and any defects that might affect the final casting.
- Mold Integrity: Ensure that the mold cavity, cores, and gating system are properly assembled and aligned to prevent defects.
Metal Preparation and Pouring:
- Metal Composition: Conduct chemical analysis of the molten metal to verify that it meets the required specifications for alloy composition.
- Temperature Monitoring: Monitor the temperature of the molten metal during pouring to ensure that it is within the specified range for the casting material.
- Pouring Control: Maintain control over the pouring rate and sequence to prevent turbulence, metal splashing, and other pouring-related defects.
- Pouring Temperature: Ensure that the pouring temperature is appropriate for the specific casting material to achieve the desired mechanical properties.
Mold Filling and Solidification:
- Metal Flow and Venting: Check that the gating system, sprues, and vents are designed properly to facilitate smooth metal flow and escape of gases.
- Solidification Time: Monitor the cooling and solidification time to prevent premature mold breakout and shrinkage-related defects.
Casting Removal and Finishing:
- Mold Breakout: Carefully remove the sand mold to avoid damaging the casting. Inspect the mold for any residual sand or mold defects.
- Dimensional Inspection: Measure the dimensions of the casting to ensure that they match the intended specifications. Check for deviations and tolerances.
- Surface Inspection: Inspect the casting’s surface finish for defects such as cracks, porosity, inclusions, and surface irregularities.
- Finishing Processes: Evaluate the effectiveness of post-casting processes like machining, grinding, and surface treatment to achieve the desired final appearance and dimensions.
Non-Destructive Testing (NDT) and Documentation:
- Visual Inspection: Perform visual inspections to identify any visible defects or irregularities.
- Non-Destructive Testing (NDT): Utilize techniques such as radiography, ultrasonic testing, magnetic particle inspection, and dye penetrant testing to detect internal defects that might not be visible externally.
- Documentation: Maintain detailed records of the casting process, inspection results, corrective actions taken, and any adjustments made to the process.
Continuous Improvement:
- Root Cause Analysis: When defects or deviations are identified, perform root cause analysis to determine the underlying factors and implement corrective measures.
- Process Optimization: Continuously improve the casting process by analyzing data, identifying trends, and implementing adjustments to prevent defects.
Effective quality control in sand casting parts involves collaboration between skilled operators, inspectors, and engineers. Regular training, process monitoring, and feedback loops contribute to consistent, high-quality castings that meet the desired specifications and performance standards.
Chapter 5: The Application of Sand Casting Parts
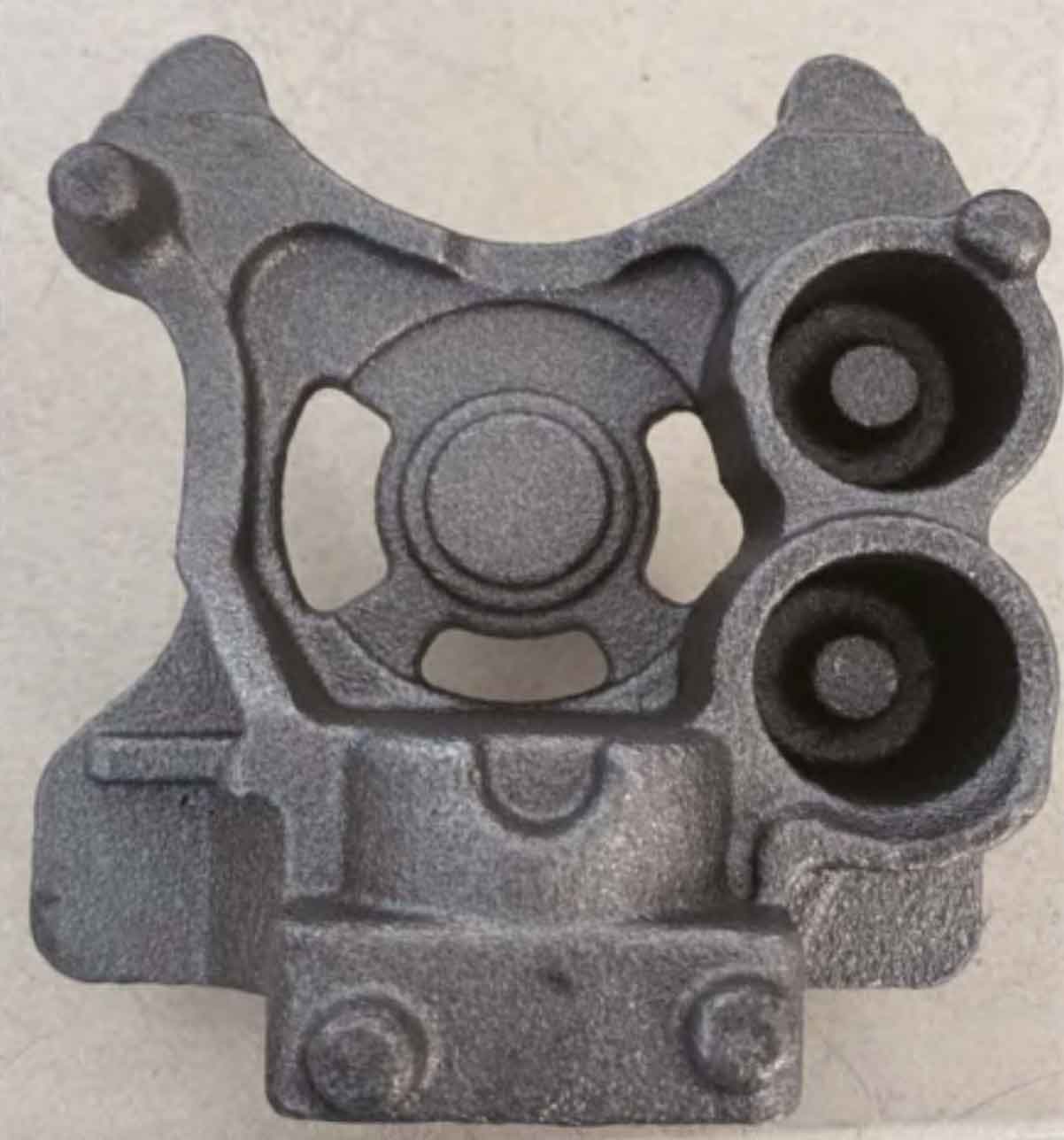
Sand casting parts are the widely used casting process that finds applications in various industries due to its versatility, ability to produce both small and large parts, and relatively low production costs. Here are some key application fields where sand casting parts are commonly used:
- Automotive Industry: Sand casting parts are employed to produce engine blocks, cylinder heads, transmission housings, brake components, and other automotive parts, particularly for prototypes and low-volume production.
- Aerospace and Defense: The aerospace sector uses sand casting parts for manufacturing aerospace engine components, structural parts, and other critical components that require specific alloys and complex geometries.
- Heavy Machinery and Equipment: Sand casting parts are used to create parts for heavy machinery, construction equipment, agricultural machinery, and mining equipment, including gears, pulleys, and housings.
- Oil and Gas Industry: Components for the oil and gas sector, such as valves, pump parts, and connectors, can be produced through sand casting parts.
- Energy Generation: Sand casting parts are used in the energy industry to manufacture parts for power generation equipment like steam turbines, hydroelectric turbines, and wind turbine components.
- Railway and Transportation: Sand casting parts are employed for producing railway components, including brake systems, couplings, and wheel hubs.
- Marine and Shipbuilding: Sand casting parts are used in shipbuilding to produce marine equipment components such as propellers, rudders, and ship fittings.
- Pumps and Valves: Sand casting parts are used to create parts for pumps, valves, and fluid control systems.
- Industrial Equipment: Sand casting parts are utilized in various industrial applications to produce parts such as pulleys, housings, and brackets.
- Art and Sculpture: Artists and sculptors use sand casting parts to create metal sculptures, artworks, and decorative elements.
- Architectural and Construction: Sand casting parts can be used for architectural hardware, decorative elements, and customized building components.
- Automated and Manual Equipment: Sand casting parts are used to create components for automated machinery, as well as manual tools and equipment.
- Historical Restoration: Sand casting parts are employed to replicate historical components, ornamental features, and architectural details during restoration projects.
- Prototype Development: Sand casting parts are valuable for producing prototypes of various parts before committing to more expensive production methods.
- Educational and Research Use: Sand casting parts are often used in educational settings to teach casting principles and in research to study metallurgical properties and processes.
Sand casting’s flexibility and ability to handle various alloys make it suitable for a wide range of applications, from industrial machinery to artistic creations. However, it’s important to note that while sand casting parts are versatile, it might not be the most suitable method for applications that require extremely tight tolerances or high-precision details.
Chapter 6: The Advantages and Disadvantages of Sand Casting Parts
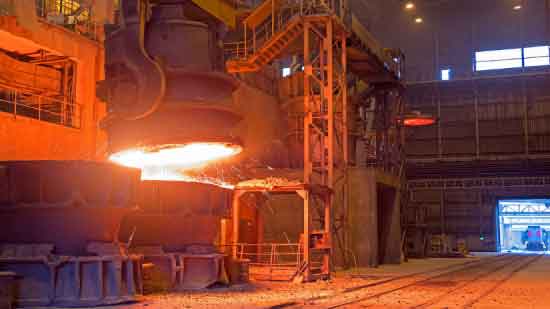
Sand casting, as a versatile and widely used casting process, offers several advantages and disadvantages. Here’s a breakdown of the pros and cons of sand casting parts:
Advantages:
- Versatility: Sand casting parts are suitable for a wide range of metals, including ferrous and non-ferrous alloys, making it applicable to various industries and applications.
- Complex Geometries: Sand casting parts can accommodate complex shapes, intricate details, and undercuts, making it suitable for parts with varying complexities.
- Low Cost: The initial tooling and equipment costs for sand casting parts are generally lower compared to other casting methods, making it cost-effective for small to medium production runs.
- Size Range: Sand casting parts can produce parts ranging from small to very large, making it suitable for a wide spectrum of part sizes.
- Tooling Flexibility: Patterns can be made from various materials, including wood, plastic, and metal, allowing flexibility in pattern construction.
- Quick Turnaround: Sand casting parts allows for relatively quick tooling setup and production, making it suitable for rapid prototyping and short lead times.
- Mold Reusability: Sand molds can be used multiple times, reducing material waste and lowering costs for subsequent production runs.
- Design Changes: Design modifications can be easily accommodated by altering the pattern, enabling flexibility during the development phase.
- Large Part Quantities: Sand casting parts can be used for both small batch and high-volume production, making it adaptable to different production demands.
- Surface Finish: Depending on the quality of the sand mold and the casting process, sand casting parts can produce satisfactory surface finishes without extensive post-casting machining.
Disadvantages:
- Surface Finish Variation: Achieving consistent surface finish can be challenging due to variations in mold preparation and molding techniques.
- Tolerances: Sand casting parts might not achieve the tight tolerances required for precision applications without subsequent machining.
- Porosity and Inclusions: Gas-related defects, such as porosity and inclusions, can occur due to the permeability of the sand mold.
- Surface Defects: Sand casting parts can result in surface defects like sand inclusions, surface roughness, and occasional mold-related defects.
- Mold Wear and Tear: Repeated use of sand molds can lead to mold degradation and dimensional inaccuracies over time.
- Environmental Impact: Sand casting produces sand waste, and the disposal and reuse of used sand can have environmental implications.
- Labor Intensive: The manual nature of mold preparation, pouring, and post-casting finishing can lead to higher labor costs.
- Limited Detail Replication: Extremely fine details and intricate features might not be faithfully replicated due to the nature of sand mold materials.
- Cooling and Solidification: Cooling and solidification times can be longer compared to other casting methods, affecting production speed.
- Health and Safety: Sand casting parts involves exposure to foundry materials, dust, and potential fumes, requiring attention to health and safety measures.
While sand casting parts have its limitations, it remains a valuable and accessible method for producing a wide variety of parts across different industries. The decision to use sand casting parts should be based on the specific requirements of the project, including size, complexity, cost considerations, and desired outcomes.
Chapter 7: The Environmental Protection and Sustainability of Sand Casting Parts
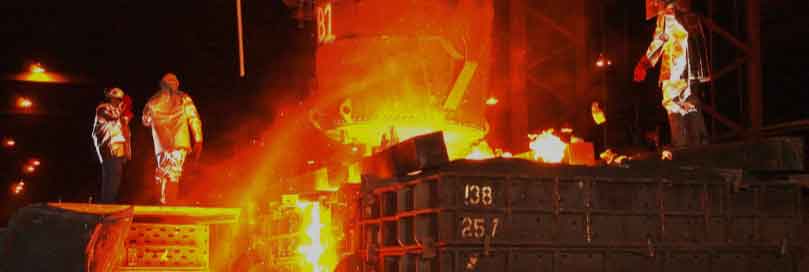
Sand casting, like any industrial process, has both environmental impacts and potential for sustainability. While it is a widely used casting method, there are considerations related to resource usage, waste generation, and energy consumption. Efforts have been made to address these concerns and improve the environmental profile and sustainability of sand casting parts. Here’s a look at the environmental protection and sustainability aspects of sand casting parts:
Environmental Concerns:
- Resource Usage: Sand casting parts requires large amounts of sand, which can lead to excessive consumption of this natural resource. Additionally, the production of molds and cores requires binders and additives, some of which can be derived from non-renewable resources.
- Waste Generation: Sand casting parts generates waste in the form of used sand and casting-related waste materials. Used sand, often referred to as “foundry sand,” can contain impurities and contaminants that may require proper disposal or treatment.
- Energy Consumption: The melting process in sand casting parts requires substantial energy input, particularly for metals with high melting points. This energy consumption contributes to greenhouse gas emissions.
- Emissions and Air Quality: The melting of metals in furnaces can release pollutants and emissions, including particulate matter, volatile organic compounds (VOCs), and carbon dioxide (CO2).
Sustainability and Environmental Protection Measures:
- Foundry Sand Reuse: One approach to mitigate resource usage is the reuse and recycling of foundry sand. Used sand can often be reclaimed and used in future molds after undergoing appropriate treatment and testing.
- Alternative Binders: Research is ongoing to develop alternative binders for sand molds that are more environmentally friendly, reducing the reliance on traditional chemical binders.
- Green Sand Systems: Green sand systems use water-based binders that are more sustainable and less harmful to the environment compared to traditional chemical binders.
- Efficient Furnace Operation: Improved furnace design, better insulation, and advanced heating technologies can increase the energy efficiency of melting operations.
- Emission Control: Modern furnaces are equipped with emissions control technologies, such as scrubbers and filters, to reduce pollutants released into the atmosphere.
- Waste Management: Proper handling, treatment, and disposal of waste materials generated during the casting process are important for minimizing environmental impacts. Recycling and reclamation of materials whenever possible can contribute to sustainability.
- Environmental Regulations: Adherence to environmental regulations and standards is essential for minimizing negative impacts. Many regions have regulations that govern emissions, waste management, and other aspects of foundry operations.
- Lifecycle Assessment: Conducting a lifecycle assessment of the entire sand casting parts can help identify areas of improvement in terms of resource usage, energy consumption, emissions, and waste generation.
- Research and Innovation: Ongoing research and innovation in materials, processes, and technologies can lead to more environmentally friendly casting methods and materials.
Efforts to make sand casting parts more environmentally sustainable involve a combination of adopting cleaner technologies, optimizing resource usage, minimizing waste, and adhering to environmental regulations. As industries focus on reducing their environmental footprint, advancements in sand casting parts methods and practices continue to contribute to improved environmental protection and sustainability.