Vacuum die casting is an advanced die casting technology, which can eliminate or reduce the defects such as air entrainment and air hole in the die casting die cavity and improve the mechanical properties and surface quality of the die casting parts. Vacuum die casting is a high near net forming process, which has the advantages of less pores, good surface quality, high elongation and high production efficiency. It is suitable for the production of high strength, high toughness, complex thin-walled structural parts, mainly used in the complex structure and key joints.
Technical advantages of vacuum die casting aluminum alloy parts:
(1) The lightweight effect of the car body is significant. Fully combining the technical advantages of aluminum alloy lightweight materials and vacuum die casting technology, more design ideas and methods are provided for the lightweight structure design of vehicle body. For example, the weight of the key structural parts of the body, such as the shock absorption tower, the front torsion box and the rear torsion box, can be reduced by 30% – 40% compared with the traditional steel assembly.
(2) Improve the overall performance of the car body. Aluminum castings can be used in complex structures to meet the energy transfer requirements of multiple dimensions during collision. When the front cabin module of the following car body is designed, as shown in figure (a), the front torsion box is die casting by vacuum, as shown in figure (b), which can improve the connection strength of the front longitudinal beam, the sill beam and the front wall lower crossbeam, and effectively transfer the force of the front longitudinal beam to the sill beam and the front crossbeam through the “s” front torsion box during collision, so as to improve the collision safety performance.
(3) Integrated design of parts. The traditional steel shock absorption tower assembly is welded by 5-8 stamping parts, as shown in figure (a). Only one part is needed for vacuum die casting, as shown in figure (b), which significantly reduces the number of parts, reduces the one-time investment of tooling, and reduces the difficulty of dimensional accuracy control of the assembly.
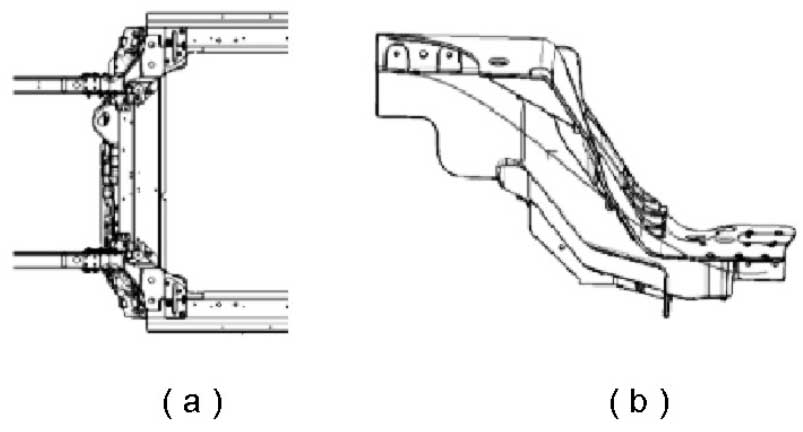
(4) Good body manufacturing technology. Due to the small number and size of internal pores, the mechanical properties and stress corrosion resistance of parts are balanced by solution and over aging treatment. Aluminum castings have excellent connection performance, which can be used in cold connection processes such as SPR (self piercing riveting), FDS (flow drilling screw), press riveting, pull riveting, etc., or in fusion welding such as MIG, CMT (cold metal transition arc welding).
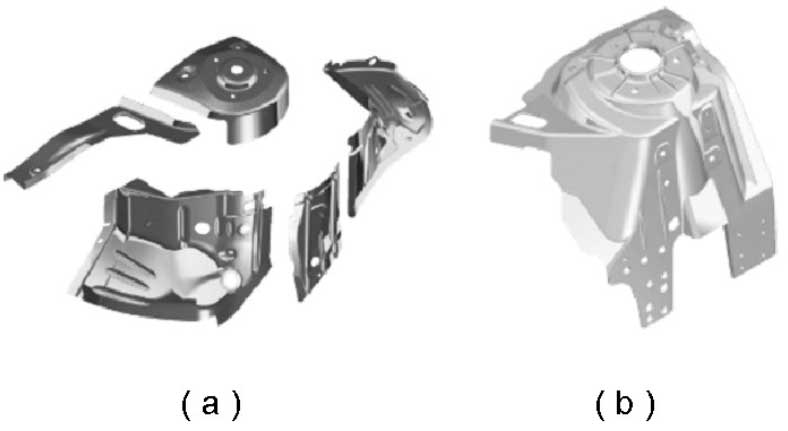
The basic requirements and optimization suggestions for the structural design of vacuum die casting aluminum alloy parts are described in combination with the part design practice as follows:
(1) Selection of aluminum alloy materials. Die casting aluminum alloy is required to have good fluidity, high-speed filling capacity, small linear shrinkage, fast cooling and easy demoulding characteristics, with good heat treatment performance. Common aluminum alloy materials are shown in Table 1. Al Si 10mg Mn is a very ideal vacuum die casting aluminum alloy, which can be applied to the body structure parts with high stress, high load and high toughness.
(basic mechanical properties of vacuum die casting materials: Rp0.2 > 120 MPa, RM > 180 MPa, A50 > 10%)
(2) Wall thickness of the main part. According to the function and stress conditions, the material thickness range of the main part is 3mm-5mm; the minimum wall thickness of the stiffener is 2.5mm, too small wall thickness is easy to cause defects such as cold separation, insufficient filling and difficult demoulding. The maximum material thickness of the key stressed parts shall not exceed 8mm. If the local material thickness is too large, it is easy to produce hot spots. There are shrinkage porosity, shrinkage cavity and other defects in the parts, and the mechanical properties of the materials are greatly reduced.
(3) Part draft angle. In order to make demoulding easier, the larger the draft angle is, the better. Generally, the draft angle ≥ 3 °, the minimum draft angle of stiffener and stiffener = 1 °, too small the draft angle makes demoulding difficult, the surface of parts is scratched, the mold is worn, and the service life is reduced. In order to prevent the die from being scoured by aluminum liquid, the draft angle at the root of rib plate shall be ≥ 3 °, and the fillet radius shall be ≥ 6mm.
(4) Minimum fillet radius of the part. The minimum fillet radius r of the part is equal to the equivalent material thickness of the adjacent area, too small fillet radius is not conducive to metal filling and gas discharge, local stress concentration cracking at the small radius sharp corner, mold wear is too fast.
(5) Optimization of ejector number and distribution. Ensure that the number of thimbles is sufficient and evenly distributed to prevent the deformation of parts, die sticking and crack at thimble caused by insufficient or uneven distribution of thimbles during part demoulding.
(6) Thread hole plus wire thread sleeve. When there are strength requirements for bolt connection and there is possibility of repeated disassembly and assembly during use, the use of steel wire thread sleeve for threaded hole can effectively increase the strength and service life of connection point. It is applied to the repair of bolted connection.
(7) Optimization of part structure by finite element analysis: using structural topology optimization and safety CAE analysis, the key structures such as part material thickness and stiffener are optimized. Through the optimization of finite element analysis, the maximum plastic strain of the front torsion box is reduced from 47% to 17%, as shown in the figure.
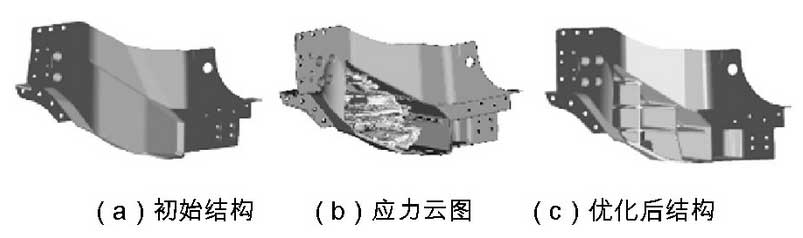
With the development of new energy vehicles, the development and application of aluminum alloy vacuum die casting parts have a very large market. However, the research time of high strength and toughness vacuum die casting aluminum alloy material and technology in China is short, and there is still a big gap between China and foreign advanced enterprises. In order to prevent foreign die casting enterprises from monopolizing the domestic market, China’s die casting industry should do more basic and applied research in the fields of high strength and toughness aluminum alloy, vacuum die casting technology and equipment.