Al-Cu system cast aluminum alloy is the earliest used casting alloy, which has high heat treatment effect and thermal stability. It is suitable for casting parts at high temperature, but its casting performance is poor, its corrosion resistance is not good, and its linear expansion coefficient is also large. Therefore, the Al Cu system alloy can be used for some heat-resistant castings with small volume and simple shape. The heat-resistant temperature of this series of alloy is 300 ~ 350 ℃. ZL205A, zl207, zl208 (China) and foreign alloys rr350 (UK), a д P1 (Russia), a201.0, 206 (US) have been used in the manufacture of engine parts, such as cylinder, cylinder head, piston and cylinder head.
At present, scholars at home and abroad have carried out a lot of related work in the research of high temperature properties of Al Cu alloys. Due to the coarsening of metastable phase θ′ in Al Cu alloy at high temperature, the high temperature mechanical properties and creep resistance of the alloy decrease. Therefore, generally, adding elements such as SC, Zr, re (such as Er, La, etc.) in Al Cu alloy increases the number of θ′ precipitates, reduces their size and produces coherent precipitates to improve the heat resistance of the alloy. As a trace addition element, the co lattice al3sc phase precipitated in the Al based alloy can strongly pin dislocation and grain boundary, stabilize the substructure of the alloy, significantly refine the grain and improve the strength of the alloy. However, due to the high price of SC, the application range of Al Cu alloy containing SC is limited.
In recent years, researchers have found that the addition of a small amount of Er to Al Cu alloy can form al 3er phase which is coherent and semi coherent with the matrix. This phase is similar to the heat stable al 3sc of type L12. It can refine the as cast structure of the alloy, improve the thermal stability, hardness and strength of the alloy. The results show that LA can significantly increase the number of θ′ precipitates and reduce their size, and improve the aging strengthening effect. After adding 1% (mass fraction) La to al-6% (mass fraction) Cu alloy, the precipitated al11la3 phase can effectively inhibit grain boundary sliding and limit dislocation movement, The creep properties of the alloy are increased by 3 ~ 5 times than that of the alloy without La addition.
The creep properties of the cast Al Cu alloy with PR and its oxides were studied experimentally. The results show that PR and its nano oxides can reduce the size of θ′ phase and increase the number of θ′ phase, and al11pr3 phase with excellent thermal stability can be precipitated at the boundary and dendrite edge, which can inhibit the migration of the boundary and the movement of dislocations during the creep process. Under the same creep conditions, The creep rate of the alloy without PR element is 4 times of that of the alloy with PR element. The time strain creep curve is shown in the figure. The same effect can be obtained by adding nano prxoy particles into the alloy.
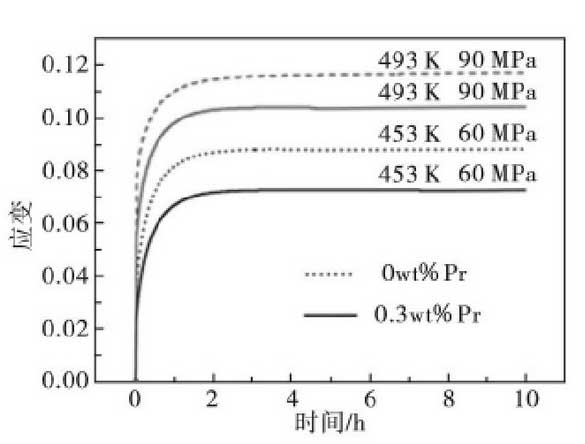
211z. X heat-resistant, high-strength and toughened aluminum alloy is a kind of Al Cu alloy with Ti, Zr, re and other elements. TiB2 is the most important casting refining agent when Ti and B are added at the same time. Zr and Al can form fine and dispersed intermetallic compound particle Al3Zr, which effectively hinders recrystallization and grain growth. The addition of appropriate amount of re to aluminum alloy can play the role of modification, refining, purification and microalloying. After adding these elements, the tensile strength of the alloy at room temperature is about 500 MPa, the elongation is up to 10%, the hardness is up to 165 HBW, and the strength is not less than 130 MPa at 350 ℃.
The addition of a small amount of Ag to the Al Cu system alloy will result in the co lattice precipitation of Ω phase on the main slip surface α of the Al alloy, which can effectively prevent the dislocation sliding and greatly improve the mechanical properties of the material. At the same time, the phase also has high thermal stability. However, with the continuous development of automobile industry, Al Cu mg Ag alloy can not meet the performance requirements of engine more and more. Therefore, adding rare earth elements on the basis of Al Cu mg AG has become a trend of Al Cu alloy development.
Xiao Daihong et al. Studied the effect of rare earth element Ce on the structure and properties of Al Cu mg Ag alloy. The results showed that compared with Al Cu mg Ag alloy without CE, the size and density and volume fraction of Ω phase in Al Cu mg Ag alloy with CE were smaller, which indicated that CE could effectively increase the nucleation density and inhibit the growth rate of Ω phase, Moreover, CE can significantly reduce the diffusion rate of Cu in Al matrix, thus inhibiting the coarsening rate of Ω phase; in addition, some supersaturated CE atoms gather at the interface between Ω phase and matrix to reduce the free energy and improve the thermal stability of Ω phase.
At present, in the research of cast heat-resistant Al Cu alloy, scholars at home and abroad tend to add rare earth elements or transition metal elements which can form nano precipitates or reduce the coarsening rate of Ω phase and θ′ phase, It is hoped that the nano precipitates formed by this element can significantly bind dislocations and grain boundaries and effectively inhibit the growth rate of the main thermally stable phases (such as ω phase and θ′ phase). According to this principle, the progress of deformation heat-resistant Al Cu system alloy is great, and the results are relatively remarkable. Now people are trying to apply the heat-resistant mechanism of deformation heat-resistant Al Cu system alloy to cast Al Cu system alloy, in order to obtain similar high-temperature strengthening effect.