Al-Si series alloy is the most widely used alloy system with the most varieties in cast aluminum alloy, and there are relatively more researches on high temperature properties, mainly including the following two categories:
(1) The Al Si mg and Al Si Cu systems used in engine cylinder and cylinder head are 319, A380, A356 (USA), etc;
(2) The eutectic Al Si Cu mg system and hypereutectic Al Si Cu mg system used in engine piston are m124, m142, m174 (Germany), ZL117, yl117 (China), A390, A393 (United States), etc.
The addition of Mg to Al Si alloy can age precipitate Mg2Si phase and improve the room temperature strength of the material. As the thermal stability temperature of Mg2Si phase is about 180 ℃, the heat resistance of cast Al Si Mg alloy is low, and its working temperature is generally lower than 185 ℃. Haghdadi et al. Studied the high temperature rheological behavior of cast Al Si Mg alloy. It was found that the spheroidization of Si particles and the coarsening or dissolution of Mg2Si precipitates at 400 ~ 450 ℃ resulted in the high temperature softening of the alloy. The Al 2Cu phase precipitated by aging after adding Cu into the Al Si system alloy has a thermal stability temperature of about 225 ℃, which can improve the high temperature strength of the material. E. R. Wang et al. Studied the mechanical properties of eutectic Al Si Cu Fe Mn alloy at room temperature and high temperature. After T6 heat treatment, the tensile strength of the alloy was 336 MPa at room temperature, 144.3 MPa at 300 ℃, and the precipitation of α – Fe (al15 (Fe, Mn) 3si2) and copper rich phase (al2cu) was the main reason for the improvement of the mechanical properties at room temperature and high temperature. This conclusion is consistent with the research results of Hiroyuki toda et al. It shows that the precipitation of al2cu phase with good thermal stability is the main reason why Al Si Cu system aluminum alloy can be used at about 200 ℃.
The overall high temperature strength level of Al Si Cu system and Al Si mg system cast aluminum alloy is not high, generally working below 225 ℃. When the working temperature exceeds 225 ℃, cast Al Si Cu mg system aluminum alloy should be used, which is mainly used in engine piston, so it is also called piston aluminum alloy. The results show that the Ni rich intermetallic compounds such as al3ni, al3cuni and al7cu4ni are mainly formed after the addition of Ni element in the Al Si Cu mg system alloy, while the al3cuni phase is the significant contribution to the high temperature strength. The tensile strength of the alloy at 350 ℃ is about 62mpa. By changing the content of Cu element in the Al Si Cu Mg Ni system alloy, It was found that with the increase of Cu content (2.63% ~ 5.45% (mass fraction)), the tensile strength of the alloy increased from 78.1mpa to 93.5mpa at 350 ℃, and the tensile strength at room temperature decreased first and then increased, because the al3cuni phase increased with the increase of Cu content.
Therefore, the al3cuni with reticular and semi reticular structure in the alloy matrix has an outstanding contribution to the high temperature mechanical properties of the cast Al Si Cu Mg Ni alloy. Australian Z. ashhar et al. Studied the room temperature and high temperature properties of Al-12Si, al-12si-ni, al-10si-5cu-1 ~ 2Ni and other cast aluminum alloys by using advanced 3D characterization methods such as synchrotron radiation, and put forward the high temperature strengthening mechanism of Al Si system alloy, which regards Al Si Cu Mg Ni system cast aluminum alloy as a metal matrix composite with eutectic Si and aluminum containing intermetallics as reinforcement phase, The physical and mechanical properties of the alloy are affected by the morphology and volume fraction of these reinforcing phases, as well as the degree of overlap between the eutectic Si phase and the intermetallic compound containing aluminum. The larger the specific surface area of the contact surface, the length width ratio of eutectic Si phase and the volume fraction of al7cu4ni and alsifenicu intermetallics, the better the room temperature and high temperature strength of the alloy.
Korean scholars have studied the fatigue and creep properties of cast Al Si Cu mg and Al Si Cu Mg Ni. It is found that in Al Si Cu Mg alloy, with the increase of Cu content, the yield strength of 100-300 ℃ decreases from 26.7 × 10-6 ℃ – 1 to 23.7 × 10-6 ℃ – 1250 ℃ from 120 MPa to 186 MPa, The changes of elastic modulus, mechanical properties and fatigue properties are related to the precipitation and growth of al2cu. In Al Si Cu Mg Ni system, with the increase of Cu and Ni content, the thermal expansion coefficient of 100-300 ℃ decreases from 23.6 × 10-6 ℃ – 1 to 21.6 × 10-6 ℃ – 1, the elastic modulus of 25-400 ℃ increases by 5gpa, and the creep fracture time increases from 2.8h to 23.8h (creep temperature 250-400 ℃, creep stress 20-130 MPa), The stress index n increased from 5.3 to 6.6, and the deformation activation energy increased from 269kj / mol to 311kj / mol. the reason for the above performance changes is that the addition of Ni and Cu precipitates the high temperature stable Al3 (Ni, Cu) 2 phase and the stable fenial intermetallic compound at 350 ℃, which improves the physical and mechanical properties of the alloy. The main controlling factor of the creep rate of cast aluminum alloy at high temperature is lattice diffusion, For example, the movement of vacancy, grain boundary sliding and dislocation climbing at grain boundary, the thermal stable phase can improve the creep performance of the alloy by forming dislocation wall and increasing the creep activation energy.
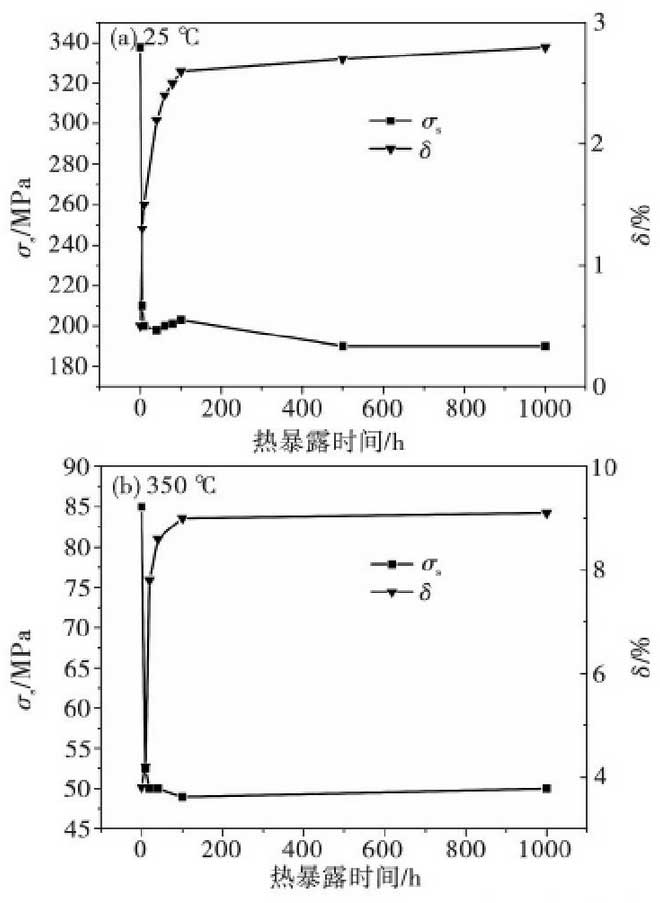
The Al Si Cu Ni Mg (m142) alloy developed by Mahler company in Germany has good tensile properties, creep resistance and casting properties. The tensile strength of m142 alloy under gravity casting reaches 100 MPa at 350 ℃, which has been widely used in automobile engine piston. However, under the coupling action of engine high temperature environment and thermal mechanical load, the structural instability and the significant decrease of strength with the extension of service time are the bottleneck problems faced by the cast aluminum alloy. Li Jianping et al. In China studied the high temperature endurance strength and structure stability of m142 alloy, and obtained the change curve of mechanical properties of the alloy before and after heat exposure (as shown in Figure 2). The results showed that under the coupling effect of high temperature environment and thermal mechanical load, with the extension of service time, α – Al grains grew gradually, The high temperature strengthening phases (al2cu, Mg2Si and al7cu4ni) gradually dissolve or coarsen, and the segregation of Al3 (CuNi) 2 at high temperature results in a higher vacancy concentration, which leads to a significant decrease in the high temperature properties of the materials. The conclusion of Wojciech Kasprzak et al. In the Al Si Cu mg system alloy is similar to that of Wojciech Kasprzak et al. They think that the addition of elements with smaller high-temperature diffusion coefficient and the aging precipitation of nano-sized coherent phases (such as Al3 (Zr, V, Ti)) can slow down the trend of high-temperature strength decreasing with the extension of heat exposure time.
At present, in the research of cast heat-resistant Al Si alloy, scholars at home and abroad tend to add trace rare earth elements (such as CE, Gd, er, etc.) and transition metal elements (such as Ag, Co, Cr, y, etc.) to the alloy, hoping to reduce the stacking fault energy of the alloy system and form high-temperature stable nano coherent precipitates to improve the heat resistance of the alloy, but the progress is not very good. The lack of high-strength and heat-resistant cast aluminum alloy has become one of the main problems restricting the progress of engine industry technology in the world.