1.Application in automobile and motorcycle casting
As one of the main directions of piston blank production, squeeze casting has produced various kinds of piston with a diameter of 90-190mm in China. The first automobile factory has been engaged in piston production with squeeze casting for many years, which is the largest piston production enterprise in China. The 140 type squeeze casting piston with anti expanding sheet developed by the author for Dongfeng automobile has been tested by relevant departments of Dongfeng Automobile Company and reached the level of superior product.
The performance requirements of automobile brake cylinder block are relatively high. Most of the domestic similar products are metal mold casting or low-pressure casting, which leads to high rejection rate of products. The main cylinder holes are mostly blind holes, with large machining allowance, which wastes a lot of non-ferrous metals and machining hours, and increases the production cost. Since 1992, the author has successfully developed the brake main cylinder block of Isuzu, Xiali, BMW and other models with Squeeze Casting Technology (see Figure). After appraisal, all the performance indexes of the products have reached or exceeded the advanced level of the similar products in Japan, and have been put into production in large quantities.
In order to reduce the weight of the connecting rod and improve the performance of the air compressor, the squeeze casting aluminum alloy connecting rod has been applied in the air compressor of Dongfeng Motor Co., Ltd. and good economic and social benefits have been obtained.
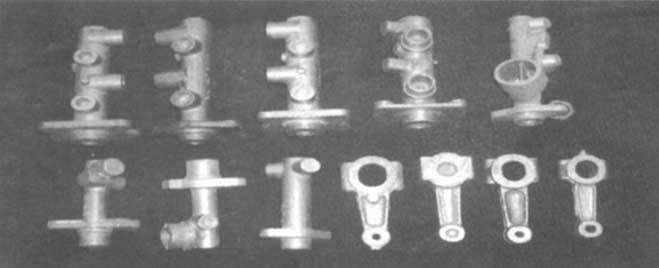
In China, motorcycle shock absorber casings are mostly produced by metal mold casting or low pressure casting process. The quality of castings is not stable, the rejection rate is high, the allowance of pouring riser is large, and the utilization rate of metal is low. By using squeeze casting to produce casings, non porous castings can be obtained, machining allowance can be reduced, material and power consumption can be saved, and mechanization and automation can be realized in mass production. Therefore, compared with other processes, squeeze casting process has obvious advantages.
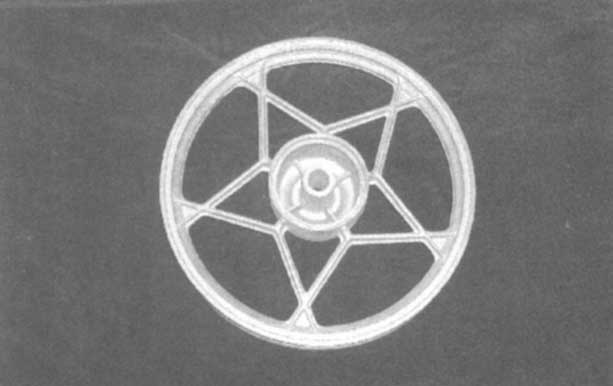
The production of motorcycle aluminum wheel hub in China started in the mid-1980s, and all of them adopt low-pressure casting (differential pressure casting), metal mold casting and pressure casting processes. In the early 1990s, extrusion casting of motorcycle aluminum hub was first developed by No. 52 Institute. At present, the production of motorcycle aluminum hub by squeeze casting technology has a strong competitiveness. The production capacity of extrusion casting motorcycle aluminum hub in China has accounted for more than 1 / 3 of the production capacity of aluminum hub. Figure 2 and Figure 3 are respectively extrusion casting motorcycle aluminum hub and automobile aluminum hub.
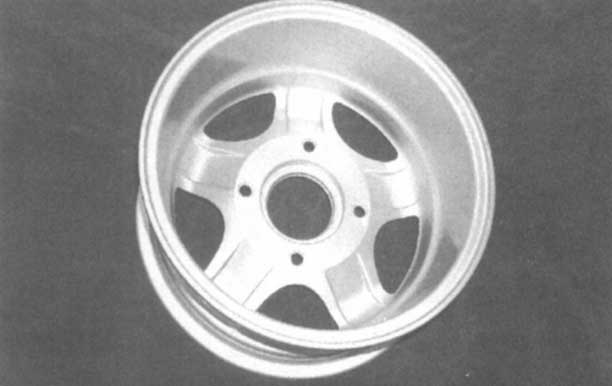
In addition, there are many parts of automobile and motorcycle produced by squeeze casting, such as parts of air conditioning compressor, engine oil pipe, clutch cylinder, brake caliper, motorcycle shoe, governor, etc.
2.Application in national defense industry
For many years, the 52nd Research Institute of China’s Ordnance Industry Corporation has been committed to the application of squeeze casting in the ordnance industry. It has successively developed a batch of military products, such as the lower body of mortar, the body of bullet and the hood. The second stage rudder surface of missile is successfully developed by squeeze casting technology. The narrow production process of the product is forging blank, and then machining forming. The production process is complex, long cycle, and large waste of materials. The net weight of parts processed from blank 10kg is only 0.65kg, and the theoretical shape processing is difficult. It must be completed on the three coordinate CNC machining center machine tool, which greatly increases the production cost. By using squeeze casting, not only the problem of no machining is solved for the theoretical shape direct forming (only 0.8kg for the squeeze casting blank), but also the mechanical properties that the blank can reach the design requirements without quenching are solved, and the production cost is greatly reduced.
3.Application in composite casting
It has become one of the most common and effective methods to produce composite materials by squeeze casting. Under the action of extrusion pressure, the matrix and composite can be well combined, which makes the matrix infiltrate into the pre casting of fiber reinforced body, improves the wettability of fiber and matrix, and improves the bonding strength of fiber and matrix. For example, the aluminum matrix composite made of alumina (Al2O3) or aluminum silicate (Al2O3 ยท SiO2) short fiber by squeeze casting process has obvious improvement in wear resistance and high temperature (250-300 โ) strength performance, while the linear expansion coefficient decreases; the internal combustion engine piston made of composite material and matrix alloy has good combination, and can be processed with alloy steel cutter. In addition, the alumina short fiber reinforced aluminum matrix composite prepared by the direct extrusion process after liquid infiltration has a dense, uniform and fine deformation recrystallization structure with uniform fiber distribution and a large length diameter ratio, which can play a better role in strengthening the bearing capacity. Therefore, it has many advantages such as eliminating defects, strengthening matrix, improving fiber distribution and avoiding fiber breakage and damage in the forming process.
4.Application in ferrous casting
The research on squeeze casting of ferrous metals started later than that on squeeze casting of nonferrous metals. In the 1960s, the former research institute of mechanical science of the first Ministry of mechanical industry, Changchun Institute of Optics and precision machinery and other units carried out research on the squeeze casting of ferrous metals, and then stopped for various reasons. Qingdao Jimo casting and forging plant started the research of steel squeeze casting in 1978, and cooperated with Harbin University of technology in 1980 to successfully apply the technology to the production of steel flange, long diameter flange, front and rear end cover of motor and other shaped parts, and achieved good results. The quality of the castings is stable. More than 300 tons of steel castings are exported to Japan, Southeast Asia and other countries.