The sand cores in the inner cavity of the cylinder head produced by the coated sand process are (generally refers to the water jacket core, water channel core and oil pipe core). There are sand sticking defects on the surface of the inner cavity (generally refers to the water channel and oil channel) of the casting, especially the sintering (plugging) phenomenon in the narrow part of the inner cavity, which reduces the qualification rate of the casting and increases the risk of outflow of defective products (the cleanliness of the inner cavity exceeds the standard). In order to solve the sand sticking and sintering defects in the inner cavity, reduce the cleaning work of castings and improve the quality of castings. Generally, the methods of improving the surface fire resistance and compactness of the sand core and reducing the pouring temperature are used, but the defects of sand sticking and sintering are not fundamentally solved, and often accompanied by pore defects; Prepreg coating can effectively reduce the sand sticking defects at the root of the water jacket cavity, but the improvement of the sintering defects is not obvious; After two times of dip coating, manual touch-up is carried out. Although no sand sticking and sintering are formed, there are serious coating skins, so it is not easy to miss the inspection.

In view of the two casting defects of sand sticking and sintering in the inner cavity of the cylinder block, it is best to reasonably select the coating, which has both good anti sand sticking and anti sintering functions and reasonable permeability. On the premise of ensuring the quality, the one-time dip coating method is adopted to prevent the coating from inclusion of holes and coating skin.
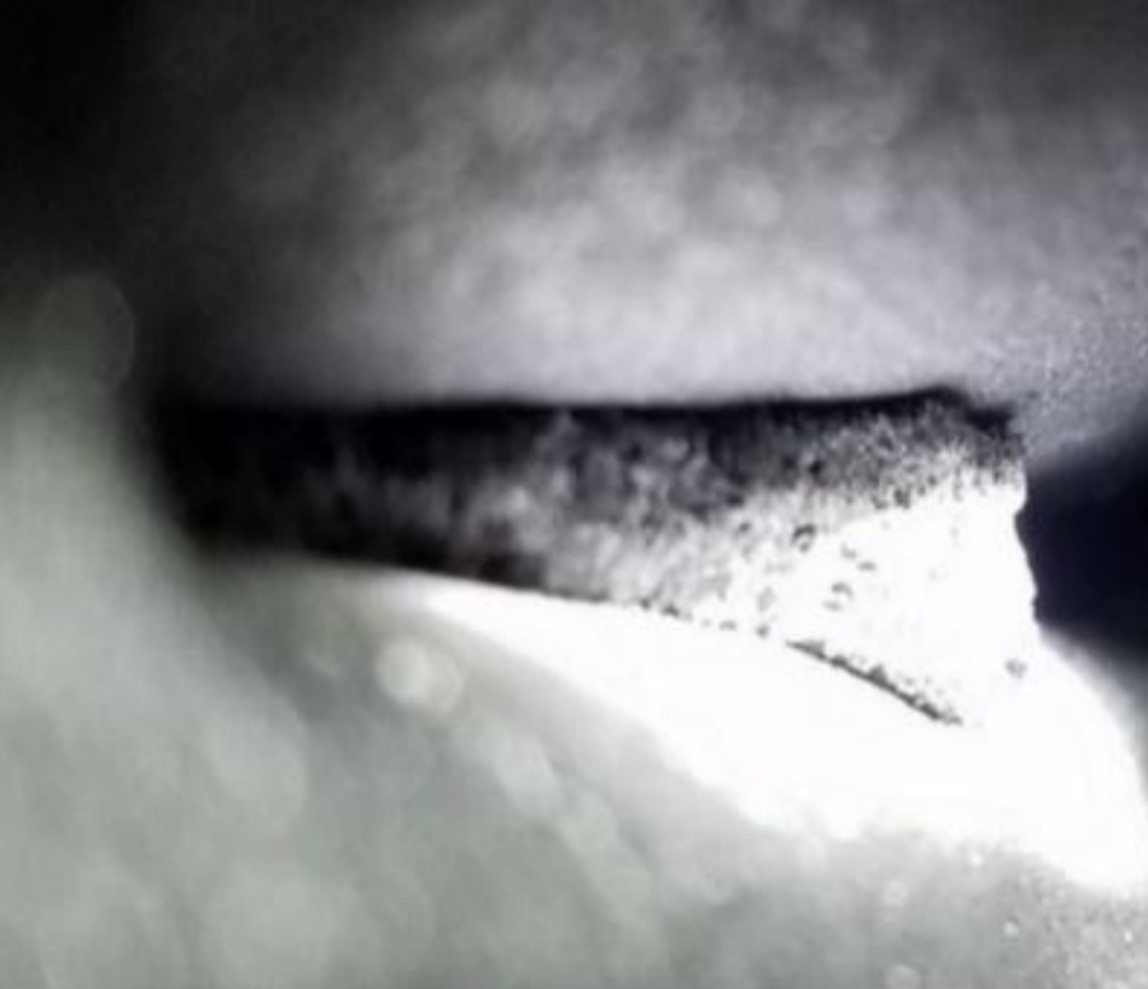
Corefon (Italy) m590a is a kind of anti sticking and anti sintering coating specially used for sand cores in the inner cavity of thin-walled and complex castings (such as water channel core, oil pipe core and tappet core of engine cylinder head).
After using the coating, no sand sticking and sintering defects were found in the inner cavity of the water jacket, and no other abnormalities were found on the surface of the inner and outer cavities of the casting (defects such as coating inclusion holes, coating skin, coating color, etc.) and the proportion of defects was greatly reduced. At the same time, the application of m590a in the overall core assembly of a cylinder head is also very ideal. The problem of veins in the cylinder head casting inlet (cold core, 70% quartzite +30% pearl sand) has been improved, and the veins have significantly reduced in size, which can be cleaned along the line. This proves that the m590a coating has a certain function of thermal insulation, which can alleviate the heating effect of the sand core (especially the thin and small parts) to a certain extent, It also indirectly supports the action mechanism of m590a coating on the sintering defects at the front end of the inner cavity of the cylinder water jacket.