
High wear resistance, high hardness and good toughness are important indexes of bimetal composite pipe, which are directly related to the service performance of pipe fittings. The wear resistance of the inner layer of 304 stainless steel outer layer and high chromium cast iron inner layer centrifugal cast composite pipe is more than four times that of 45 steel. This is because the hardness of M7C3 and martensite in high chromium cast iron is much higher than that of cementite and pearlite in 45 steel. The impact toughness can reach up to 200 j/cm2, the tensile strength is slightly lower than that of the outer layer, about 414 MPa, and the interfacial shear strength is 500 MPa. It has good bonding performance. In addition, the composite pipe can be modified by adding alloy elements in the centrifugal casting process, such as adding 0 005% ~0. 030% Bi can significantly reduce the adverse effects caused by the high silicon content and the decrease of chilling effect, and finally make the outer layer hardness reach more than 50HRC. The addition of Si, V and Ti to the composite pipe with carbon steel as the outer layer and high chromium cast iron as the inner layer can help to improve the mechanical properties of the composite pipe, and the effect of Ti is the most significant. In the process of centrifugal casting, because the composite tube has the characteristics of one-way heat transfer, that is, the heat of the wear-resistant inner layer is mainly dissipated from the interface to the outside through the outer layer, resulting in a certain directionality of the structure of the wear-resistant inner layer. Liujixiong et al. Observed the interface structure morphology of high chromium cast iron / carbon steel composite pipe. As shown in Figure 1, the carbon steel structure is a hypoeutectoid structure composed of a large amount of pearlite and a small amount of ferrite, and the high chromium cast iron structure is eutectic carbide, martensite and a small amount of residual austenite; The inner and outer transition areas are small, and the interface is composed of a layer of white tissue. The microstructure and thermal deformation behavior of the high chromium cast iron / carbon steel composite pipe were studied. The results show that good metallurgical bonding can be achieved by a small amount of mass transfer at the interface between the constituent steels. At the same time, it is also found that the composite pipe has four areas, namely, low carbon steel area (pearlite and ferrite), interface area, full pearlite area and proeutectoid ferrite / pearlite area. As shown in Figure 2, the structures of different areas determine their performance differences; In addition, the plastic deformation of bimetallic composite pipe is uneven due to the difference of hot working response.
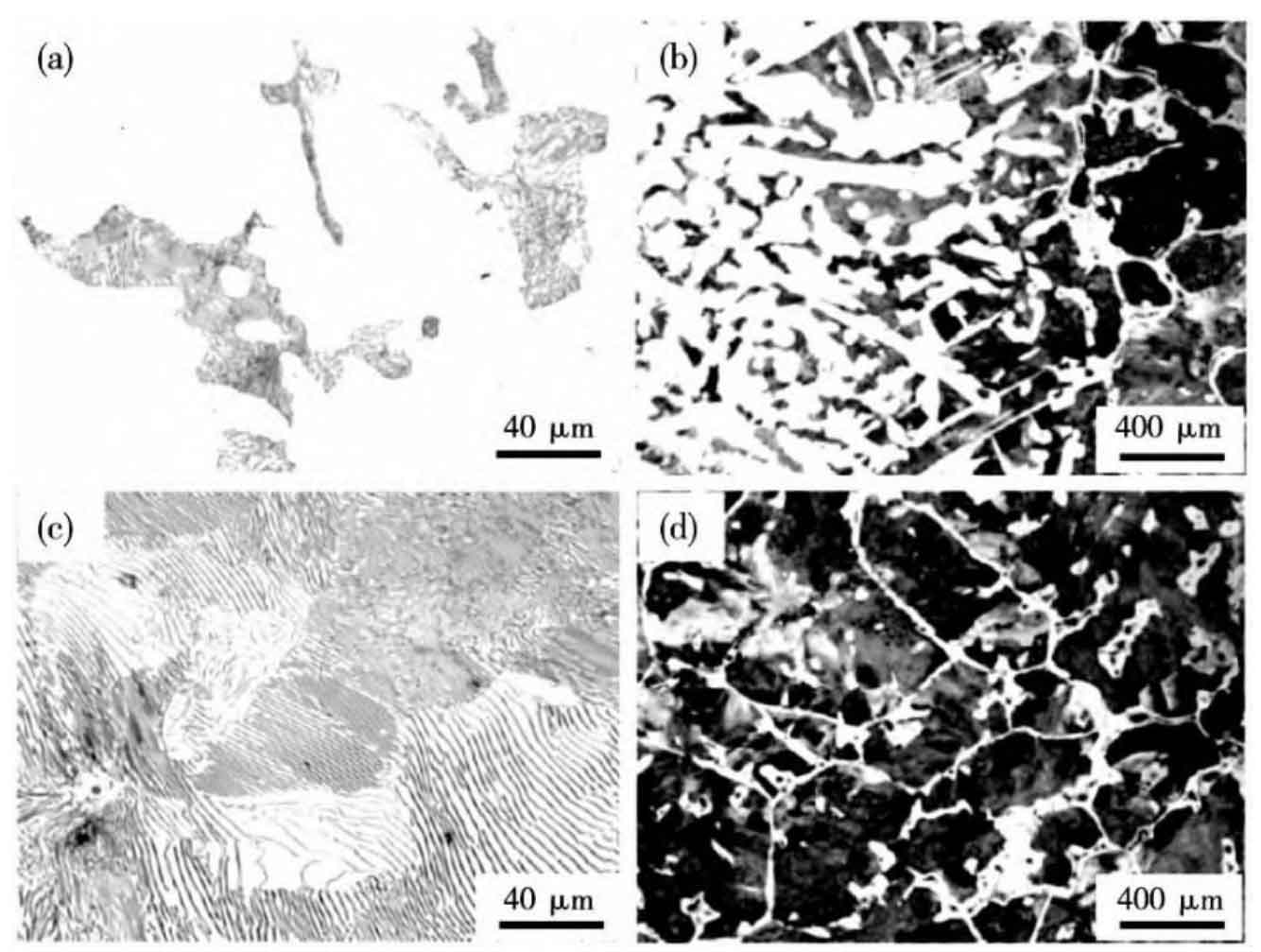
Heat treatment is also an important link to improve the bonding interface morphology and mechanical properties of bimetal composite pipes. Xiaohuazhao et al. Studied the phase change trend of bimetal sleeves with low carbon steel outer layer and high chromium cast iron inner layer during heat treatment. The results show that only the characteristics of high chromium cast iron need to be considered during heat treatment. Although air-cooled quenching can improve the mechanical properties of components, it is easy to cause cracking of sleeve parts due to the different thermal expansion coefficients of cast steel and high chromium cast iron; The bimetallic cylinder liners made of zg270-500 carbon steel in the outer layer and 17crmncu in the inner layer are subject to stepped heat treatment. For example, after holding at 260 ℃ for 1 hour, they are cooled and annealed in the furnace. After rough machining, they are heated to 980 ℃ for 3 hours and then air cooled. At this time, the inner layer is quenched and the outer layer is normalized, and then tempered. After annealing, the outer layer is mainly ferrite, and the inner layer is austenite and distributed with primary carbides, After quenching, the outer layer structure is ferrite + pearlite, the inner layer is transformed into martensite and secondary carbides are dispersed and distributed, and secondary carbides are precipitated along the grain boundary. The transition layer structure is uniform, and the inner and outer layers have achieved a solid metallurgical combination, which can not only avoid the occurrence of outer layer cracks, but also significantly improve the hardness of the inner layer (up to 64.7hrc after quenching). Therefore, It can be considered that quenching and high temperature tempering are the better heat treatment schemes for bimetal composite pipes at present. The hardness and shear strength of the outer 304 stainless steel / inner high chromium cast iron composite pipe were obtained by different heat treatment processes. The hardness transition zone was small, and obvious element diffusion occurred near the interface, as shown in Fig. 3 and Fig. 4. After heat treatment, high chromium cast iron has good wear resistance, and the hardness value at the composite interface is between high chromium cast iron and stainless steel (Fig. 3). Fig. 4 shows that the shear strength of the composite pipe after heat treatment is lower than that of as cast, and the interface shear strength after subcritical treatment is the lowest, because the physical parameters of the two materials are different, the thermal expansion and shrinkage are different during heating and cooling, and the interface cracks and stress concentration at the interface are serious. However, the shear strength of the bonding interface after quenching + high temperature tempering is higher than that under other heat treatment processes. The main reason is that the diffusion degree of C, Cr and Ni elements in the transition zone is increased during high temperature tempering, and a large number of alloy carbides are formed in the transition zone, which are mostly spherical and lamellar, and the amount of carbides is more than that of low temperature tempering, so the bonding strength of the interface is higher. Therefore, quenching + high temperature tempering is a suitable heat treatment process for 304 stainless steel / high chromium cast iron composite pipe.
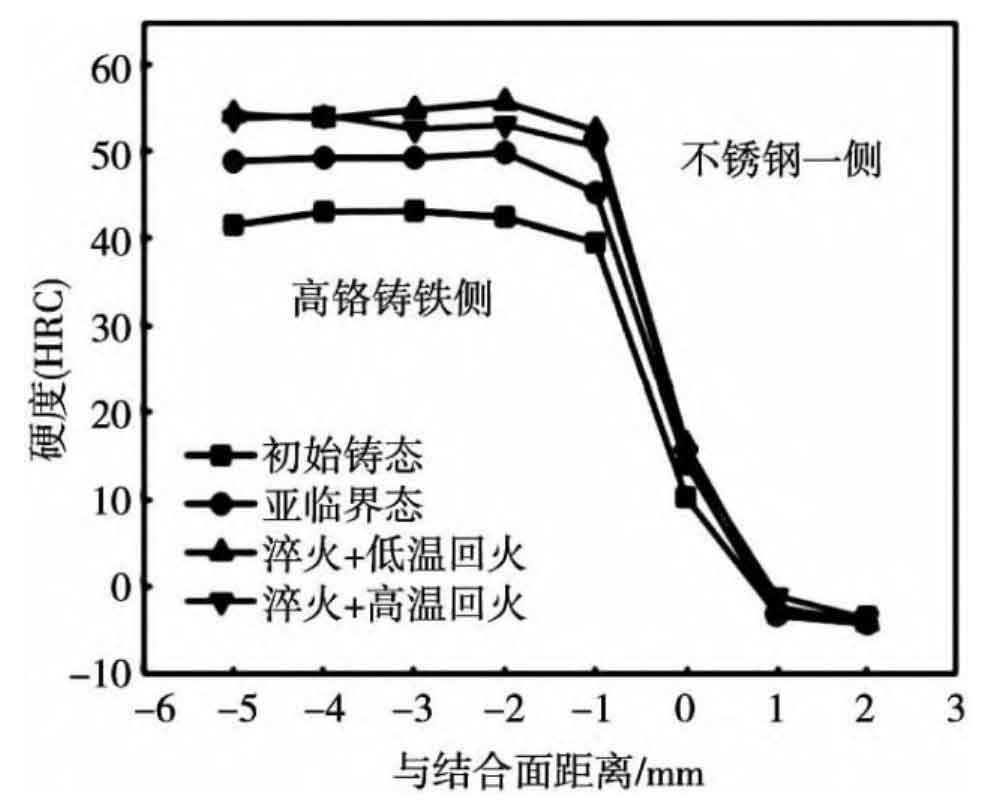
To sum up, at present, the research on bimetallic composite pipe mainly focuses on its mechanical properties and process parameter control, but the internal structure and interface element diffusion and distribution characteristics have not been thoroughly discussed. The following problems mainly exist: the analysis of the causes of the structure distribution and solidification segregation of the wear-resistant layer of composite pipe is not complete, and the research on the bonding interface of bimetallic composite pipe other than high chromium cast iron and carbon steel is still insufficient; Because the inner and outer materials are different, their thermal expansion coefficients are different, so their yield strength is different, which is easy to cause special residual stress; The centrifugal casting process is complex and the parameters are difficult to control. It is easy to cause problems such as excessive internal stress and internal shrinkage cavity, resulting in some problems in its application. Therefore, in the actual pouring process, in order to avoid cracks, shrinkage porosity and other defects, the following principles should be followed as far as possible: the pouring interval between inner and outer layers should be set strictly according to the casting temperature, and the low mold speed should be guaranteed as far as possible under the requirements of ensuring the mold filling quality of the casting.
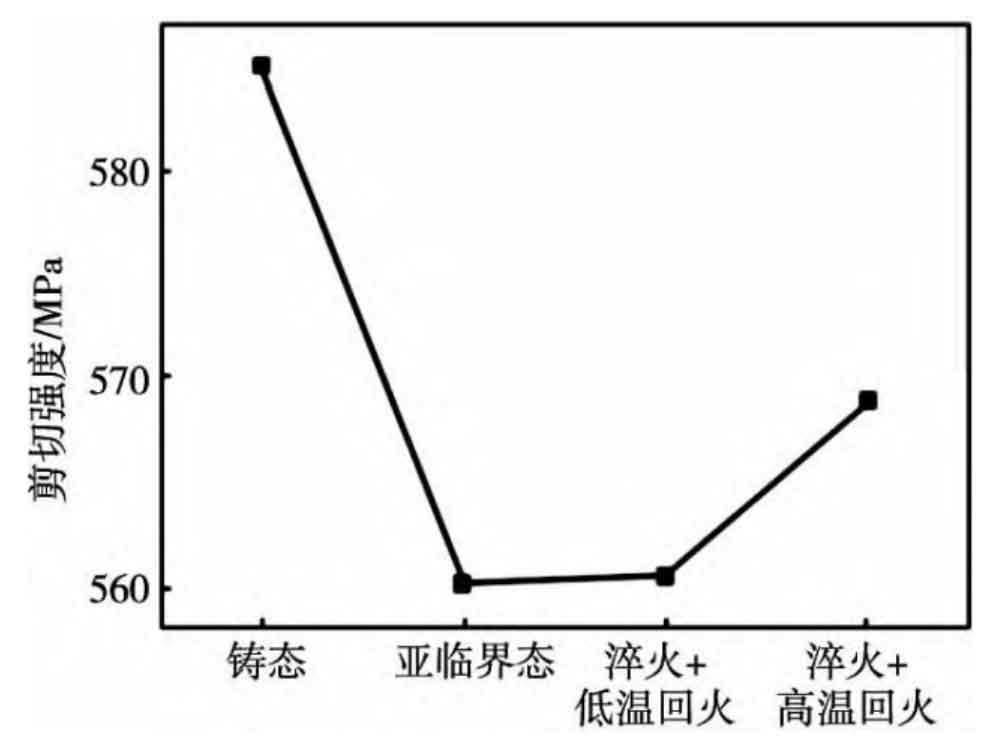