Abstract:
This paper compares the effects of exothermic pads and metallic pads in the production of duplex steel castings. With the aid of solidification simulation software, the performance of the designed exothermic pads was simulated and verified through pouring tests. The results indicate that EX5 BLEND exothermic material pads can replace metallic pads, reducing metal consumption and energy expenditure during pad removal while meeting feeding requirements, thereby significantly lowering production costs.
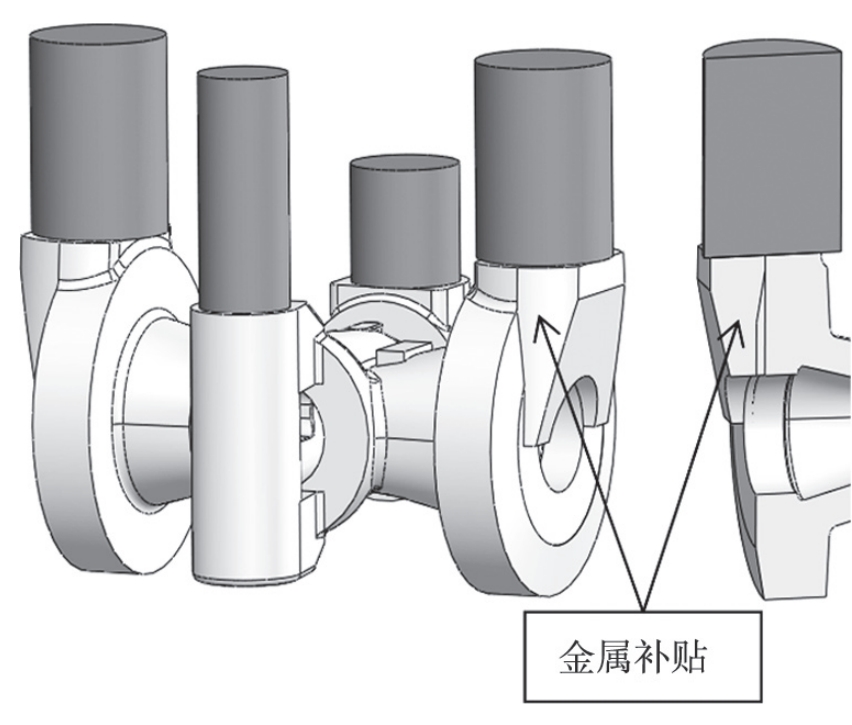
1. Introduction
In sand casting production, metallic pads are often used to extend the feeding distance of risers. However, these pads usually need to be removed, resulting in energy consumption for both the pad material and its removal, especially for high-alloy duplex steel castings, where this waste is substantial. The adoption of efficient exothermic pads can save metal material and reduce the energy consumption associated with pad removal, thereby lowering costs.
2. Materials and Methods
2.1 Material Selection
EX5 BLEND exothermic material was selected for production trials due to its superior exothermic and insulating properties compared to conventional materials.
Table 1: Comparison of Combustion and Insulation Curves
Material Type | Holding Time at 1147°C (min) |
---|---|
Common Exothermic | 2.25 |
EX5 BLEND Exothermic | 5.70 |
2.2 Casting Design
A gate valve body with dimensions of 830 mm × 500 mm × 440 mm and a gross weight of 540 kg, made of duplex steel ASTM A890 5A, was selected for the production trial.
Table 2: Comparison of Pad Designs
Pad Type | Dimensions (mm) | Theoretical Weight (kg) per Pair | Pouring Weight (kg) | Process Yield (%) |
---|---|---|---|---|
Metallic Pad | 270 × 260 × 90 | 70 | 1050 | 51.4 |
Exothermic Pad | 270 × 260 × 90 | – | 980 | 55.1 |
2.3 Simulation and Verification
Solidification simulations were conducted for both metallic and exothermic pad designs. The results indicated that the exothermic pad design could meet feeding requirements.
3. Production Process
3.1 Preparation of Exothermic Pads
The powdered exothermic material was mixed with a binder in the required proportion and prefabricated using a core box.
3.2 Molding, Box Closing, and Pouring
The exothermic pads were placed in the designed positions before molding, with attention paid to the placement of exhaust pipes to ensure smooth exhaust during the reaction of the exothermic material.
3.3 Inspection
- Surface Inspection: After shakeout, the castings showed no porosity, sand adherence defects, and a smooth surface close to the sand mold.
- Internal Quality Inspection: Radiographic testing revealed no defects in the flanges of both castings produced with metallic and exothermic pads.
4. Results and Discussion
4.1 Effectiveness of Exothermic Pads
The EX5 BLEND exothermic material pads could be initially evaluated through simulation software. Radiographic and visual inspections confirmed that the designed exothermic pads met the internal and surface quality requirements of the castings.
4.2 Cost Reduction
Replacing metallic pads with EX5 BLEND exothermic pads of the same size significantly improved the process yield of the castings, from 51.4% to 55.1%, reducing metal consumption, energy expenditure during pad removal, and other costs. Even after accounting for the cost of the exothermic pad material, a substantial reduction in production costs was achieved.
5. Conclusion
- EX5 BLEND exothermic material pads can replace metallic pads in sand casting production of duplex steel castings.
- The adoption of exothermic pads significantly improves the process yield of castings, reduces metal consumption and energy expenditure, and lowers production costs.
This study demonstrates the feasibility and economic benefits of using exothermic pads in the production of duplex steel castings in sand casting, contributing to the advancement of casting technology and cost reduction in the industry.