With the economic development of the country, all walks of life are developing rapidly, and the machinery industry is also growing steadily, especially the forklift industry. The demand for supporting oil cylinders for forklifts is also increasing gradually. In order to complete the production tasks on time and in quantity, it is required to improve product quality, production efficiency, and processing technology and tooling that are relatively lagging behind. G27z4 steering cylinder of our company is mainly used for Heli K series forklift. The processing quality and efficiency of casting cylinder head, which is an important part of cylinder, are not ideal and often become the bottleneck to complete the production task. The casting cylinder head was originally clamped by screw and pressing plate on the machining center with split type common tooling. The defects of this way are as follows:
1、 The product has strict requirements on form and position tolerance, with slight deviation, resulting in the two ends of cylinder head not on a horizontal plane;
2、 The manual clamping torque force is not enough, the clamping torque is different each time and the force size is related to the operator;
3、 The labor intensity is high, the operator needs to screw and loosen constantly, and adjust the height of the lower support rod to adjust the parallelism of the two end faces of the cylinder head;
4、 For a long clamping time, the operator needs to adjust constantly to ensure the parallelism of both sides of the cylinder head, which becomes one of the main factors restricting the improvement of processing efficiency.
For this reason, ZHY casting technical personnel combined with product characteristics and processing efficiency, used hydraulic principle and electrical design to carry out special design, and entrusted hydraulic fixture manufacturers to produce fully automatic clamping hydraulic fixture. After verification, the production efficiency was nearly doubled, and the stability of product quality was greatly improved. The labor intensity is greatly reduced. The hydraulic principle and electrical design are used for special design, and the hydraulic fixture manufacturer is entrusted to produce the fully automatic clamping hydraulic fixture. After verification, the production efficiency is nearly doubled, and the stability of product quality is greatly improved. The operator needs to adjust constantly to ensure the parallelism of the two ends of the cylinder head, which becomes one of the main factors restricting the improvement of processing efficiency.
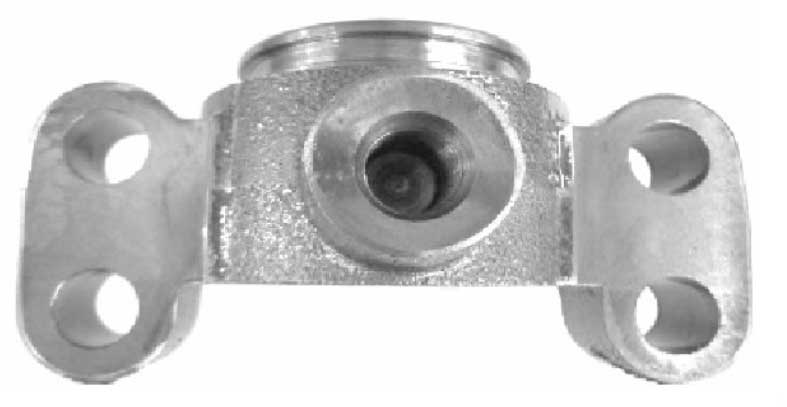
The average loading and unloading time of each cylinder head of the original old tooling is 72 seconds, and the qualified rate of product processing is 98%. Now the loading and unloading time of the hydraulic fixture is 42 seconds, the efficiency is improved by 42%, and the qualified rate of product processing is 99%. At the same time, the structure design of the hydraulic fixture is reasonable, the working process is fully automatic, the labor intensity is low, the working efficiency is high, and the workpiece processing stability and qualification rate are also improved a lot.
Forklift truck has a broad market in China, and it keeps a high growth every year. The corresponding forklift cylinder is also facing more demands of high quality and efficiency. As an important part of steering cylinder, casting cylinder head is widely used, and also in urgent need of capacity and efficiency improvement. The application of the full-automatic hydraulic fixture can improve the product quality and production efficiency without increasing the processing equipment, meet the production needs, and create greater benefits with less costs. Fully automatic hydraulic fixture has been recognized and welcomed by many operators in our company, and the company is also processing piston rod and other parts to apply and promote hydraulic fixture.