Al-Mg cast aluminum alloy is also known as corrosion-resistant cast aluminum alloy, which has the advantages of high corrosion resistance, strength, machinability and smooth surface. The heat resistance of Al Mg system cast aluminum alloy is relatively poor. Generally, SC element is added to improve its high temperature performance, but the cost of SC is very high at present. Therefore, Al Mg SC system alloy is only used in the field of aerospace and rocket manufacturing.
Some scholars have studied the structure and heat-resistant mechanism of Al Mg SC system alloy. They believe that the addition of SC refines the as cast structure of the alloy, affects the solute atom enrichment area at the liquid end of the dendrite front, and refines the dendrite. The al3sc formed by SC in Al Mg system alloy and the matrix structure is coherent (as shown in the figure). This phase can effectively pin dislocation and grain boundary at high temperature, and has high thermal stability. The addition of Zr or er to Al Mg SC alloy results in the formation of nano core-shell structure due to the different diffusion rate of SC, Zr and ER in Al matrix at high temperature, which reduces the cost of the alloy to a certain extent.
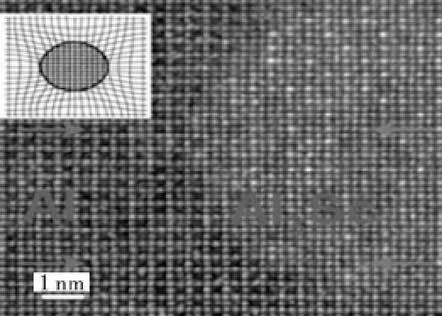
In the case that there is no great breakthrough in the research of composition optimization and heat treatment process of traditional cast heat-resistant aluminum alloy, researchers pay attention to the matrix reinforcement of traditional cast heat-resistant aluminum alloy. The matrix reinforcement function is to form reinforcement phase by adding elements or directly adding high-strength reinforcement materials to form composite materials. For example, the Al2O3 short fiber reinforced aluminum matrix composite piston developed by Shandong Binzhou Bohai piston Co., Ltd. [53] can effectively transfer the load from the matrix to the reinforced fiber, making the tensile strength of the material reach about 110 MPa at 350 ℃, and the elongation is about 0.9%.
Yang Zhong et al. Prepared SiCp Reinforced Aluminum Matrix Composite by small eddy liquid agitation method. The SiC distribution is uniform and the interface with the matrix is good. When the matrix contains 15% (volume fraction) SiCp, the tensile strength of the material reaches 213 MPa at 350 ℃. Australian g. requena et al. Studied the microstructure of short fiber reinforced alsi12cumgni alloy and its creep performance at 300 ℃. The results showed that during the creep process, diffusion led to the coarsening of eutectic Si and intermetallic compound, which increased the contact area between eutectic Si phase, intermetallic compound and short fiber, and enhanced the effect of load transfer from Al matrix to reinforcement phase, Thus the creep rate is reduced.