The steering knuckle is a chassis safety part, which has the functions of connection, bearing and steering, and the service conditions are complex. The prototype of an aluminum alloy squeeze cast steering knuckle is carried on the SUV. The original production process is nodular cast iron sand casting, with a mass of 4.5kg. The A356 aluminum alloy steering knuckle is planned to be produced by squeeze casting process. The strength of the preliminary structure is analyzed according to 8 typical working conditions of passenger car chassis parts, and the structure is optimized according to the CAE analysis results. Finally, the optimization model of aluminum alloy steering knuckle and the casting are shown in the figure, with a mass of 2.19kg, The relative weight reduction ratio of iron castings is 56.6%. The CAE analysis results of the steering knuckle under 8 typical working conditions show that the stress distribution meets the requirements and is less than the yield strength of 230MPa required by the technical conditions.
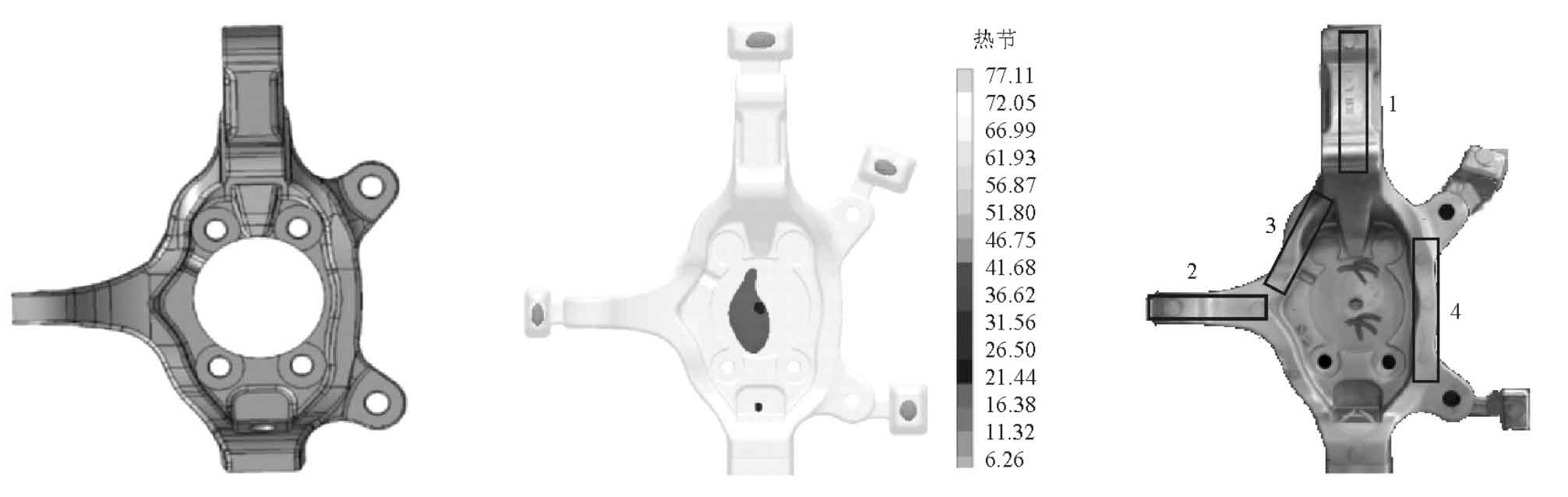
Hvsc-800pl horizontal squeeze casting machine is adopted, and indirect extrusion process is adopted in die design. Through the preliminary mold flow analysis of the extrusion process for the steering knuckle, it is found that the last liquid phase area in the solidification process is lower than the middle of the front wheel center of the part, as shown in Fig. B. the hot joint of the casting is also here, and there is the possibility of shrinkage cavity or porosity. In order to ensure stable mold filling and good feeding during solidification, the round hole connected with the hub in the middle is improved by water cooling and local extrusion. Due to the detailed design and analysis in the early stage, in the later stage of die test, in addition to opening an exhaust slot on the die and modifying the extrusion pin clearance, the whole trial production process was smooth.
The squeeze cast steering knuckle is treated with T6, the solid solution temperature is 530 ℃, the heat preservation is 8h, the water is cooled at 40 ℃, the aging temperature is 180 ℃, and the heat preservation is 6h. Samples are taken from the casting body to test the mechanical properties. The sampling position is shown in Fig. C. the material tensile property test results show that the material properties meet the design requirements.
The bench test is carried out after the sample of squeeze cast aluminum alloy steering knuckle is processed and assembled with the dual part. The test instrument is schenck160kn / 100mm hydraulic servo test equipment. The test parameters such as the magnitude, direction and loading frequency of the test loading force are the same as those of the original cast iron steering knuckle. The static strength and fatigue endurance test of the steering knuckle under typical working conditions are carried out, and the samples are free of cracks, deformation and other conditions, meeting the requirements.