Y can improve the comprehensive mechanical properties of cast high magnesium alloy, refine the microstructure of rolled magnesium alloy, and improve the high temperature mechanical properties and creep resistance of magnesium alloy.
1. Application of yttrium in AZ91 cast magnesium alloy
The properties of AZ91D magnesium alloy with y can be further improved by heat treatment at the same time. With the addition of Y and the content of Y less than 1% (mass fraction, the same below), the β phase with reticular structure of most dendrites in AZ91D cast magnesium alloy basically changes into granular β phase, that is, element Y has obvious refining effect on β phase, and a small amount of dark structure appears in magnesium alloy, That is to say, adding element Y to AZ91D casting magnesium alloy can refine the structure of the alloy strongly, and form square al6mn6y phase and rod al2y phase in the alloy. At the same time, the amount of β phase (Mg17Al12) in the alloy decreased and changed from the original network distribution to the broken network distribution, but when the Y content was more than 1.5%, the network structure appeared again. Adding a small amount of Y into AZ91D alloy can improve the mechanical properties of the alloy. When the Y content reaches 1.5%, the maximum tensile strength of the alloy reaches 184.83 MPa, and the maximum hardness of the alloy reaches 71.1. Compared with pure AZ91D, the aging peak hardness increased at 175 and 200 ℃ after adding y, and the aging peak appeared earlier with the increase of aging temperature. At the same time, because of the addition of Y, the peak aging time of the alloy is delayed compared with that of pure AZ91D.
2. Application of yttrium in mg Zn Zr cast magnesium alloy
The effect of Y on the microstructure and mechanical properties of mg-zn-y-zr cast magnesium alloy was studied. The composition of the alloy is mg-5.5% zn-xy-0.4zr. The content of Y in the alloy is changed. The microstructure evolution and recrystallization process of the alloy are observed by hot stretching at different temperatures. There are α – Mg and I-phase particles in 0.74% or 1.35% of the alloy with low y content, and α – Mg, I-phase and w-phase in the alloy with high Y Content and 1.72% y content. For the alloy with low y content, fine I-phase is formed during hot drawing, and these phases strengthen the alloy. The alloy with high y content does not form fine I-phase during hot stretching, and the XRD test results are shown in Fig. 3. However, w phase is not easy to change in this process. The strength of high y content alloy containing 1.72% y is higher than that of low y content alloy containing 1.35% y at low temperature. In the process of hot drawing, dynamic recrystallization takes place in all alloys.
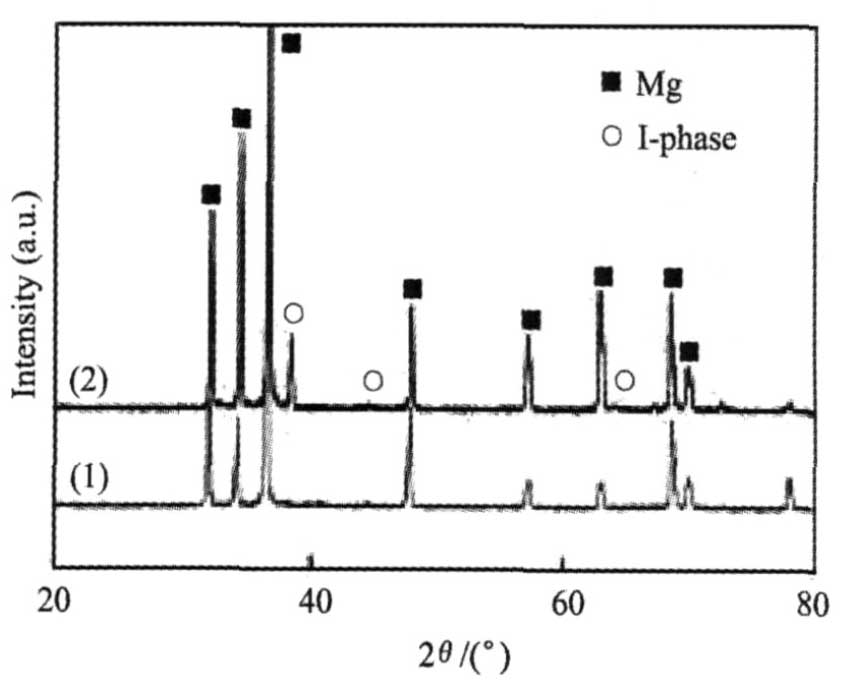
The results show that with the increase of re y, the tensile strength at room temperature increases, the elongation slightly increases, the tensile strength at 150 ℃ gradually increases, and the elongation gradually decreases. The mechanical properties of cast magnesium alloy AZ91 can be improved by adding appropriate amount of Y, which can meet the application requirements at high temperature. The tensile fracture is relatively flat and bright, and there is almost no section shrinkage at the fracture, and the fracture type should be brittle fracture. After adding 1% y, the as cast microstructure and mechanical properties of magnesium alloy AZ91 are refined, which can meet the application requirements at high temperature.
Adding 3% Ca and 2% Zn to mg-5% y alloy and mg-10% y alloy respectively, P / M alloy was prepared by rapid cooling. The samples were solidified under cold pressing and hot extrusion conditions. The solid y distributed on Mg matrix was obtained in the rapidly solidified Mg-Y binary alloy. The fine crystal structure of 400 nm was found in the rapidly solidified samples of the ternary alloy. The hardness of the rapidly solidified sample containing 10% y heated to 473k increases gradually due to the existence of β phase. There are various compounds in the remelting sample of P / M alloy, mg24y5 in binary alloy, mg24y5, mg2ca, mg12yzn in ternary alloy. No obvious softening sign was found in the tensile test of mg-10% y, mg-10% Y-2% P / M alloy quenched at 573K. The highest strength of mg-10% Y-2% P / M alloy is 520 MPa at room temperature and 440 MPa at 473k. At 573 K, the strength of all P / M alloys decreased below 80 MPa.
3. Application of yttrium in mg Zn Zr hot rolled magnesium alloy
The effect of Y element on the microstructure and properties of mg-4.9zn-0.9y-0.7zr and mg-4.9zn-0.7zr alloy plates prepared by unidirectional hot rolling process was studied. The results showed that y effectively refined the as cast microstructure of mg-4.9zn-0.7zr alloy, and improved the tensile strength and yield strength of mg-4.9zn-0.7zr alloy. The main strengthening mechanism was the second phase strengthening.
The mechanical properties of magnesium alloy were observed by self hardening sand mold. The microstructure of extruded magnesium alloy containing Li and Y is not different from that of solid-state dissolved magnesium alloy, but the tensile properties of the column base surface of extruded magnesium alloy are significantly higher than those of other directions (i.e., the normal direction and rolling direction, {C + a}), and the alloy has higher ductility than pure magnesium. The deformation mode of {C + a} can provide more deformation ability, that is to say, the deformation in the direction of C can be carried out inside the grains.
4. Application of yttrium in mg-9al-1si cast magnesium alloy
Mg2Si, the main strengthening phase in mg-9al-1si alloy, is distributed around the grain boundary in the form of thick Chinese characters. Under stress, the interface between the Chinese characters and the matrix is prone to produce microcracks, which reduces the tensile strength, plasticity and other mechanical properties of the alloy. The microstructure of mg-9al-1si alloy was refined obviously after adding a small amount of Y into the alloy. The morphology of Mg2Si strengthened phase changed from coarse Chinese characters to fine, dispersed particles. With the improvement of microstructure, the mechanical properties of mg-9al-1si alloy at room temperature and high temperature are improved to a certain extent, and the creep resistance of mg-9al-1si alloy is obviously improved, as shown in the figure.
Due to the addition of Y, the bar like al11y3 phase in the grain boundary is strengthened. The joint action of Mg2Si and al11y3 prevents the grain boundary from sliding during high temperature creep. With the increase of Y addition, the high temperature creep resistance of the alloy is improved. At the same time, the mechanical properties of the alloy are improved due to the change of the morphology of Mg2Si. When the addition of Y exceeds 0.6%, The high temperature properties of mg-9al-1si magnesium alloy are better than that of ae42.
5. Application of yttrium in mg Zn Sn cast magnesium alloy
The structure of mg Zn Sn cast magnesium alloy is unstable at high temperature, which limits its application. Adding alloy elements to mg Zn Sn cast magnesium alloy to form high temperature phase (HTP) can increase the structural stability of the alloy. In this paper, the microstructure evolution of mg Zn Sn cast magnesium alloy after heat treatment by adding y and Sb was studied. The results show that the existence of HTP prevents the recovery of dislocations, hinders the movement of dislocations in the solid fusion, and forms substructures and sub grains of 20-30 μ M. during aging, the grain boundaries of sub grains are pinned by HTP particles, and strengthened by two precipitation phases, mgzn2 and mg2sb. The precipitation phases are generated at the grain boundaries and sub grain boundaries, The pinned sub grain structure provides high structural stability for the alloy at high temperature.
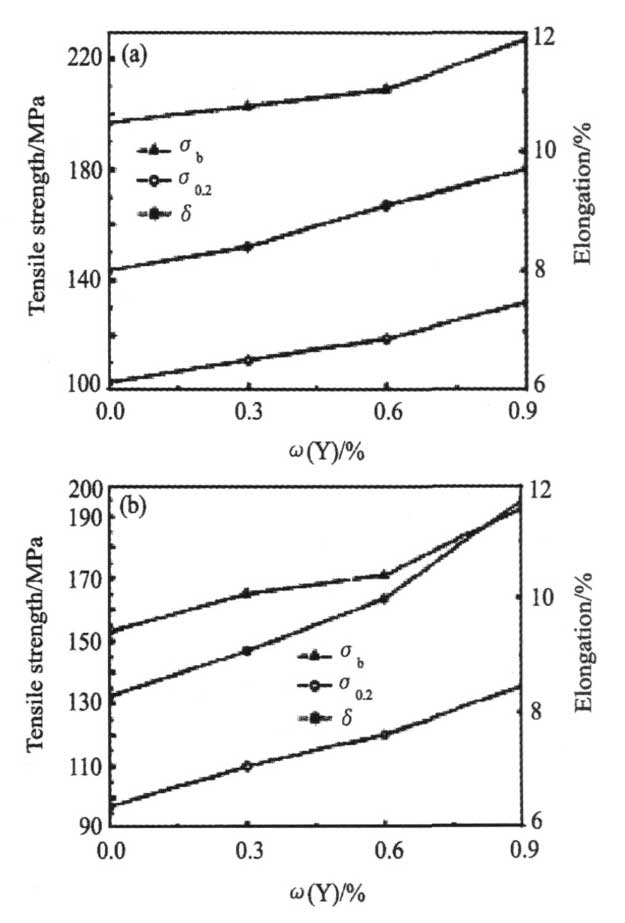
6. Effect of Yttrium on creep resistance of cast magnesium alloy
The creep resistance of Mg-Zn and mg-zn-y-zr cast magnesium alloys is studied. The results show that the alloy with the highest creep resistance is mg-4.1% zn-0.2y alloy. For mg-1.6-2.0% Zn alloy, the room temperature strength increases with the increase of Y content. The alloy with the highest strength and elongation is mg-5.4% zn-0.6% Zr, which has the finest grains and the lowest creep resistance.
The results show that the creep resistance is related to the applied stress. If the stress is greater than 40 MPa, the creep index is between 4 and 8; if the stress is less than 40 MPa, the creep index is 2.2. The relationship between microstructure and tensile and creep properties of other magnesium based alloys is also discussed.