It is beneficial to obtain castings with clear contour, precise shape, smooth surface and intact internal structure by mastering the pouring process and reasonable pouring operation. Therefore, the whole pouring process should follow the following principles:
(1) The ladle shall be dry, and the ladle can only be connected with molten steel when it is over 700 ℃;
(2) Due to the high chromium content of ghl-5 alloy, chromium oxide inclusions are easy to form during the pouring process, which reduces the fluidity. The chromium oxide film also makes the casting easy to produce defects such as cold insulation and surface wrinkling. When the temperature of molten steel is too low and the pouring time is too long, the oxidation phenomenon is more serious. Therefore, the pouring temperature should be increased and the pouring time should be shortened. The tapping temperature is 1620 ± 10 ℃, and the pouring temperature is 1580 ± 10 ℃;
(3) Inspection in front of furnace: control melting, measure temperature, sample test after chemical cleaning, adjust composition, pour plum sample in front of furnace.
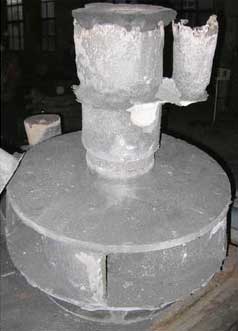
(4) The filling time is 10-12s. In the pouring process, the drainage should be accurate, the injection flow should be stable and the collection flow should be slow. In order to avoid the excessive oxidation, absorption and pouring of the molten metal, the ladle nozzle should be as close to the gate as possible;
After pouring, after cooling for a period of time, it is necessary to open a box in time to improve the cooling conditions and obtain dense metal structure. Casting after boxing is as shown in the figure: