Connecting rod is an important part of mechanical transmission. It is necessary to use connecting rod to change the direction of motion from circular motion to linear motion or from linear motion to circular motion. The automobile connecting rod is a kind of part that connects the piston and the crankshaft. It is used to transfer the pneumatic force borne by the piston to the crankshaft, and make the reciprocating motion of the piston change into the rotating motion of the crankshaft. The engine is the heart of the automobile, and the connecting rod is the key part of the engine. Therefore, the surface quality and internal quality of the connecting rod are very strict in production. The connecting rod in high-speed motion mainly bears the alternating load caused by the gas pressure and the reciprocating inertia force of the piston group. In addition, the inertia moment caused by the variable speed swing of the connecting rod also makes the connecting rod bear a small bending moment. If the rigidity of the connecting rod is not enough, the bending of the connecting rod body will cause eccentric wear between the piston and the cylinder, air leakage and oil channeling of the piston ring. If the connecting rod breaks under alternating load, it will lead to malignant damage accidents, and even the whole engine will be scrapped. Therefore, it is required to have good mechanical properties, high machining accuracy and strict quality accuracy. Moreover, the machined surface of the finished connecting rod is relatively few, and about 70% of the surface is still the forged surface. Therefore, the precision forging process must be used to produce high-quality and accurate connecting rod forgings to meet its use requirements. In addition, the connecting rod is processed by mass production with a high degree of mechanical automation, which requires that the connecting rod forgings have high repetition accuracy to meet the requirements of machining process. Therefore, the main requirement of connecting rod design is to ensure sufficient stiffness and fatigue strength under the lightest possible structure. Therefore, it is necessary to select strong materials, reasonable structural shapes and sizes, and take surface strengthening measures.
The connecting rod transmits the piston pressure to the crankshaft, and the compression stress is very high. It also forms a moving part together with the piston, so the balance of inertia mass has a great impact on the stability of engine operation and the durability of high speed zone. It can be said that in recent years, the performance of engines with high power, low fuel consumption and low vibration has endlessly required to reduce the weight of connecting rods. There are three ways to design light connecting rod:
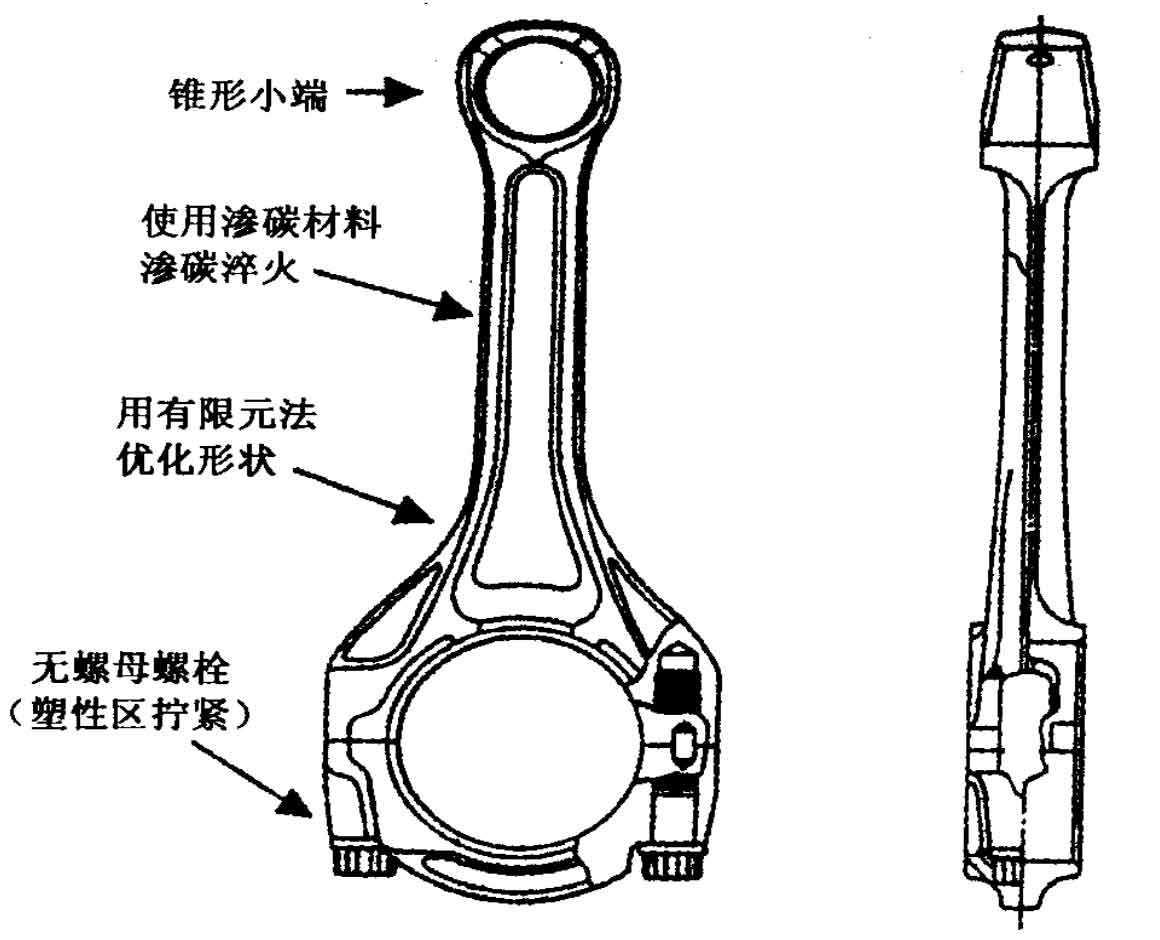
(1) Using FEM (finite element analysis) to optimize the shape of each part;
(2) Connecting rod bolts are tightened in plastic zone;
(3) Develop high strength materials, such as the light connecting rod design in Figure 1.
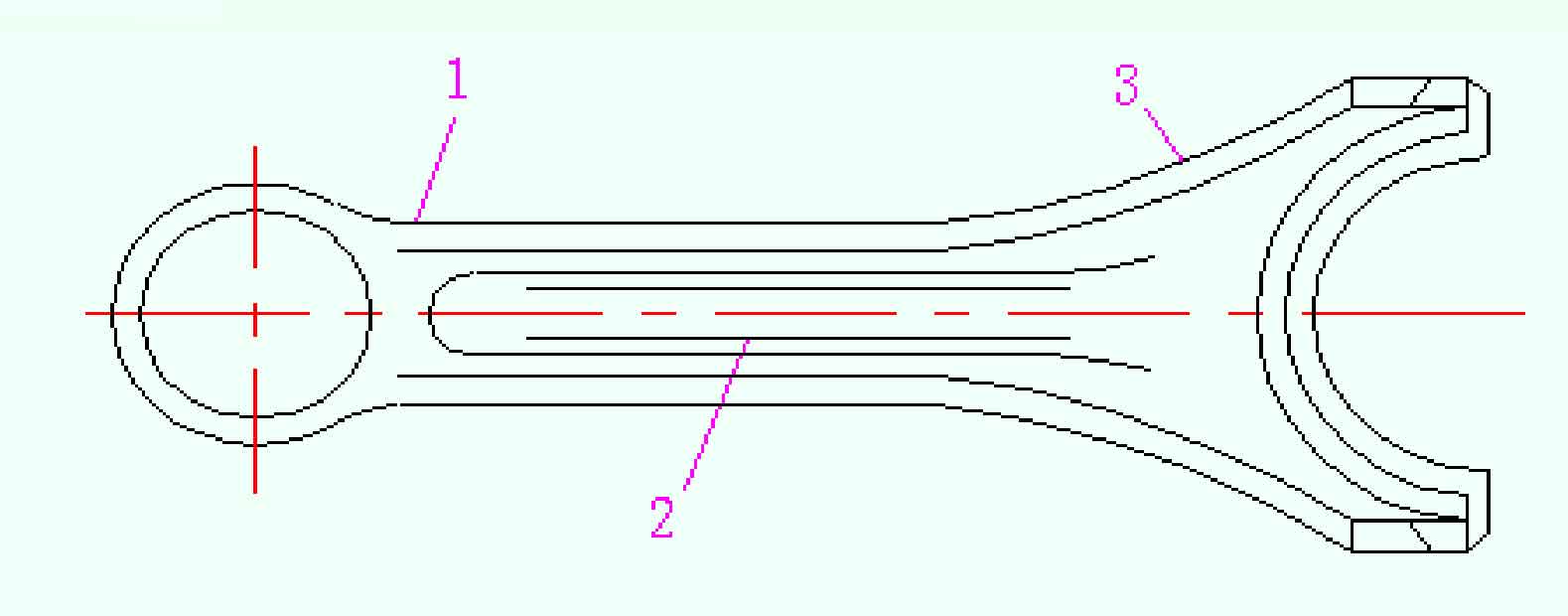
The failure mode of automobile connecting rod is mainly fatigue fracture, which often occurs in the three high stress zones on the connecting rod, as shown in Figure 2, namely, the middle of the rod body, the transition zone between the small end and the rod body, and the transition zone between the big end and the rod body (near the bolt hole); Raw material defects, forging folding and quenching cracks often lead to fracture accidents of connecting rods.