Inoculation treatment: inoculation treatment of nodular cast iron can improve the roundness of graphite ball, improve the spheroidization rate, and assist the spheroidal growth of graphite. Inoculation is an important means to increase the number of graphite balls, and the number of graphite spheres has an important effect on shrinkage cavity and porosity. There is an optimum amount of inoculant. Too little inoculant will lead to insufficient inoculation and high hardness, but too much inoculant may not melt completely, which may cause slag inclusion, increase shrinkage of cast iron, and produce shrinkage cavity and porosity.
Holding time of molten iron: the nucleation capacity of molten iron will decrease during the night residence of original iron, and a large amount of C will be burned. Therefore, it is necessary to avoid too long residence time of molten iron before spheroidizing and inoculation. Accordingly, if the hot metal after spheroidizing can not be poured in a short time, with the decline of spheroidizing and inoculation effect, the morphology and quantity of graphite will become worse, and the tendency of shrinkage cavity and porosity will increase.
Influence of mold strength: because of the unique solidification characteristics of ductile iron, volume expansion will occur during solidification process, and the expansion pressure is relatively large compared with other metals. Therefore, if the mold strength is insufficient, the “expansion” phenomenon will appear in the production process of ductile iron. The “expansion” will cause the cavity volume to increase, and more molten iron is needed for feeding, and the graphite expansion in the later stage cannot be compensated The change of filling cavity causes shrinkage porosity.
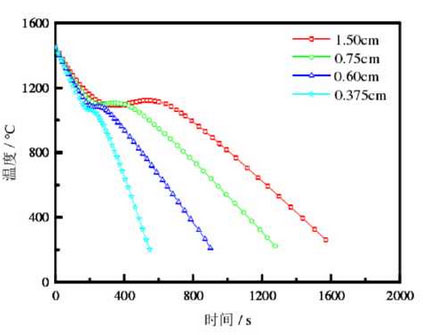
Feeding and solidification rate: in the solidification process of nodular cast iron, the shrinkage is greater than the net shrinkage of expansion, which must be replenished by foreign materials. Even if graphite expansion is fully utilized, ductile iron must have a smooth feeding channel in a certain period of solidification to complete the feeding molten iron transportation. In nodular iron, both shrinkage and shrinkage can not be eliminated before and after shrinkage. Self feeding is to make use of the difference of solidification speed and time in different regions of the casting section, and the graphitization expansion of the first solidification area offsets the ongoing shrinkage of the adjacent and later solidified regions. In order to realize the sequence of solidification time in different regions, it is necessary to have different cooling rates, which are shown in different temperature gradients on the cross section of castings. As shown in the figure below, the smaller the temperature gradient is, the closer the solidification characteristics of different regions are, and the worse the self feeding effect is; on the contrary, the better the self feeding effect is. The temperature gradient in the solidification process of casting is always changing, which is related to the composition of molten iron, pouring temperature and time, water inlet position and the modulus of parts.