The causes of shrinkage cavity and porosity of nodular cast iron are complex. The main factors affecting primary shrinkage, volume expansion and secondary shrinkage are metallurgical quality and cooling rate of molten iron, as well as the effect of spheroidizing and inoculation treatment. The metallurgical quality of nodular cast iron depends on the chemical composition, purity and superheat temperature of molten iron.
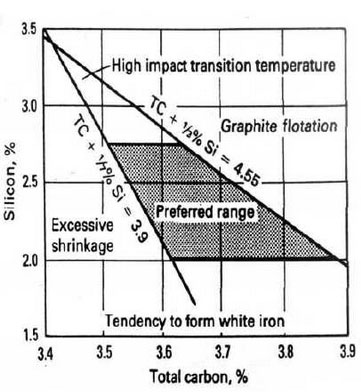
Composition of molten iron: on the premise of no graphite floating and no primary graphite precipitation, the content of C should be increased as much as possible, and the content of Si should not be too high, as long as the formation of carbide can be prevented and the strengthening ferrite can meet the requirements of mechanical properties, because C is the element that makes graphite expand, Si is the element that affects the expansion amount at the initial stage of solidification The higher the content, the more graphite balls will be, more ferrite will appear, and the graphite precipitation time will be earlier, which will lead to excessive expansion at the initial stage of solidification, and the expansion amount of residual liquid iron in the later solidification stage is insufficient, which can not offset the volume increment of the initial casting. Fig. 1 shows the influence of different C and Si element ratios on the shrinkage porosity trend of castings. Alloying elements such as Mn, Cr, Mo, V and other anti spheroidizing elements should not be too high. They form composite carbides with Fe and C atoms, which can reduce the precipitation of free C atoms, reduce the expansion of graphite, and increase the volume shrinkage value of molten iron during solidification.
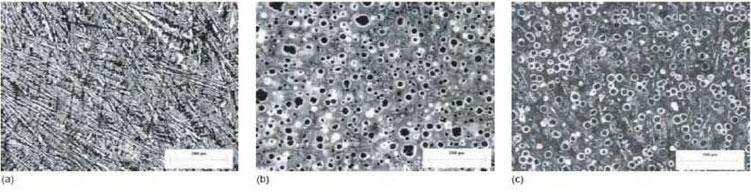
Spheroidizing treatment: the special lanthanide spheroidizing agent is used to spheroidize the molten iron (Fig. 2). The purpose of adding rare earth elements is to counteract the anti spheroidizing elements, prevent the carbide on the casting edge when the casting temperature is low, and optimize the number of graphite balls. After adding La element with high purity, not only the number of graphite balls in the casting is more, but also the sizes of graphite balls are different. The number of graphite balls precipitated in the early stage of solidification is also slightly reduced, and the number of medium and small size graphite balls increases obviously, which indicates that the graphite precipitation amount is consistent from the beginning to the end in the solidification process, so it is guaranteed that there is a large expansion amount in the later stage of solidification. While ensuring the effect of spheroidizing treatment, the amount of residual magnesium should be strictly controlled (Fig 3) When the amount of residual magnesium is high, the shrinkage porosity and shrinkage porosity tend to increase. The reason is that magnesium distributes unevenly in molten iron and has a large tendency of white mouth, and is enriched in pearlite and carbide. This area is the final region of composition segregation and eutectic solidification, and is also a high risk area of shrinkage cavity and porosity. Magnesium segregation, especially the enrichment of magnesium inclusions, creates conditions for the formation of shrinkage cavity and porosity.
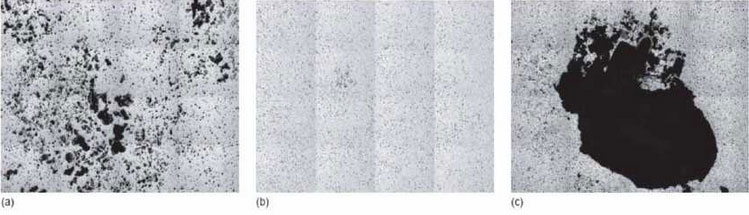