China’s sand casting industry has grown rapidly, becoming a dominant player in the global market. Its success can be attributed to the country’s efficient production processes and the use of advanced technologies. This article takes you behind the scenes of China’s sand casting industry, offering a deep dive into the production processes that have propelled it to the forefront of the casting market.
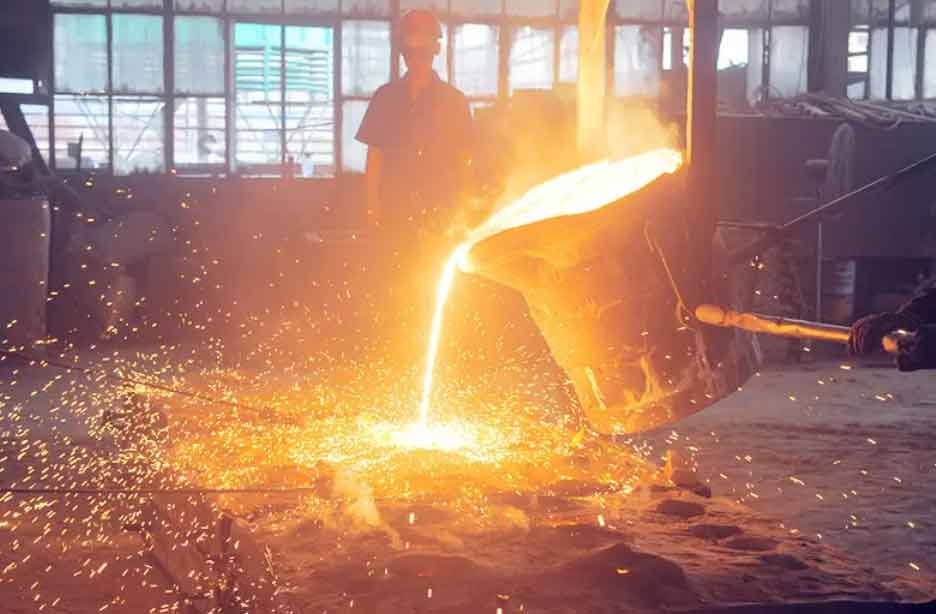
Key Stages of the Sand Casting Process in China:
- Pattern making: The process begins with the creation of a pattern, which is a replica of the final product. Typically made from wood, plastic, or metal, the pattern is designed to accommodate shrinkage during the cooling process.
- Sand mold preparation: The sand mold is created by packing a mixture of sand, clay, and water around the pattern. The sand mixture must be carefully prepared to ensure the right balance of strength, permeability, and collapsibility. The mold is then separated into two halves, known as the cope and drag, and the pattern is removed.
- Core making: If the casting requires internal cavities, a core is produced using a similar process as the sand mold. Cores are typically made from resin-coated sand and are placed inside the mold cavity to create the desired internal features.
- Mold assembly: The mold halves and any necessary cores are assembled, ensuring proper alignment. Vents and gates are added to facilitate the flow of molten metal and the release of gases during the casting process.
- Melting and pouring: The selected metal is melted in a furnace, and its composition is carefully controlled to meet the desired specifications. Once the molten metal reaches the appropriate temperature, it is poured into the mold cavity through the gating system.
- Cooling and solidification: The molten metal cools and solidifies within the mold. The cooling time depends on the size and complexity of the casting, as well as the type of metal used.
- Shakeout and cleaning: Once the metal has solidified, the sand mold is broken away, revealing the rough casting. The casting is then separated from the gating system, and any remaining sand is removed.
- Finishing and inspection: The casting undergoes various finishing processes, such as grinding, machining, and heat treatment, to achieve the desired surface finish and dimensional accuracy. Quality control measures, including visual inspection and non-destructive testing, are employed to ensure the casting meets required specifications.
Technological Advancements in China’s Sand Casting Industry:
- Computer-aided design (CAD) and simulation software: Chinese foundries have adopted CAD and simulation software to improve the efficiency and accuracy of their sand casting processes. This technology allows for better pattern design, mold optimization, and prediction of potential casting defects.
- Automation and Industry 4.0: The adoption of automation and Industry 4.0 concepts in China’s sand casting industry has resulted in increased productivity, reduced labor costs, and improved quality control.
- Green manufacturing initiatives: With increasing environmental awareness, China’s sand casting industry is focusing on sustainable practices, such as recycling and reusing sand, reducing energy consumption, and minimizing waste.
China’s sand casting industry has achieved its dominant position in the global market through efficient production processes and the adoption of advanced technologies. A deep understanding of the sand casting process, combined with a commitment to innovation and sustainability, has allowed China to meet the growing demand for high-quality, affordable castings worldwide.