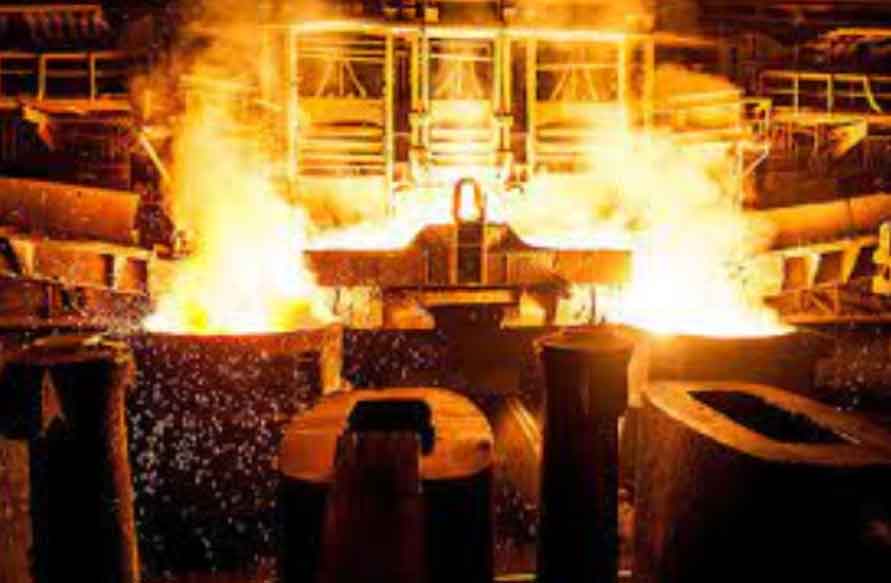
Advancements in sand casting manufacturing technology have revolutionized the traditional sand casting process, leading to increased efficiency, precision, and cost-effectiveness. Some of the notable advancements in sand casting technology include:
- Computer-Aided Design (CAD): CAD software allows engineers and designers to create detailed 3D models of castings, streamlining the design process, and reducing the time required to produce prototypes.
- Simulation and Virtual Prototyping: Advanced simulation software enables engineers to perform virtual casting simulations, predicting potential defects and optimizing the casting process before physical production begins.
- Additive Manufacturing (3D Printing): 3D printing technology has introduced new possibilities for sand casting patterns and molds. It allows for the rapid production of intricate patterns, reducing lead times, and enabling more complex designs.
- Automated Molding Machines: Automated molding machines have replaced manual labor in mold-making, improving consistency and reducing the time required to create molds.
- Robotic Systems: Robotic systems are being integrated into sand casting processes, performing tasks such as mold handling, pouring, and finishing, resulting in increased productivity and reduced human error.
- High-Performance Materials: Advancements in materials science have led to the development of high-performance molding and core materials, improving the strength and quality of sand molds.
- Real-Time Monitoring: Sensors and data analytics are being used to monitor and control various aspects of the sand casting process, ensuring quality and optimizing parameters for better results.
- Direct Part Pouring: In some cases, direct part pouring techniques eliminate the need for mold-making, allowing molten metal to be poured directly onto the core or a disposable foam pattern.
- Green Sand Reclamation: Reclamation systems are used to recycle and reuse green sand, reducing waste and making the process more environmentally friendly.
- Moldless Sand Casting: Moldless casting techniques, such as vacuum casting and die casting, have expanded the range of options available to manufacturers for producing complex and intricate components.
- Machine Learning and Artificial Intelligence: Machine learning algorithms are being utilized to optimize process parameters, predict defects, and improve casting quality.
- Innovative Cooling Techniques: Advanced cooling techniques, such as directional solidification and optimized cooling channels, enhance the metallurgical properties of the casting and reduce the risk of defects.
These advancements have transformed the sand casting manufacturing landscape, making it a more competitive and viable option for various industries. Manufacturers now have access to sophisticated tools and technologies that enhance product quality, reduce production times, and lower overall costs, contributing to the continued growth and relevance of sand casting in modern manufacturing.