Introduction
The blow bar is a crucial component in an Impact Crusher, playing a pivotal role in the crushing process by striking and breaking down materials fed into the crusher. The performance and efficiency of an Impact Crusher largely depend on the design, material, and maintenance of the blow bar. This article delves into the importance of blow bar in Impact Crushers, exploring their materials, design considerations, common issues, and maintenance practices to ensure optimal performance and longevity.
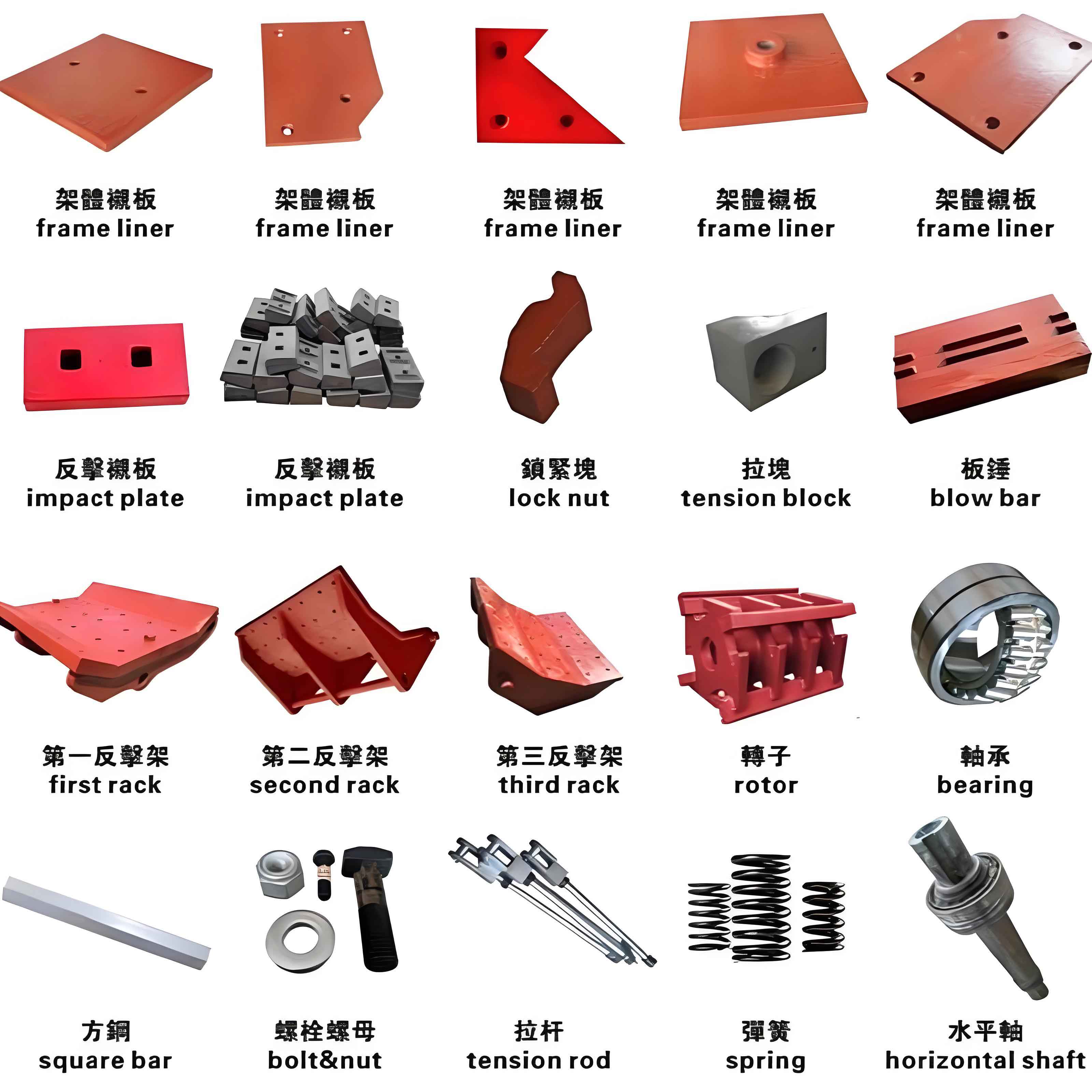
The Role of Blow Bar in Impact Crushers
In an Impact Crusher, the blow bar is mounted on the rotor and rotates at high speeds. When the rotor spins, the blow bar strikes the material fed into the crusher, causing it to shatter and break down into smaller pieces. The impact force generated by the blow bar is what facilitates the crushing process.
Key Functions of Blow Bar:
- Impact Force Generation:
- The blow bar generates a high-impact force that crushes the material upon contact.
- Material Shredding:
- The repeated strikes by the blow bar help shred the material into smaller, more manageable sizes.
- Reduction in Material Size:
- By continuously striking the material, the blow bar reduces it to the desired size for further processing or use.
Materials Used in Blow Bar
The material of the blow bar significantly impacts its durability, wear resistance, and overall performance in an Impact Crusher. Various materials are used to manufacture blow bar, each offering distinct properties suitable for different crushing applications.
Common Materials for Blow Bar:
- High Manganese Steel:
- Characteristics: Known for its toughness and work-hardening properties, making it highly resistant to impact.
- Applications: Ideal for crushing abrasive materials like granite and basalt.
- Advantages: Excellent impact resistance and durability.
- Disadvantages: Rapid wear when used with less abrasive materials.
- Martensitic Steel:
- Characteristics: Combines high wear resistance with good impact strength, featuring moderate hardness.
- Applications: Suitable for medium-hard materials like limestone.
- Advantages: Balanced wear resistance and toughness.
- Disadvantages: Not ideal for extremely abrasive materials.
- Chrome Steel:
- Characteristics: High hardness and excellent wear resistance due to chromium content.
- Applications: Best suited for highly abrasive materials.
- Advantages: Long lifespan in abrasive conditions.
- Disadvantages: Brittle and can break under high impact.
- Ceramic Inserts:
- Characteristics: Incorporates ceramic inserts within a steel matrix to enhance wear resistance.
- Applications: Used for extremely abrasive materials such as asphalt and concrete.
- Advantages: Superior wear resistance and extended lifespan.
- Disadvantages: Higher cost and potential for breakage if not properly manufactured.
Material | Characteristics | Applications | Advantages | Disadvantages |
---|---|---|---|---|
High Manganese Steel | Toughness, work-hardening | Abrasive materials (granite, basalt) | Excellent impact resistance | Rapid wear with less abrasive materials |
Martensitic Steel | Wear resistance, impact strength | Medium-hard materials (limestone) | Balanced wear resistance, toughness | Not ideal for extremely abrasive materials |
Chrome Steel | High hardness, wear resistance | Highly abrasive materials | Long lifespan in abrasive conditions | Brittle, can break under high impact |
Ceramic Inserts | Enhanced wear resistance | Extremely abrasive materials (asphalt) | Superior wear resistance, extended lifespan | Higher cost, potential for breakage |
Design Considerations for Blow Bar
The design of blow bar impacts their efficiency and suitability for different types of crushing applications. Key design aspects include the shape, profile, and reinforcement of the blow bar.
Shape and Profile:
- Straight Blow Bar:
- Description: Flat and straight design.
- Advantages: Easy to manufacture and replace.
- Disadvantages: Less effective in distributing impact forces, leading to uneven wear.
- Curved Blow Bar:
- Description: Curved profile to improve impact distribution.
- Advantages: Better distribution of impact forces, reducing uneven wear.
- Disadvantages: More complex to manufacture and replace.
- Wing-Tip Blow Bar:
- Description: Extended tips to enhance material penetration.
- Advantages: Improved material penetration and crushing efficiency.
- Disadvantages: Higher wear at the tips, requiring more frequent replacement.
Reinforcement:
- Solid Blow Bar:
- Description: Solid construction for maximum strength.
- Advantages: High durability and resistance to breakage.
- Disadvantages: Heavier, causing increased stress on the Impact Crusher.
- Composite Blow Bar:
- Description: Combination of materials for enhanced performance.
- Advantages: Optimized wear resistance and impact strength.
- Disadvantages: Higher manufacturing cost and complexity.
Design Aspect | Description | Advantages | Disadvantages |
---|---|---|---|
Straight Blow Bar | Flat and straight design | Easy to manufacture, replace | Less effective in impact distribution, uneven wear |
Curved Blow Bar | Curved profile | Better impact distribution, reduced wear | Complex to manufacture, replace |
Wing-Tip Blow Bar | Extended tips | Improved penetration, efficiency | Higher wear at tips, frequent replacement |
Solid Blow Bar | Solid construction | High durability, breakage resistance | Heavier, increased stress on crusher |
Composite Blow Bar | Combination of materials | Optimized wear resistance, strength | Higher cost, manufacturing complexity |
Common Issues and Maintenance of Blow Bar
Blow bar in Impact Crushers are subject to wear and tear, which can lead to several issues affecting the crusher’s performance. Regular maintenance is crucial to prolong the lifespan of blow bar and ensure efficient operation.
Common Issues:
- Wear and Tear:
- Blow bar wear down over time due to continuous impact and friction with the material being crushed.
- Solution: Regularly inspect and replace blow bar to maintain crusher efficiency.
- Breakage:
- Blow bar can break if subjected to excessive impact force or if they are made from brittle materials.
- Solution: Use blow bar made from materials with high impact resistance and ensure proper installation.
- Uneven Wear:
- Uneven wear can occur due to improper alignment or inconsistent feed material.
- Solution: Ensure proper alignment of blow bar and maintain consistent feed material quality.
Maintenance Practices:
- Regular Inspections:
- Conduct routine inspections to check for signs of wear, cracks, or damage.
- Replace blow bar when wear reaches critical levels to prevent damage to the Impact Crusher.
- Proper Installation:
- Ensure blow bar is correctly installed and secured to avoid movement during operation.
- Follow manufacturer guidelines for installation and torque specifications.
- Material Selection:
- Select the appropriate material for blow bar based on the type of material being crushed and the specific crusher application.
- Use high-quality blow bar to ensure durability and performance.
- Balancing:
- Regularly balance the rotor to minimize vibration and uneven wear on blow bar.
- Ensure that all blow bar is of the same weight and dimensions to maintain balance.
Issue | Cause | Solution |
---|---|---|
Wear and Tear | Continuous impact and friction | Regular inspection and replacement |
Breakage | Excessive impact force, brittle materials | Use high impact resistance materials, ensure proper installation |
Uneven Wear | Improper alignment, inconsistent feed material | Proper alignment, consistent feed material |
Vibration | Unbalanced rotor | Regular balancing, use uniform blow bar |
Conclusion
Blow bar is essential components in Impact Crushers, directly influencing the efficiency and effectiveness of the crushing process. By selecting the right material, considering design aspects, and implementing regular maintenance practices, operators can ensure that their blow bar deliver optimal performance and longevity. Understanding the characteristics and applications of different blow bar materials, such as high manganese steel, martensitic steel, chrome steel, and ceramic inserts, allows for better decision-making and improved crusher performance. Proper management of blow bar leads to enhanced productivity, reduced operational costs, and prolonged equipment life in various crushing applications.