Lost wax casting, also known as investment casting, is a highly precise and versatile technique widely used to produce complex metal components. High-performance alloys, such as those used in aerospace, medical, and industrial applications, require careful consideration of process parameters to achieve optimal results. This article explores the optimization of the lost wax casting process for high-performance alloys, focusing on key areas such as alloy selection, mold materials, process control, and post-casting treatments.
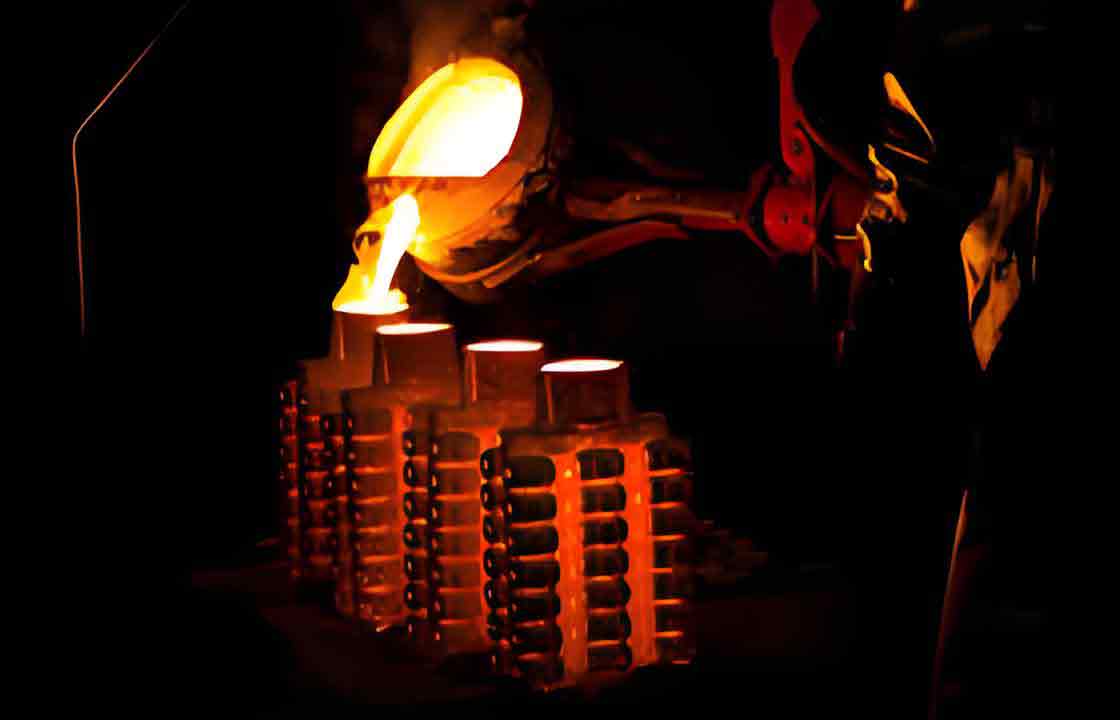
Alloy Selection for Lost Wax Casting
Choosing the right alloy is crucial for achieving the desired properties in high-performance components. High-performance alloys typically exhibit superior mechanical properties, corrosion resistance, and temperature stability. Some common high-performance alloys used in lost wax casting include:
1. Superalloys
Superalloys, such as Inconel and Hastelloy, are designed to withstand extreme temperatures and corrosive environments. These alloys are commonly used in aerospace and industrial gas turbine applications.
- Properties:
- Excellent high-temperature strength
- Superior oxidation and corrosion resistance
- Good creep resistance
2. Titanium Alloys
Titanium alloys, like Ti-6Al-4V, offer a unique combination of strength, lightweight, and biocompatibility, making them ideal for aerospace, medical implants, and sports equipment.
- Properties:
- High strength-to-weight ratio
- Excellent corrosion resistance
- Biocompatibility
3. Stainless Steels
Stainless steels, such as 316L and 17-4 PH, are widely used for their excellent corrosion resistance and mechanical properties, suitable for medical devices, automotive components, and industrial equipment.
- Properties:
- Excellent corrosion resistance
- Good mechanical properties
- Versatility in applications
Alloy Type | Properties | Applications |
---|---|---|
Superalloys | High-temperature strength, corrosion resistance, creep resistance | Aerospace, industrial gas turbines |
Titanium Alloys | Strength-to-weight ratio, corrosion resistance, biocompatibility | Aerospace, medical implants, sports equipment |
Stainless Steels | Corrosion resistance, mechanical properties | Medical devices, automotive components, industrial equipment |
Mold Materials and Preparation
The quality of the ceramic mold used in lost wax casting significantly affects the final component’s properties. Optimizing mold materials and preparation techniques is essential for casting high-performance alloys.
1. Refractory Materials
Refractory materials used in mold making must withstand high temperatures and provide dimensional stability. Common refractory materials include:
- Silica: Provides good thermal stability and is cost-effective.
- Zircon: Offers excellent thermal stability and low thermal expansion, ideal for high-performance alloys.
- Alumina: High melting point and good thermal stability, suitable for superalloys.
2. Mold Coating
Applying a high-quality coating to the mold surface enhances its performance. Coatings such as yttria-stabilized zirconia (YSZ) can improve mold durability and prevent metal-mold reactions.
3. Shell Building
Building a strong and stable ceramic shell is crucial for maintaining the mold’s integrity during metal pouring. The shell-building process involves multiple layers of ceramic slurry and fine sand:
- Primary Coating: Apply a thin layer of ceramic slurry to the wax pattern to capture fine details.
- Secondary Coating: Add successive layers of ceramic slurry and sand to build shell thickness and strength.
- Drying: Allow each layer to dry thoroughly before applying the next.
Refractory Material | Properties |
---|---|
Silica | Good thermal stability, cost-effective |
Zircon | Excellent thermal stability, low thermal expansion |
Alumina | High melting point, good thermal stability |
Process Control and Optimization
Controlling and optimizing the lost wax casting process parameters is essential for achieving high-quality castings with high-performance alloys. Key parameters include:
1. Temperature Control
Maintaining precise temperature control during mold preheating, metal melting, and pouring is critical. High-performance alloys often require higher pouring temperatures, necessitating robust temperature monitoring systems.
- Mold Preheating: Preheat the mold to remove moisture and prevent thermal shock. Typical preheating temperatures range from 800°C to 1100°C.
- Metal Melting: Use induction furnaces or vacuum melting to achieve the required metal temperature, ensuring complete melting and homogeneity.
- Metal Pouring: Maintain a consistent pouring temperature to prevent defects such as cold shuts and incomplete filling.
2. Vacuum Casting
Vacuum casting is often employed for high-performance alloys to reduce oxidation and contamination. This technique involves pouring molten metal into the mold under vacuum conditions, minimizing gas entrapment and ensuring a high-quality casting.
3. Solidification Control
Controlling the solidification process is essential for minimizing defects and achieving the desired microstructure. Techniques such as directional solidification and rapid cooling can enhance the mechanical properties of the final component.
- Directional Solidification: Promote unidirectional grain growth to improve mechanical properties such as strength and fatigue resistance.
- Rapid Cooling: Use controlled cooling rates to achieve the desired microstructure and reduce the risk of defects.
Process Parameter | Optimization Techniques |
---|---|
Temperature Control | Precise monitoring during mold preheating, metal melting, and pouring |
Vacuum Casting | Minimizes oxidation and contamination |
Solidification Control | Directional solidification, rapid cooling |
Post-Casting Treatments
Post-casting treatments are crucial for enhancing the properties of high-performance alloy castings. These treatments include:
1. Heat Treatment
Heat treatment processes such as annealing, solution heat treatment, and aging can improve the mechanical properties and performance of cast components.
- Annealing: Relieves internal stresses and improves ductility.
- Solution Heat Treatment: Dissolves alloying elements to form a homogeneous structure, followed by rapid cooling to retain the solution structure.
- Aging: Enhances strength and hardness through controlled precipitation of alloying elements.
2. Surface Finishing
Surface finishing techniques improve the component’s aesthetic appearance, corrosion resistance, and wear resistance.
- Polishing: Achieves a smooth and reflective surface, enhancing corrosion resistance.
- Electroplating: Deposits a thin layer of metal on the surface, improving wear resistance and appearance.
- Anodizing: Forms a protective oxide layer, enhancing corrosion resistance and providing a decorative finish.
3. Non-Destructive Testing
Non-destructive testing (NDT) methods are used to inspect cast components for defects without causing damage. Common NDT techniques include:
- X-ray Inspection: Detects internal defects such as porosity and cracks.
- Ultrasonic Testing: Identifies subsurface flaws and material discontinuities.
- Magnetic Particle Testing: Reveals surface and near-surface defects in ferromagnetic materials.
Post-Casting Treatment | Benefits |
---|---|
Heat Treatment | Relieves stresses, improves ductility, enhances strength and hardness |
Surface Finishing | Improves appearance, corrosion resistance, and wear resistance |
Non-Destructive Testing | Detects internal and surface defects without causing damage |
Conclusion
Optimizing the lost wax casting process for high-performance alloys involves careful consideration of alloy selection, mold materials, process control, and post-casting treatments. By implementing these optimizations, manufacturers can produce high-quality cast components with superior mechanical properties, corrosion resistance, and overall performance. Understanding and controlling the various factors involved in the lost wax casting process ensures the successful production of components that meet the demanding standards of industries such as aerospace, medical, and industrial applications.