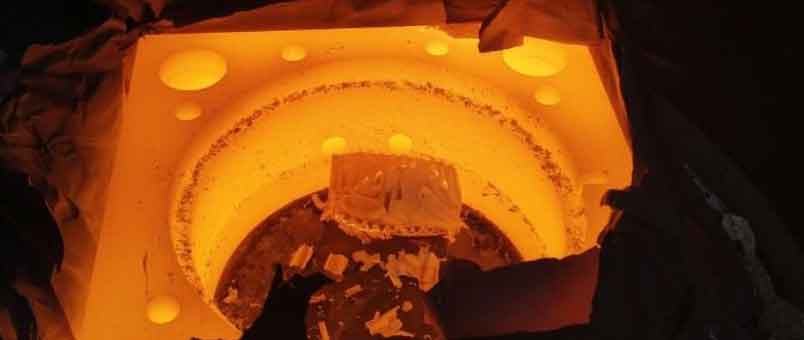
Brittle fracture in heat-treated materials refers to the sudden and catastrophic failure of a component without significant plastic deformation. It is characterized by little or no warning before fracture occurs, and it often happens at stresses below the material’s ultimate tensile strength. Understanding the causes and prevention of brittle fracture is crucial for ensuring the structural integrity of heat-treated components. Here are key aspects to consider:
- Causes of Brittle Fracture:
- High-strength materials: Materials with high strength, such as some steels or alloys, are more prone to brittle fracture.
- Low toughness: Materials with low toughness, which is a measure of a material’s ability to absorb energy before fracturing, are more susceptible to brittle fracture.
- Low temperature: Brittle fracture susceptibility generally increases at lower temperatures due to reduced ductility and increased brittleness.
- Residual stresses: The presence of residual stresses in heat-treated materials can reduce their fracture toughness and promote brittle fracture.
- Notch sensitivity: Components with sharp notches, cracks, or stress concentrations are more susceptible to brittle fracture.
- Incorrect heat treatment: Improper selection or execution of heat treatment processes can lead to a material’s inadequate toughness, making it prone to brittle fracture.
- Preventive Measures:
- Material selection: Choose materials with adequate toughness for the intended application to minimize the risk of brittle fracture.
- Proper heat treatment: Implement the correct heat treatment processes and parameters, ensuring the desired combination of strength, toughness, and ductility is achieved.
- Stress relief: Perform stress-relief heat treatment to minimize residual stresses that can reduce fracture toughness.
- Avoid notch or stress concentration: Design components with smooth transitions, avoiding sharp notches or stress concentration points that can initiate brittle fracture.
- Impact testing: Conduct impact tests, such as Charpy or Izod tests, to assess the material’s resistance to brittle fracture and validate its toughness.
- Temperature control: Consider operating temperatures and environmental conditions to prevent exposure to low temperatures that can increase the risk of brittle fracture.
- Quality control: Implement rigorous quality control measures to ensure material properties and heat treatment quality, including proper documentation and adherence to standards.
- Non-Destructive Testing (NDT):
- Utilize non-destructive testing techniques like ultrasonic testing, magnetic particle inspection, or radiographic testing to identify potential defects or cracks that can lead to brittle fracture. Regular inspections can help detect early signs of degradation and prevent catastrophic failures.
- Design considerations:
- Smooth transitions and fillet radii: Incorporate smooth transitions and fillet radii in component design to reduce stress concentration and avoid sharp corners.
- Design for adequate toughness: Consider the intended application and design components with sufficient toughness to withstand potential loading conditions.
- Material and Process Certification:
- Ensure the use of certified materials and follow proper process certification protocols to maintain consistency and quality in heat treatment.
- Failure analysis:
- In case of brittle fracture occurrence, conduct a thorough failure analysis to determine the root cause and take corrective actions to prevent future failures.
It’s important to note that preventing brittle fracture requires a holistic approach, involving material selection, proper heat treatment, design considerations, quality control measures, and adherence to industry standards and best practices. Collaborating with metallurgical experts and heat treatment specialists can provide valuable insights and guidance in mitigating the risk of brittle fracture in heat-treated materials.