Investment casting, also known as lost wax casting, is a fascinating and intricate manufacturing process that combines artistry and precision. With origins dating back thousands of years, investment casting has evolved into a sophisticated technique widely used today to create complex and detailed metal components. In this response, we will delve into the art and precision involved in lost wax casting.
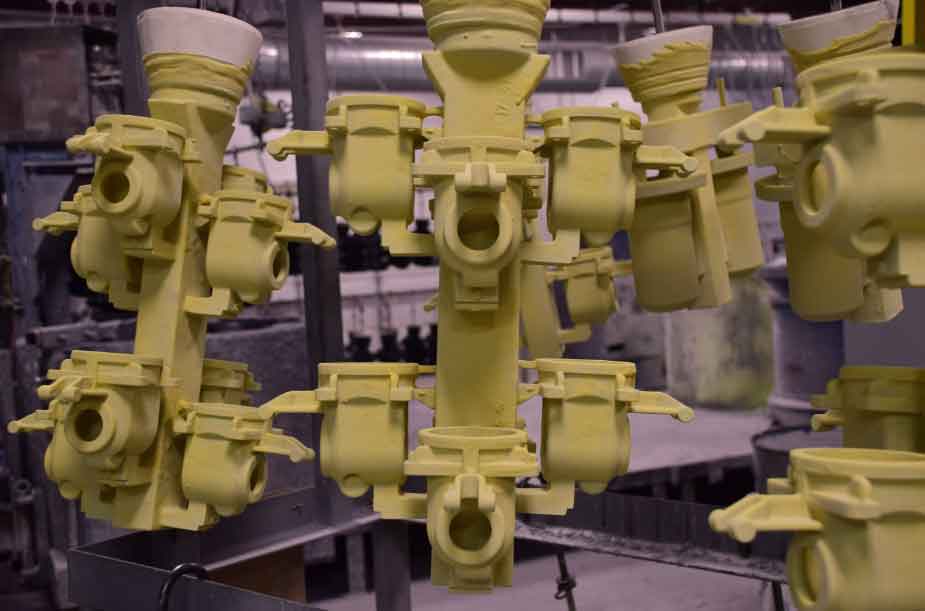
The Art of Lost Wax Casting:
Lost wax casting is often regarded as an art form due to the craftsmanship and creativity required throughout the process. It begins with the creation of a wax pattern, which serves as a replica of the desired final product. Skilled artisans can sculpt these wax patterns by hand or use specialized tools to achieve intricate details and precise shapes.
The wax pattern is not just a functional piece but also an artistic creation. In industries like jewelry manufacturing, where lost wax casting is extensively used, designers and craftsmen can transform their creative visions into tangible wax patterns. This artistic aspect allows for the production of unique and aesthetically pleasing designs.
Once the wax pattern is created, it undergoes various steps, including spruing (attaching wax rods or gates), investing (encasing the pattern in a ceramic shell), and burnout (melting the wax to create a hollow mold). These stages require careful attention to detail and a deep understanding of the materials and processes involved.
Precision in Lost Wax Casting:
Precision is a fundamental characteristic of investment casting. The ability to faithfully reproduce intricate details and maintain dimensional accuracy sets lost wax casting apart from other casting methods. This precision is achieved through several key factors:
- Wax Pattern Production: The creation of an accurate wax pattern is crucial for maintaining precision throughout the process. Skilled craftsmen ensure that the wax pattern matches the desired specifications and captures the intricacies of the final product.
- Ceramic Shell Formation: The ceramic shell created around the wax pattern plays a vital role in maintaining precision. The application of multiple layers of ceramic slurries and stucco helps build a high-quality shell with precise dimensions, ensuring that the molten metal will fill the mold accurately.
- Molten Metal Pouring: The controlled pouring of molten metal into the ceramic shell requires precision to achieve consistent results. Factors such as temperature, pouring speed, and gating system design are carefully controlled to minimize defects and ensure proper filling of the mold.
- Solidification and Cooling: The cooling process after the metal is poured affects the final dimensions and properties of the cast component. Proper cooling rates and heat dissipation techniques are employed to prevent warping, shrinkage, and other issues that could compromise precision.
Applications of Lost Wax Casting:
Lost wax casting’s artistry and precision make it well-suited for a wide range of applications, including:
- Art and Sculpture: Lost wax casting has long been used in the creation of sculptures and artistic pieces. It allows artists to translate their designs into metal with intricate details and precise forms.
- Jewelry: The jewelry industry extensively relies on lost wax casting to produce intricate and delicate pieces. The process enables the creation of complex designs, gemstone settings, and personalized jewelry.
- Industrial Components: Investment casting finds applications in industries such as aerospace, automotive, and medical, where complex and high-precision components are needed. Turbine blades, engine parts, orthopedic implants, and various mechanical components are commonly produced using lost wax casting.
In summary, lost wax casting combines the artistry of wax pattern creation with the precision required to reproduce intricate details and maintain dimensional accuracy. It is a versatile process that finds applications in art, jewelry, and industries where complex and precise components are needed. The art and precision of lost wax casting continue to captivate artisans and manufacturers alike, preserving its status as a remarkable manufacturing technique.