According to the optimized process scheme, the resource consumption, energy consumption and carbon emission in the compound mold forming process of Moldless sand casting are calculated. The mold production and processing process only takes the sand mold 3D printing process of No. 3# mold as an example, as shown in Figure 1.
The main material consumption list of the original process design scheme and process optimization design scheme of composite mold in the production of unit casting under A1 production conditions. The molding materials include furan resin sand and green molding sand. The mass of wood mold used for sprue and feeding riser molding is 0.302kg, and the consumption of wood mold evenly distributed to unit casting is 0.006kg.
Figure 2 shows the Gantt chart of the casting process flow of the composite mold under the optimized process design scheme. Among them, red represents the traditional pattern modeling process, blue represents the sand mold NC milling process, yellow represents the sand mold 3D printing process, and orange represents the common process. In the production process, according to the process characteristics of composite mold forming, some casting processes can be carried out in parallel, such as wood pattern making, sand mixing process and sand mold 3D printing can be carried out at the same time, so as to reduce the casting time.
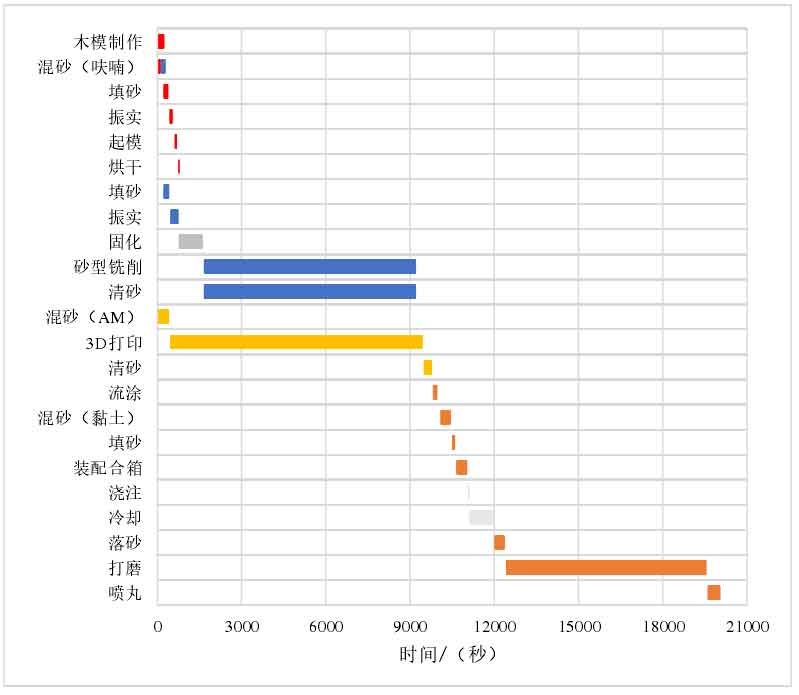
Similarly, the energy consumption per unit casting of composite mold production can be obtained according to the energy consumption calculation formula and workshop electricity meter data. Figure 3 shows the power curve of 3# mold during 3D printing. The single sand mixing amount of the printer is about 10kg, and the sand mixing and feeding cycle is 600s. During the printing process, the sand mixing system and sand feeding system will be continuously and intermittently to maintain the amount of sand in the sand laying beam. Through the analysis of the collected power curve by the origin cluster analysis tool, it can be obtained that the average printing power of the 3D printer in normal operation is 320W.
Similarly, the unit casting production time, production efficiency and energy efficiency ratio of composite mold can be obtained.
Similarly, the carbon emission and carbon efficiency per unit casting production of compound forming method are calculated according to the formula. Taking the compound mold optimization process design scheme as an example, the calculation of carbon emission per unit casting production under A1 production conditions:
The carbon emission of materials under the optimized process scheme is calculated as follows:
The calculation of energy carbon emission under the optimized process scheme is as follows:
The calculation of unexpected carbon emission under the optimized process scheme is as follows:
To sum up, the total carbon emission per unit casting production under A1 production conditions in the optimized process design scheme of composite mold is: