For the liquid metal casting process, the interval between pouring of two metals is very critical:
- the interval is too short, the high chromium cast iron poured first has not solidified, and then the molten metal of high temperature carbon steel will be mixed with it, resulting in the material performance of the casting completely failing to meet the requirements of service conditions;
- the interval is too long. The high chromium cast iron poured first is completely solidified and the temperature is very low, and then the high-temperature carbon steel molten metal is poured. Under the chilling effect of the high chromium cast iron metal, the fusion and atomic diffusion between the two metals are too late to occur, resulting in the thin interface transition bonding area or the inability to achieve effective metallurgical bonding, and the bonding strength between the high chromium cast iron layer and the carbon steel layer is insufficient, It will cause accidents in the service of the ball mill.
How to determine the appropriate pouring interval is the key technical parameter to successfully realize the dual liquid bimetallic lost foam process, which is calculated by the following formula:
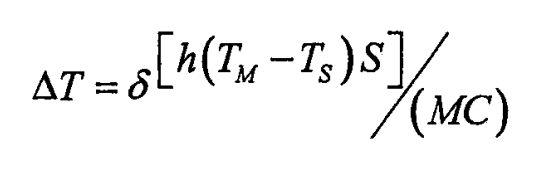
According to the formula, the falling temperature of carbon steel in the lost foam casting mold per second is 3.8 ° C, the melting point of high chromium cast iron is about 1200 ° C, and the initial pouring temperature is 1480 ° C. It can be calculated that the liquid metal of high chromium cast iron begins to solidify after about 73 seconds of pouring. Three intervals of 60s, 75s and 90s were used in the pouring stage, and the effects of different intervals on the composite interface were analyzed.