According to the function, the riser of lost foam casting process can be divided into feeding riser, exhaust slag collecting riser and two functional risers. The feeding riser is usually set above the hot spot of the casting to realize the sequential solidification and ensure the densification of the casting group. The exhaust slag collecting riser is usually located at the place where the metal liquid is filled at last or the two metal liquid converging parts. It plays the role of collecting the pyrolytic product of foam pattern and preventing the defects such as carburization, slag inclusion, cold separation and blowhole.
The methods of riser design include modulus method, feeding liquid method and proportion method. Modulus is expressed by m, and its implication is the ratio of casting volume to heat transfer surface area, also known as solidification pouring number
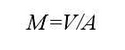
Where
M ⎯ modulus (CM);
V ⎯ volume (cm3);
A ⎯ heat transfer surface area (cm2).
In order to use modulus method to design riser more conveniently, the softened modulus method is usually used to calculate, and then the feeding liquid method is used to check. The softening formula is as follows:
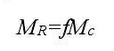
Where
Mr ⎯ riser modulus;
MC ⎯ casting modulus;
F ⎯ The calibration formula of feeding liquid method is as follows:
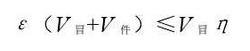
Where
ε ⎯ The feeding efficiency of η⎯⎯ riser is 12% ~ 15%;
V riser ⎯ volume;
V part ⎯ casting volume.