There is an eccentric mass on each section along the axis of the mold. The eccentric mass on the i-th disc can be expressed by two parameters: the eccentric distance EI and the azimuth angle θ I. In order to study the influence of mold mass eccentricity on the vibration performance of centrifugal casting machine, four kinds of eccentric mass distribution states and the eccentricity EI of each distribution are considered.
Figure 1 shows the amplitude frequency response curves of the mold under four eccentric mass distributions. It can be seen from the figure that when the azimuth of eccentricity does not change along the axis, even if the position of eccentricity changes, the shape of the amplitude frequency response curve hardly changes (as shown in Fig. 1 (a) and Fig. 1 (b)), but when the azimuth of eccentricity changes along the axis, the shape of the amplitude frequency response curve changes obviously (as shown in Fig. 1 (c) and Fig. 1 (b)) 1 (d). In addition, the maximum amplitudes shown in Fig. 1 (a) and Fig. 1 (b) are greater than those in Fig. 1 (c) and Fig. 1 (d), respectively. That is to say, when the eccentricity is equal, the vibration amount when the eccentricity azimuth changes according to a certain rule is less than that when the eccentricity azimuth is fixed.
Figure 2 shows the mode shape of the mold at 3000 r.min-1. It can be seen that the vibration modes in Fig. 2 (a) and Fig. 2 (b) have similar shapes, that is, the amplitude at both ends of the rotor is smaller, and the closer to the center of the rotor, the greater the amplitude. The shape of vibration mode in Fig. 2 (c) is similar to that in Fig. 2 (d), which means that the amplitude near the support point is smaller, and the amplitude far away from the support point is larger, and the vibration at the end of the rotor is greater than that at the center of the rotor. That is to say, when the eccentric azimuth is fixed, the vibration of the middle part of the mold is greater than that of the extended part. When the eccentric azimuth changes according to a certain rule, the situation is just the opposite, and the vibration of the extended part is greater than that of the middle part. According to the calculation, when the mold speed is 3000r.min-1, the maximum amplitudes of the four eccentric distributions appear at node 51, 51, 101 and 1 respectively.
Figure 3 shows the center trajectory of the node with large vibration under four kinds of eccentric distribution. Because of the consideration of the support heterogeneity in the horizontal and vertical directions, the trajectory of the node is ellipse. From the comparison of Fig. 3 (a) and Fig. 3 (c) and Fig. 3 (b) and Fig. 3 (d), it can be seen that under the condition of equal eccentricity, the vibration amount when the eccentricity azimuth changes according to a certain rule is obviously smaller than that when the eccentricity azimuth is fixed, which is the same as the conclusion in Fig. 2. It can be seen that the distribution of eccentric mass has a great influence on the vibration performance of rotor system, especially the influence of eccentric azimuth.
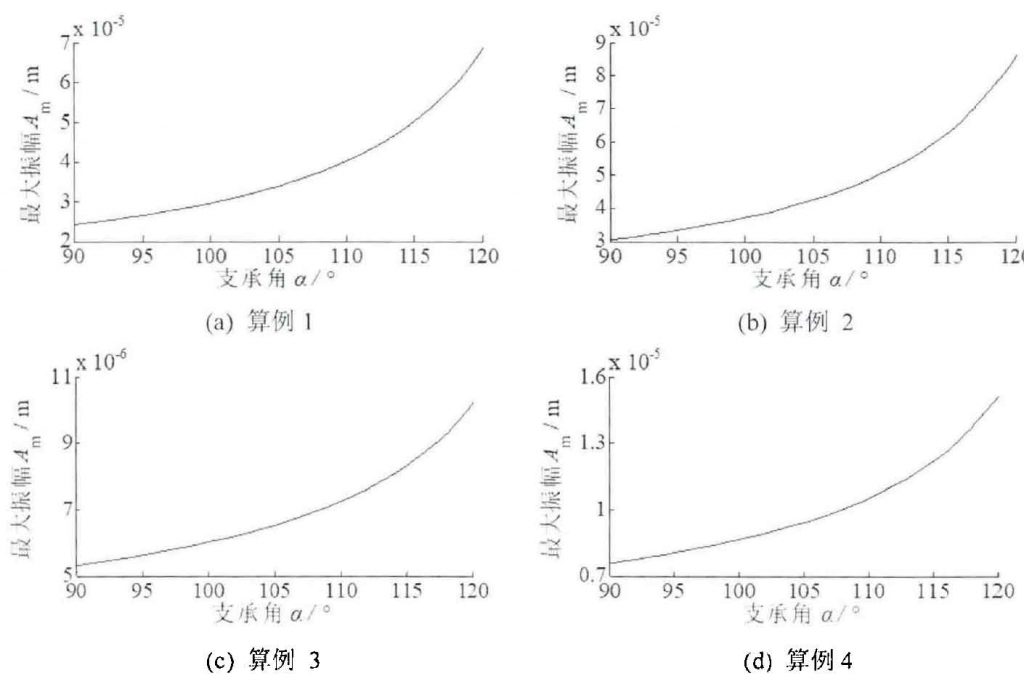
Fig. 4 shows the influence of roller support angle α = 90-120 ° on the maximum amplitude of unbalance response of cast rotor. It can be seen that the maximum amplitude of the rotor increases with the increase of the support angle when the mold speed is 3000 rmin-1. However, under this condition, no matter how the support angle α changes, the order of magnitude of the maximum amplitude is always 10 (- 5) m, and resonance will not occur.
Figure 5 shows the influence of roller support span in the range of L3 = 2-5M on the maximum amplitude of unbalance response of cast rotor. It can be seen that when the mold speed is 3000rmin (- 1), the rotor vibration is large when the support spacing L3 = 3.6-3.7m, which may be because the critical speed of the system is about 3000r.min (- 1) when L3 = 3.6-3.7m. It can be seen from Fig. 5 (c) and Fig. 5 (d) that when L3 = 2-2.2m, the amplitude of the mold is also very large, but at this time, the support span is too small and the cantilever length is too large, so this value will not be used in practice.