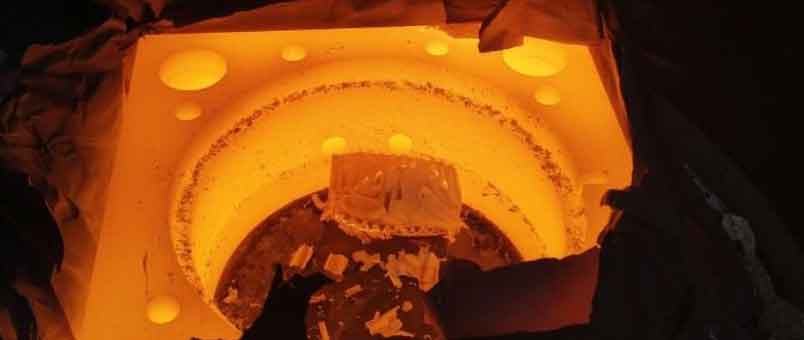
Case hardening, also known as surface hardening, is a heat treatment process used to enhance the surface hardness and wear resistance of components. However, several defects can occur during case hardening, impacting the quality and performance of the treated parts. Here are some troubleshooting tips to address common heat treatment defects encountered in case hardening:
1.Excessive Case Depth:
Issue:
The case depth, which refers to the hardened layer thickness, exceeds the desired specifications.
Potential Causes and Solutions:
- Incorrect process parameters: Review and optimize the carburizing time, temperature, and carbon potential to ensure they are within the recommended ranges.
- Long carburizing times: Reduce the carburizing time to prevent excessive carbon diffusion and achieve the desired case depth.
- Inadequate quenching: Ensure the quenching medium and method are suitable for the material and control the cooling rate to prevent excessive hardening.
2.Insufficient Case Depth:
Issue:
The case depth achieved is below the desired specifications.
Potential Causes and Solutions:
- Insufficient carburizing time: Increase the carburizing time to allow for sufficient carbon diffusion and achieve the desired case depth.
- Low carburizing temperature: Verify that the carburizing temperature is within the recommended range for the material to facilitate carbon absorption.
- Poor carbon potential: Ensure the carbon potential of the atmosphere or the carburizing compound is adequate to promote effective carbon diffusion.
3.Case Irregularities or Staining:
Issue:
Uneven or non-uniform case hardness or discoloration on the treated surface.
Potential Causes and Solutions:
- Poor surface preparation: Ensure the component surfaces are clean and free from contaminants before case hardening.
- Inadequate quenching: Optimize the quenching process to achieve uniform cooling and prevent localized variations in hardness or staining.
- Non-uniform carbon distribution: Improve the distribution of the carburizing compound or atmosphere to ensure even carbon absorption.
4.Cracking or Distortion:
Issue:
Cracks or distortion occur during or after the case hardening process.
Potential Causes and Solutions:
- Excessive quenching rates: Control the quenching rate to avoid rapid and uneven cooling, which can induce cracking or distortion. Consider using appropriate quenching media or agitation methods.
- Residual stresses: Conduct stress relief heat treatment, such as tempering, to minimize residual stresses that can contribute to cracking or distortion.
- Incorrect material selection: Evaluate the material’s susceptibility to cracking or distortion during case hardening and consider using alternative materials with better heat treatment response.
5.Poor Adhesion or Delamination:
Issue:
The hardened case exhibits poor adhesion to the core material or delamination occurs between the case and the core.
Potential Causes and Solutions:
- Insufficient surface preparation: Ensure thorough cleaning and proper surface preparation to promote good adhesion between the case and the core.
- Inadequate diffusion or activation: Review and optimize the carburizing parameters, including time, temperature, and carbon potential, to facilitate proper carbon diffusion and activation of the hardening process.
- Material mismatch: Verify that the material selection is appropriate for case hardening, considering compatibility and compatibility of the core and case materials.
6.Inconsistent Hardness:
Issue:
The hardness of the case is inconsistent across the treated component.
Potential Causes and Solutions:
- Uneven carburizing atmosphere: Ensure the carburizing atmosphere or compound is evenly distributed to promote consistent carbon absorption and diffusion.
- Variations in process parameters: Review and optimize the process parameters, including temperature, time, carbon potential, and quenching, to achieve uniform and consistent results.
- Poor temperature control: Implement accurate temperature control measures to maintain consistent heat treatment conditions throughout the component.
When troubleshooting heat treatment defects in case hardening, it is important to consider factors such as process parameters, material selection, surface preparation, quenching methods, and quality control measures. Performing thorough root cause analysis, monitoring process variables, and collaborating with heat treatment experts and metallurgists can help identify the underlying issues and implement effective corrective actions.