To achieve high-quality castings and improve the overall efficiency of the casting process, manufacturers can leverage advanced techniques that help minimize casting defects. These techniques utilize cutting-edge technologies, innovative processes, and enhanced control mechanisms to optimize the casting process. This article explores some of the advanced techniques that can be employed to minimize casting defects effectively.
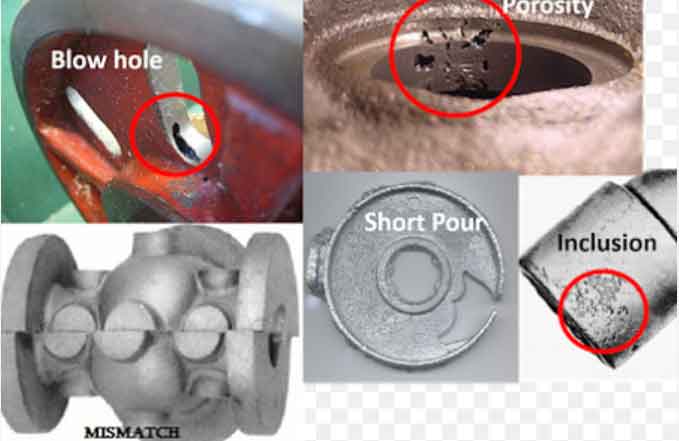
- Computer-Aided Engineering (CAE) and Simulation:
- Utilize advanced CAE software and simulation tools to model and simulate the casting process. These tools enable engineers to analyze and optimize various aspects of the process, such as mold filling, solidification, and cooling. By simulating different scenarios and optimizing process parameters virtually, potential defects can be identified and mitigated before actual casting production.
- 3D Printing and Rapid Prototyping:
- Employ 3D printing and rapid prototyping techniques to create precise and complex mold patterns and cores. These advanced techniques allow for accurate replication of intricate geometries and reduce the risk of defects associated with traditional mold making processes. By using high-resolution 3D printing technologies, the overall casting quality can be improved.
- Additive Manufacturing for Tooling and Gating Systems:
- Utilize additive manufacturing or 3D printing to produce tooling and gating systems. This approach enables the creation of customized and optimized designs that can enhance metal flow, reduce turbulence, and minimize defects like porosity and inclusions. Additive manufacturing allows for greater design freedom and flexibility, resulting in improved casting quality.
- In-line Monitoring and Control:
- Implement advanced in-line monitoring and control systems to track and adjust process parameters in real-time. These systems utilize sensors, cameras, and data analytics to continuously monitor key variables such as temperature, pressure, and flow rate. By actively controlling these parameters, the risk of defects can be minimized, and immediate corrective actions can be taken when deviations occur.
- Non-Destructive Testing (NDT) Techniques:
- Employ advanced non-destructive testing techniques, such as X-ray, ultrasonic testing, magnetic particle inspection, and laser scanning, to detect internal and surface defects in castings. These techniques enable thorough and efficient inspection without compromising the integrity of the components. Early detection of defects allows for timely corrective actions, minimizing the impact on production.
- Robotics and Automation:
- Integrate robotics and automation into the casting process to improve precision, repeatability, and consistency. Automated systems can ensure accurate pouring, controlled cooling, and optimized handling of castings, reducing the risk of defects caused by human error. Robotics and automation also enable efficient post-casting processes such as grinding, machining, and surface finishing.
- Advanced Quality Control Techniques:
- Implement advanced quality control techniques, such as 3D scanning and coordinate measuring machines (CMM), for accurate dimensional inspection and validation of castings. These techniques provide comprehensive data on deviations from design specifications, allowing for precise defect analysis and process adjustments.
- Real-Time Process Visualization and Analytics:
- Utilize advanced data visualization and analytics tools to gain real-time insights into the casting process. This allows for proactive defect detection and analysis, enabling operators and engineers to make data-driven decisions and implement corrective measures promptly.
- Material Science and Alloy Development:
- Invest in research and development of advanced materials and alloys specifically tailored for casting applications. Advanced materials with improved properties and reduced susceptibility to defects can enhance the overall casting quality and performance.
- Continuous Research and Development:
- Stay up-to-date with the latest advancements in casting technologies, materials, and process optimization strategies. Engage in continuous research and development to explore new techniques, materials, and approaches that can further minimize casting defects.
Minimizing casting defects requires the adoption of advanced techniques that leverage cutting-edge technologies and innovative approaches. By incorporating computer-aided engineering, 3D printing, advanced monitoring and control systems, non-destructive testing, automation, advanced quality control techniques, and continuous research and development, manufacturers can enhance the quality and efficiency of their casting processes. Implementing these advanced techniques enables proactive defect prevention, early detection, and timely resolution, ultimately leading to high-quality castings and improved customer satisfaction.