From January to March 2020, ZHY Casting used the above process to produce 200 motor housings in small quantities. Basically, each product has casting defects, 60% of which is serious, the overall scrap rate is about 20%, and the product quality is far from meeting the expected requirements. Due to the high scrap rate and the need for welding repair of many casting defective products, the production cost is far higher than the product sales price, and it is impossible to supply customers with quality and quantity on time, which has caused great difficulties for production and operation.
1. Statistical analysis of casting defects
In the process of small batch production, the casting defects of motor shell include crack, sand inclusion, pore, deformation, slag inclusion, etc. see the table for detailed statistics.
Defect type | Number of defective products (piece) | Scrap quantity (piece) | Defect ratio (%) | Scrap rate (%) |
Crackle | 200 | 30 | 100 | 15 |
Sand inclusion | 100 | 8 | 50 | 4 |
Stomata | 10 | 0 | 5 | 0 |
Deformation | 5 | 0 | 2,5 | 0 |
Slag inclusion | 3 | 0 | 1.5 | 0 |
From the statistical analysis table of casting defects of motor shell, it can be seen that each product has cracks, the proportion of casting defects is 100%, there are 30 waste products caused by cracks, and the waste rate is 15%. Cracks are the most prominent problem in the casting defects of motor shell. The proportion of sand inclusion casting defects is 50%, 8 pieces are scrapped, and the scrap rate is 4%. Sand inclusion is the secondary problem next to crack in the casting defects of motor shell. Porosity, deformation and slag inclusion account for a relatively small proportion, and there is no waste, which is the slightest quality problem.
Through the analysis, it can be seen that the problems of crack and sand inclusion casting defects are solved, the product quality of motor shell will go to a new level, the waste loss will drop sharply, the production cost will be greatly reduced, and the product price and quality will have a great competitive advantage.
2. Crack distribution of motor shell in blank state
The distribution of crack casting defects of motor shell is shown in Figure 1. Chalk marks it as crack. There are opening cracks at the root of flange window tie bar and large hot joint, and the rest are flaw detection crack casting defects. The specific distribution is as follows: there are 10-13 crack casting defects on the outer surface, up to 17 cracks on the inner surface 1# core, and 30-40 cracks on the inner surface 2# core due to irregular shape, so welding repair is very difficult.
3. Crack distribution on machined surface of motor housing
The machining allowance of the machined surface of the motor housing is 8mm. After machining, wet flaw detection with fluorescent magnetic particle is used. Flaw detection cracks and casting defects are still found on the inner cylindrical surface and around the threaded hole at the round end of the stop. See Figure 2 for details.
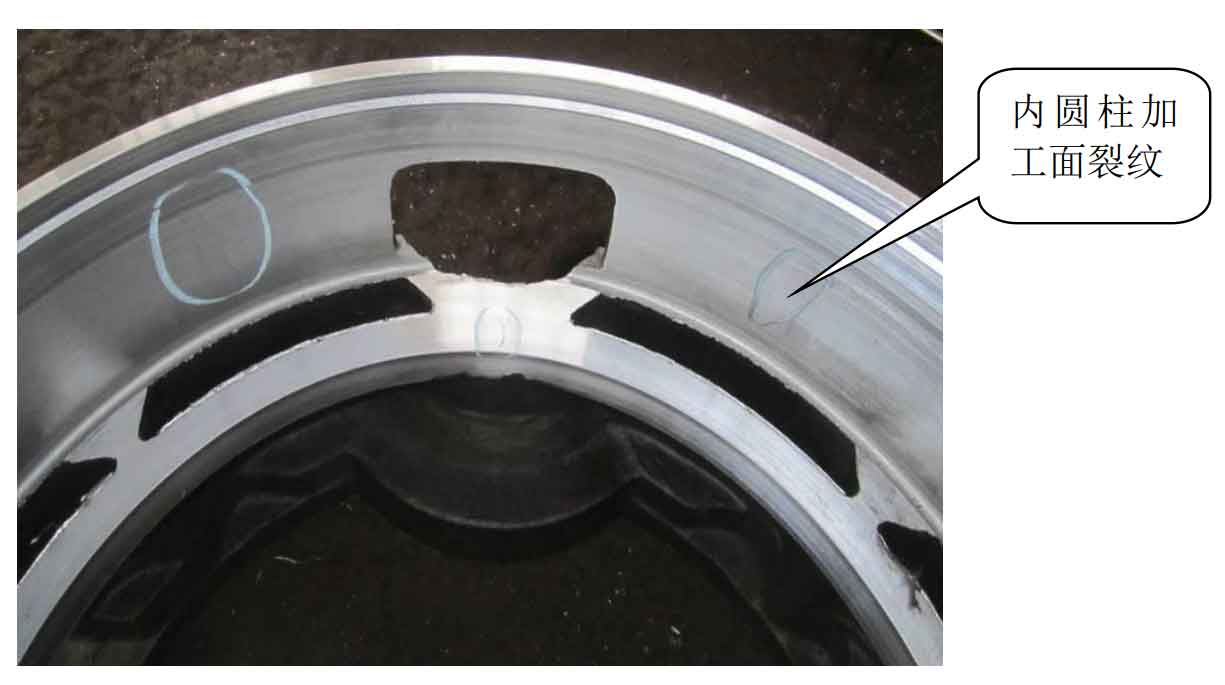
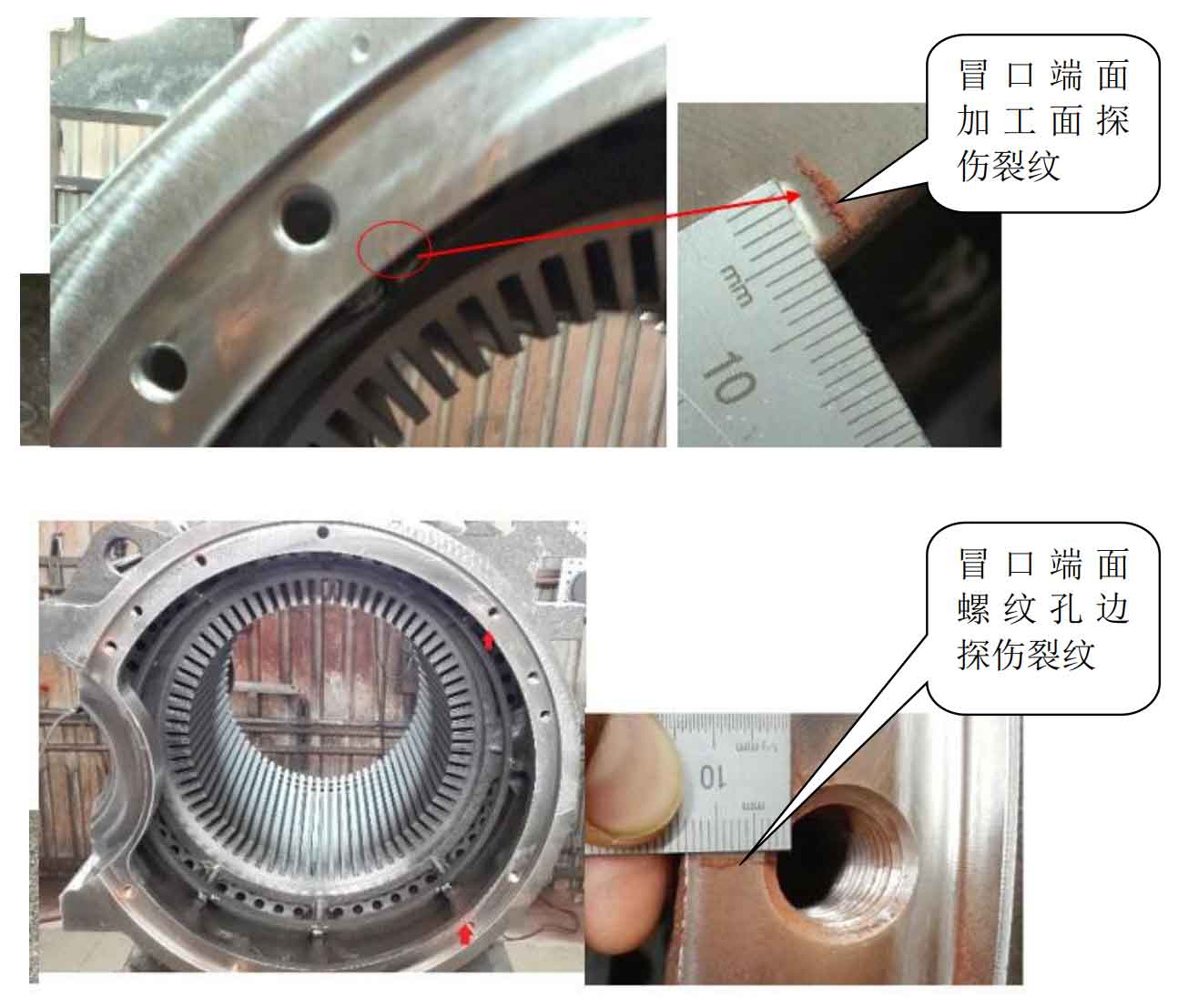
4. Distribution of sand inclusion in motor shell
Sand inclusion casting defect is an inertial quality problem of sand casting. There are many sand inclusion casting defects of motor shell produced by the existing process, especially on the machining surface of inner cylinder, there are more than 50 sand inclusion points in dispersion mold, and the quality condition is worrying. See Figure 3 for details.
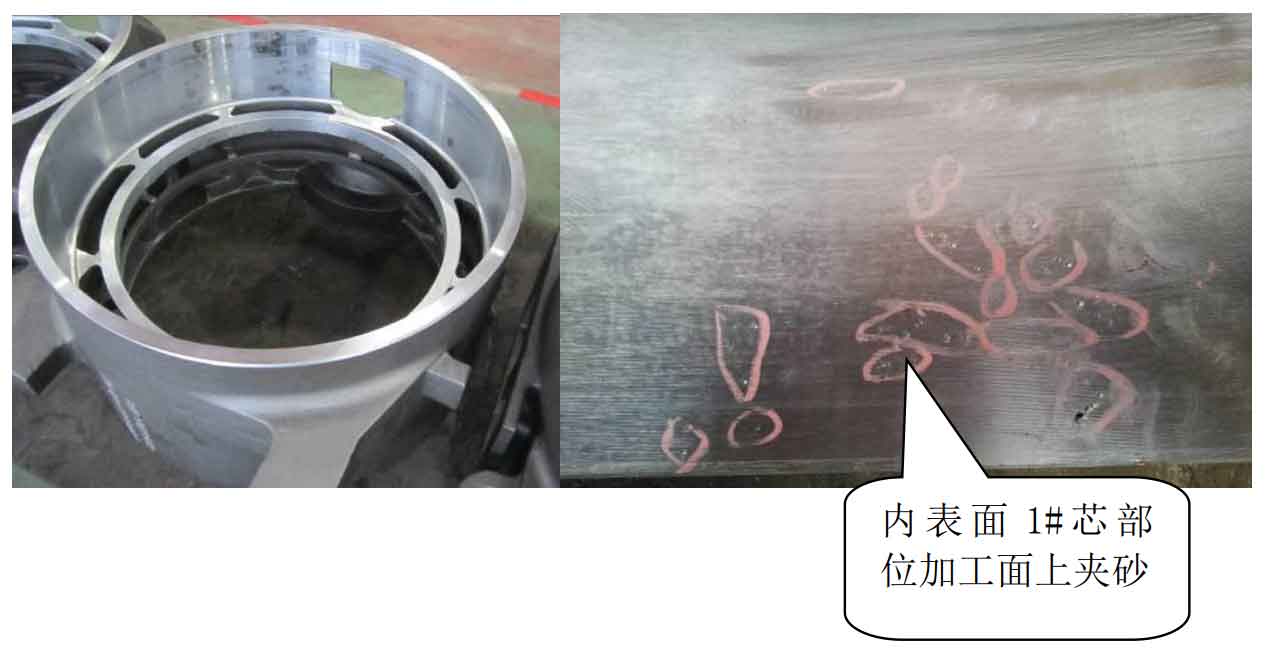
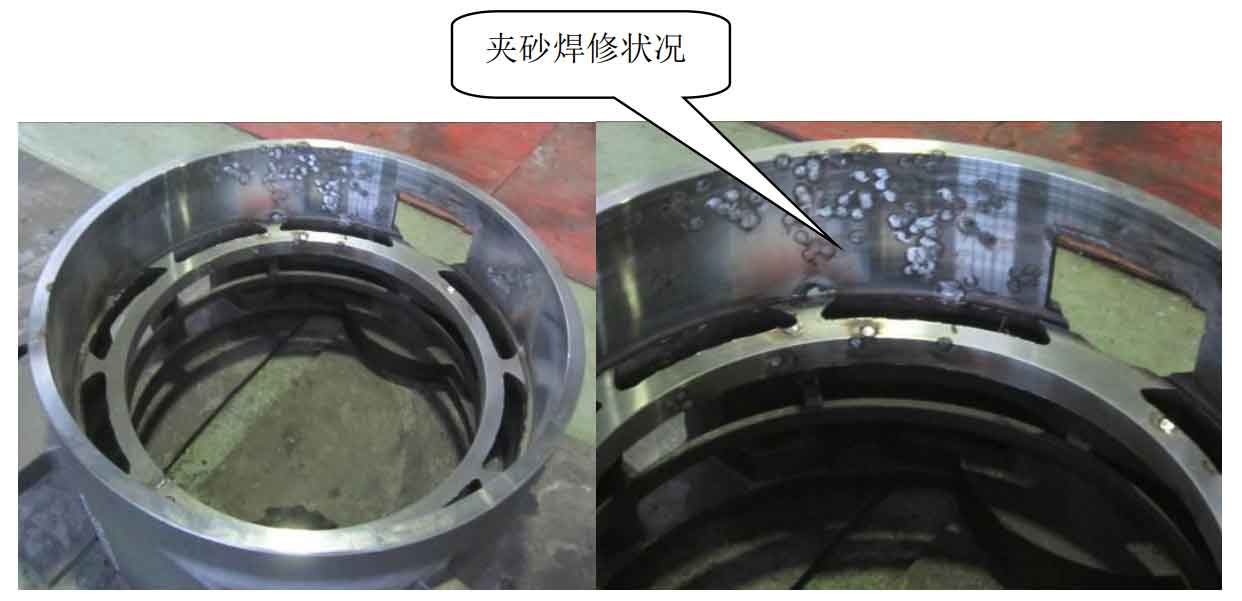