Ordinary clay sand molding is adopted, and the molding process includes mold processing, sand mixing, sand pounding, box turning, vent hole, mold lifting and finishing. The test bar molds with a height of 300 mm and diameters of Φ 10 mm, Φ 20 mm, Φ 30 mm, Φ 40 mm and Φ 50 mm were prepared, and the corresponding casting modulus MS were (CM): 0.25, 0.50, 0.75, 1.00 and 1.25, respectively.
After the casting mold of the test bar is solidified and cooled, the part below 40mm away from the bottom of the test bar is cut off, and the part 30mm away from the top of the test bar which plays the role of feeding riser is cut off. The rest parts are the sampling parts of this test. The casting process and sample cutting parts of the test bar are shown in the figure. At the same time, the specimens for austenitizing and water quenching treatment were taken from the core of the test bar, and the isothermal quenching sample and tensile test bar were taken outside the test bar.
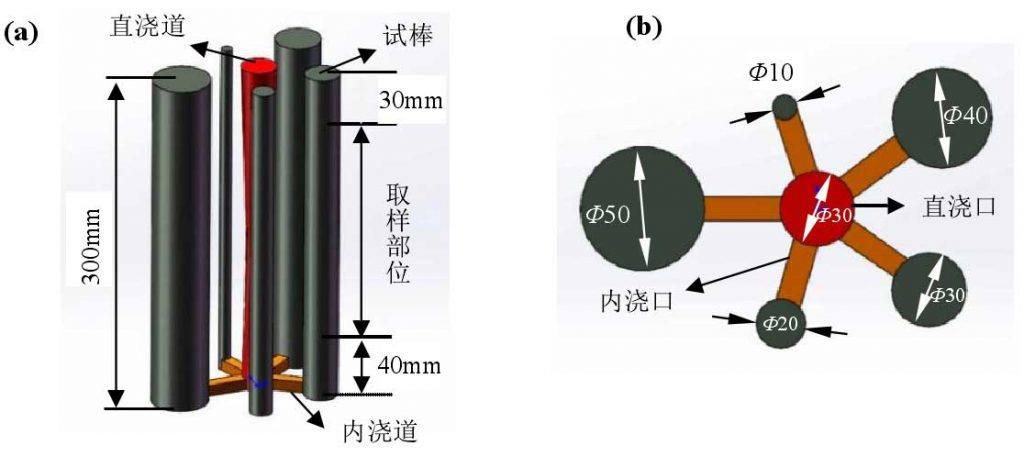
After the molten iron is melted, the molten iron is quickly lifted to the side of the sand mold by hand, and the molten iron is evenly poured and inoculated with the flow. The bottom injection method is adopted for the test bar. After the molten iron is filled with the sand mold cavity, the surface of the test bar is quickly covered with dry sand. Finally, after the test bar is solidified and cooled to room temperature, it is unpacked and cleaned, and then the test bar is machined according to the required sample specification.