As the original casting process adopts bottom pouring process, as shown in Figure 1 Through comparative analysis, it is found that the product belongs to the complex cavity thin-walled part, which is difficult to process, adopts three box modeling, and has poor filling ability of molten iron, which is easy to produce shrinkage defects at the position of the inner half shaft. During the solidification process of the axle housing, due to the temperature difference in the mold cavity, there is an isolated liquid phase area at the position of the axle housing oil seal seat, which makes it impossible to realize at this position At the same time, solidification causes shrinkage defects. In addition, the original pouring temperature of the axle housing is 1550 ℃, the original pouring time is 25s, and the box is opened below 200 ℃.
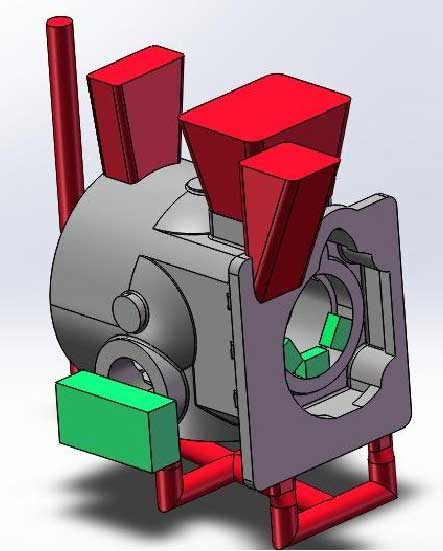
As can be seen from Figure 1, the red part is the gating system and riser feeding system, and the green part is the chilled iron solidification and chilling system. This process adopts bottom pouring. The main disadvantages are that it is difficult to pour and mold, resulting in local shrinkage defects.
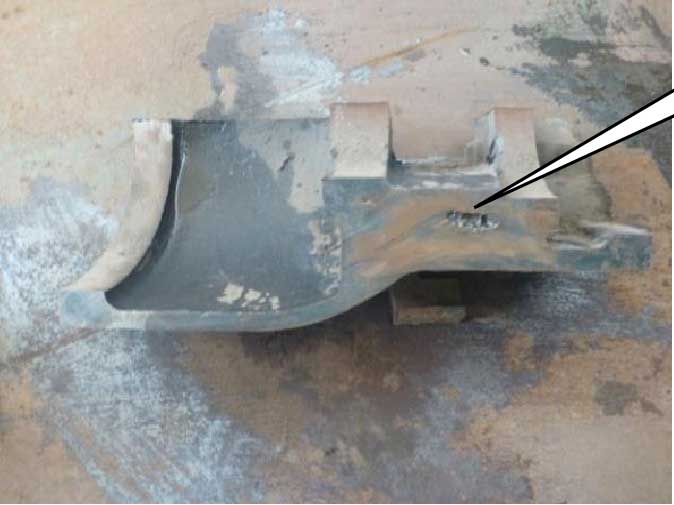
As shown in Figure 2, the product belongs to complex box thin-walled parts. For cast steel products, it is difficult to control the defects, which brings huge pressure in the subsequent processing, inspection and sealing test. The first inspection pass rate is less than 30%, and the defects are mainly distributed in the internal half shaft depression.