In this design, a new aluminum silicon alloy is used as the shell casting material. By adding Al-10Sr modifier and a proper amount of Ni alloy element to the aluminum silicon based ZL101A alloy, the alloy grain refinement modification is realized, and the chemical composition of the aluminum silicon based alloy material is prepared. The intermediate alloy particles of the material are helpful to refine the grain size of the casting and improve the quality and performance of the aluminum silicon alloy casting.
The outline dimension of the hydraulic pump shell is 167 mm wide, 248 mm long and 114 mm high, with the thinnest wall thickness of 5 mm and the thickest wall thickness of 20 mm. There are 5 groups of stiffener structures on both sides, which can increase the strength and rigidity without increasing the wall thickness. The structure shape is shown in Figure 1. The shell will adopt the low-pressure casting process. The symmetrical surface of the shell casting structure shall be placed vertically. The cylindrical double direct runner with a length of 100 mm and a diameter of 10 mm shall be used for casting. There is no need to set the transverse gate and internal gate. The pouring system will guide the molten metal into the mold cavity after smelting to improve the pouring efficiency. During the casting process of the hydraulic pump shell, the exhaust groove of the exhaust system is set to 0.15mm in depth and 20 mm in width, so that the gas in the cavity can be discharged out of the mold as much as possible during the filling process of the liquid metal, so as to reduce and prevent the formation and generation of porosity defects in the casting.
The filling speed is related to the flow state and temperature distribution of liquid metal in the cavity, so it affects the quality of castings. The filling speed is too fast, the liquid metal flow is not stable during the filling process, and the gas in the cavity is too late to be discharged, which will form back pressure and hinder the liquid metal filling. The slow filling speed and the stable filling of liquid metal are beneficial to the elimination of gas in the cavity, but the temperature difference of castings increases. If the filling speed is moderate and slow, it will be beneficial to the feeding of castings, so as to avoid the defects such as shrinkage cavity and porosity, and to the solidification of castings according to the corresponding sequence. So it is the key requirement to improve the quality of castings and produce high quality castings to set the proper pouring speed. Under the condition of full mold, the lower limit of mold filling speed is better, which can avoid spray splashing, disordered flow and oxidation slag during filling. The calculation formula of filling speed is:

Where: V filling min is the average rising speed (along the casting height) of the molten metal in the mold (minimum allowable), mm / S; h is the height of the casting, mm; δ is the wall thickness of the casting, mm; t casting is the pouring temperature of the alloy liquid, ℃. According to formula (1), the pouring speed is 44 mM / s.
The filling process of aluminum alloy casting needs to ensure the gas pressure on the metal surface. According to the structure and type of the casting, its size directly affects the casting process and molding process, has a very important impact on the internal quality of the casting, and is an important technical parameter of low-pressure casting. When the casting is in low pressure casting, the filling pressure value is generally calculated according to Pascal principle as follows:
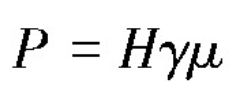
Where: P is the filling pressure, MPa; h is the distance between the top of the cavity and the metal level in the crucible, mm; γ is the weight of the metal liquid, N / mm3; μ is the filling resistance coefficient, generally 1.2-1.5. According to the above formula, the filling pressure is 3.34 × 10-3mpa. Because the exhaust hole is set in the casting mold, 0.1013 MPa is needed to be added to the base pressure, so the low-pressure casting pressure is 0.1047 MPa.