In view of the problems existing in the current casting process, three test schemes are designed to improve the process performance by increasing the flow performance of castables and changing the cooling rate, and comparative experimental studies are carried out.
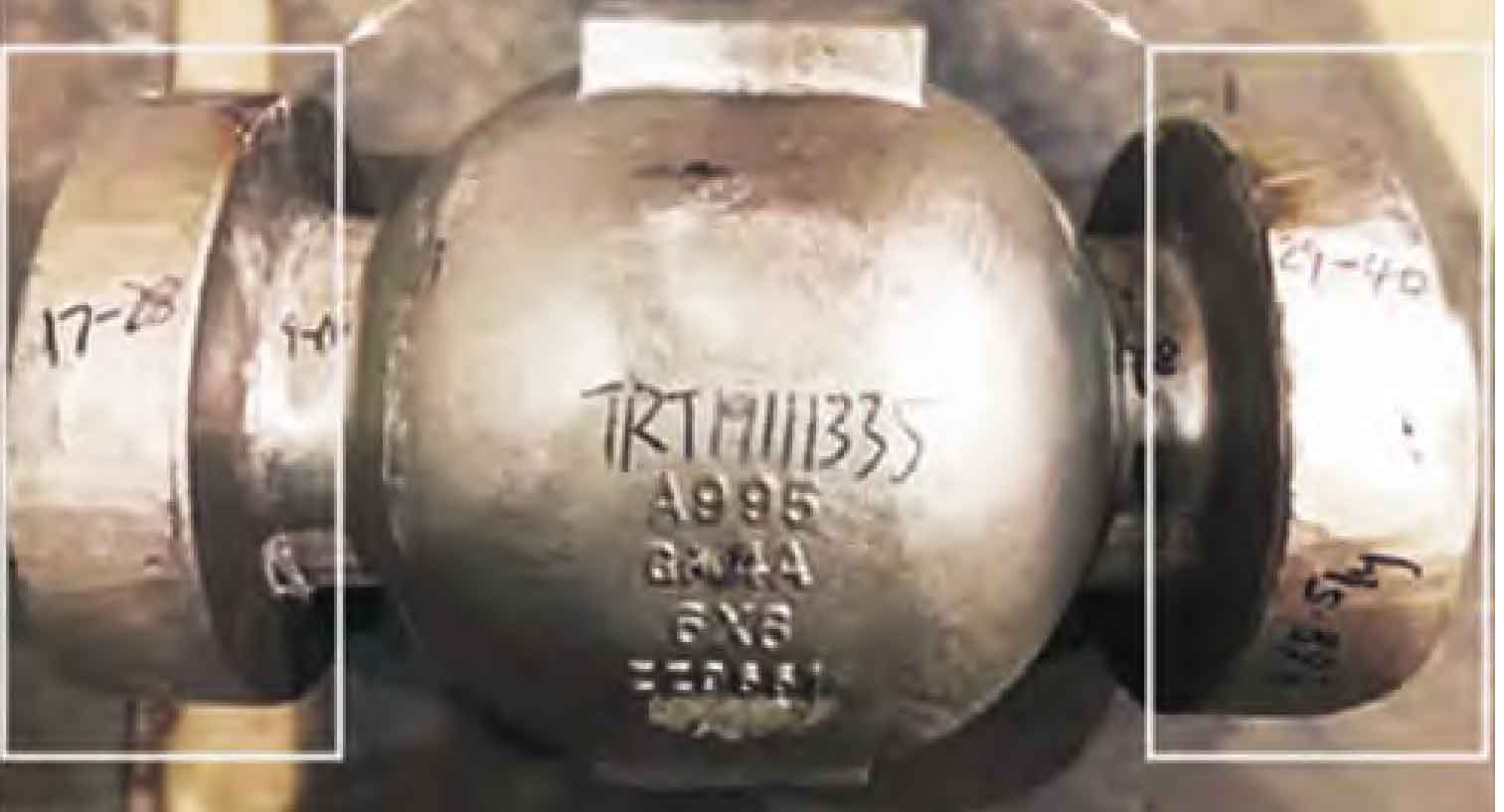
(1) Test plan 1: increase the number and area of gating risers. In the original process design, the pouring and riser positions are the inlet flange, the outlet flange, the top of the rib plate and the bottom of the rib plate. Now, a connecting riser is added at the side of the entrance and exit, and the original 4 gates and risers are increased to 5 to improve the timeliness of filling the mold with the castable, thus reducing the casting defect rate.
Considering that the defect type in the initial plan is mainly shrinkage defect, it is proposed to further enhance the flow performance of castables and reduce the occurrence of defects by expanding the pouring riser area. Considering that the valve body of this casting is made of super dual-phase steel, which is difficult to cast. This is because dual-phase steel has a high N content, and the solubility of N decreases when the metal solidifies. Therefore, gas will precipitate during the casting process, so the casting is prone to air holes. In terms of control, the process needs to be optimized, so the riser should not be set too large. To sum up, increasing the riser area by 10% can ensure good casting quality while meeting the flow area.
(2) Test plan 2: place cold iron in the middle chamber of the valve. This process plan is to accelerate the cooling and solidification rate of the inner cavity. Since the liquid metal will have non-synchronous cooling problems in the process of entering the interlayer, for example, after the riser design is added to the upper and lower parts of the valve, the rib plate thickness is thinner than the inner cavity, resulting in its cooling speed will be faster than the inner cavity during the flow process, so the feeding design of the casting inner cavity is particularly important. Placing chills in the inner cavity can effectively compensate for the volume shrinkage of liquid and solid during the solidification process of the casting, thus avoiding the cavity shrinkage defects caused by the cooling sequence.
(3) In test plan 3, cold iron shall be placed in the middle cavity of the valve while increasing the number and area of the gating and riser. Improve the process performance simultaneously by increasing the flow performance of castables and changing the cooling rate.