For three different processes, the MAGMA casting simulation software is used to simulate the valve casting process, and the results are shown in Figure 1-3.
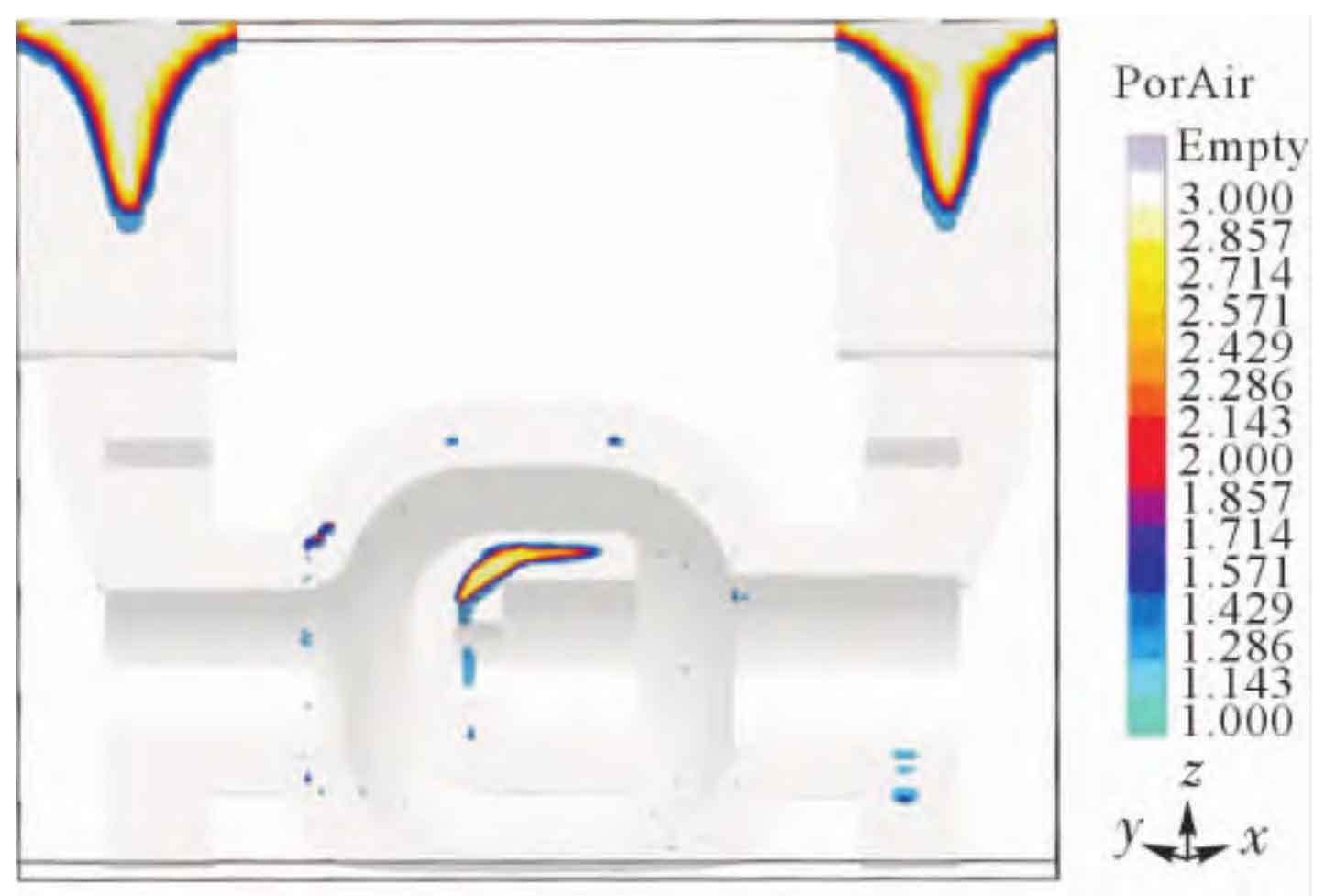
Figure 1 is the simulation result of test plan 1. It can be seen that under the valve casting process, about 10% of the casting defects still exist in the middle cavity of the valve casting. This is because although the number and area of the gating and riser are increased, the flow channel of the castable is expanded, and the molten metal still has the non-synchronous cooling problem in the process of entering the sandwich layer, resulting in the untimely shrinkage of the middle cavity, Then, the problem of cavity defect is caused.
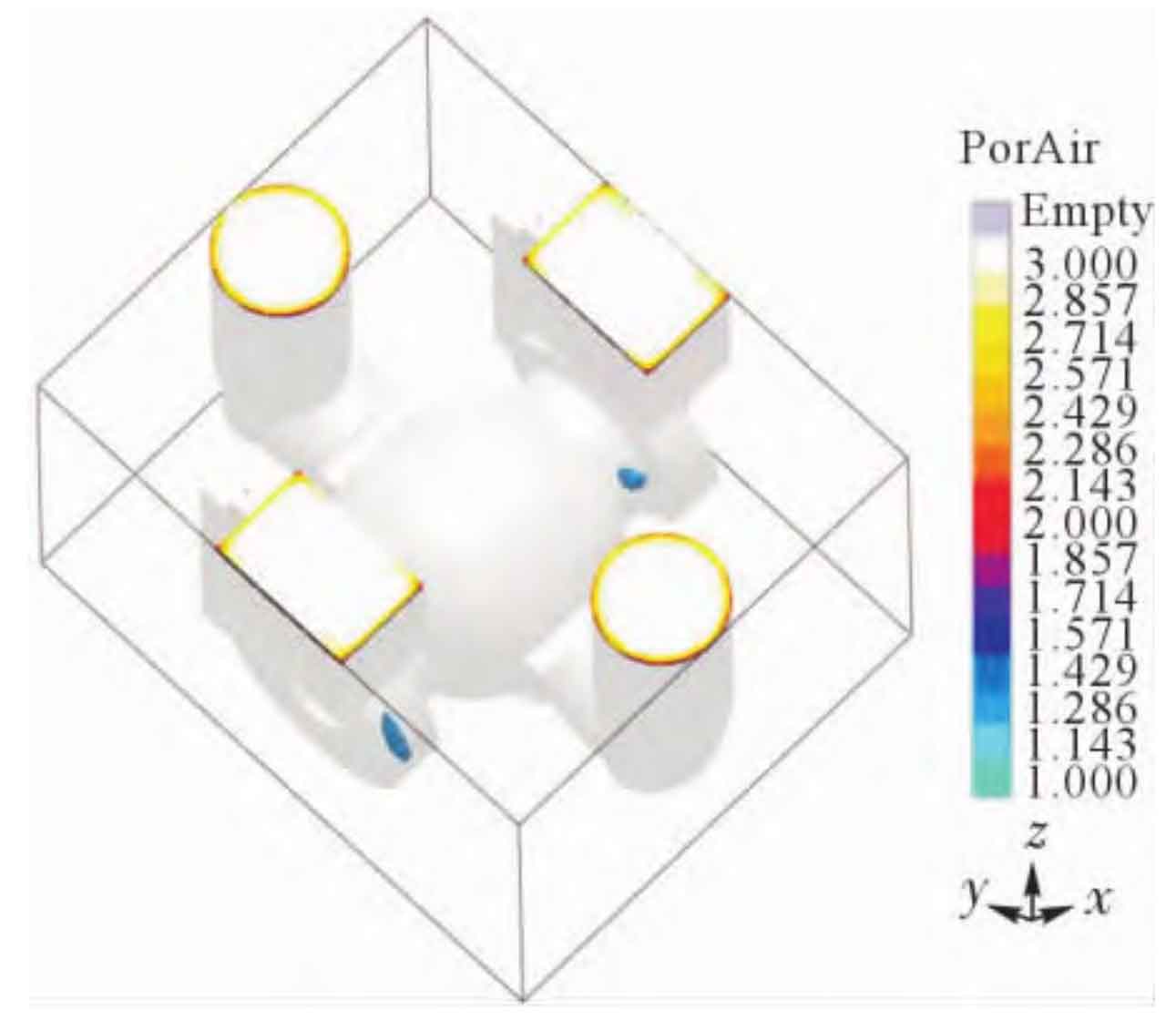
Figure 2 shows the simulation results of test plan 2. As shown in the figure, this defect does not occur in the valve cavity, but only at the inlet and outlet flanges. This is because the placement of the middle cavity chill can effectively compensate for the volume shrinkage of the liquid and condensed solids produced during the solidification process of the valve casting, so as to avoid the cavity shrinkage defects caused by the cooling sequence. However, the flow capacity of the inlet and outlet gating system has not been substantially improved, so the problem of the timeliness of the castable filling the mold has not been completely solved, and there are still about 10% defects on the valve shell.
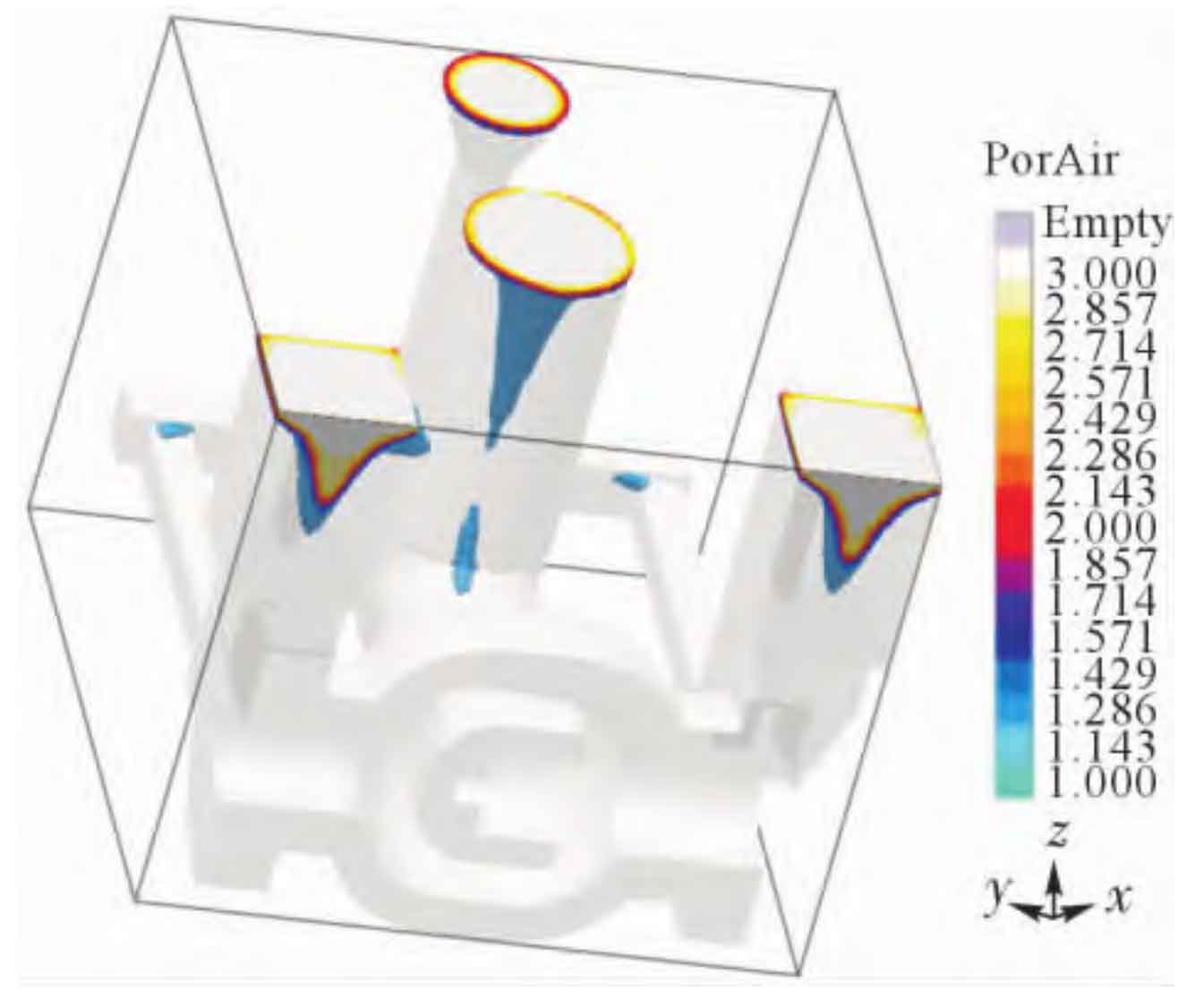
Figure 3 shows the simulation results of test plan 3. There are no defects on the valve body. Compared with the original valve casting process plan, the defect rate decreases by about 20%, which greatly improves the pressure bearing capacity of the valve casting. This is because in test plan 3, cold iron is placed in the middle cavity of the valve while increasing the number and area of gating and riser. Improve the process performance simultaneously from two aspects of increasing the castable flow performance and changing the cooling rate, thus ensuring the casting success rate of the valve body.