For the casting process design of the support table parts, first of all, from the part drawing, read the drawing, then analyze its mold type, core structure and parting surface selection, and then gradually determine the casting process parameters, design the pouring system.
In this design, the casting process drawing is undoubtedly very important, because it marks a series of essential parameters in casting, such as parting surface, machining allowance, shape and size of sand core, pouring system, etc. I also encountered many problems in the design, especially the selection of various parameters. The choice of information directly affects the strictness and preciseness of the subject design. Through discussion with teachers and students, I finally got the result.
Through this course design, I found that I did not have a good command of the knowledge I learned. I still need a lot of efforts to make a comprehensive understanding. I need to be more serious in my future study.
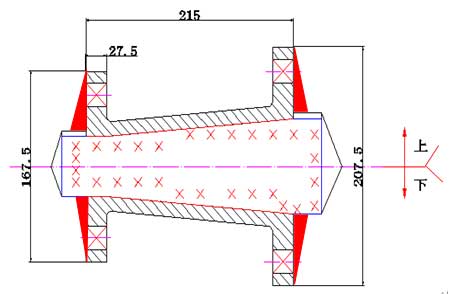
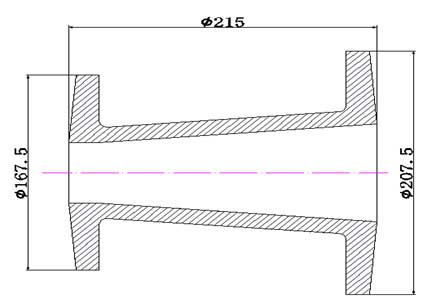
Casting process card
Casting name |
Material grade |
Production type |
Blank quality |
Minimum wall thickness |
|||||||||||
Supporting platform |
HT150 |
Small batch |
8.6kg |
12mm |
|||||||||||
modelling |
Modeling method |
Sand box casting, two box molding |
|||||||||||||
Internal dimension of sand box /mm |
Specifications |
long |
wide |
high |
Fastening method |
||||||||||
Upper box |
250 |
220 |
130 |
/ |
|||||||||||
Lower box |
250 |
220 |
130 |
||||||||||||
Sand mold drying |
Drying temperature\℃ |
Drying Time\h |
Method |
||||||||||||
300 |
5 |
Drying oven |
|||||||||||||
Size of pouring and riser\mm |
Runner quantity |
long |
wide |
high |
Cross section area |
||||||||||
1 runner |
200 |
22 |
35 |
9.97c㎡ |
|||||||||||
2 internal sprues |
50 |
52 |
17 |
8.90c㎡ |
|||||||||||
1 sprue |
150 |
18 |
18 |
10.24c㎡ |
|||||||||||
Pouring process specification |
|||||||||||||||
Oven temperature/℃ |
Pouring temperature/℃ |
Pouring speed/sec |
Cooling time/h |
||||||||||||
>1300 |
>1250 |
35~55 |
>10 |
||||||||||||
Heat treatment process |
Heating for 2 ~ 4H to 550 ± 20 ℃, heat preservation and soaking for 1 ~ 2H, then slow cooling |