For the same casting, the pouring time is different when the pouring speed is different. If the pouring speed is too small, the mold filling time will be too long, which is easy to cause casting defects such as insufficient pouring; if the pouring speed is too large, it will cause the metal liquid to flow violently in the mold and produce spraying phenomenon, which will lead to slag inclusion or iron beans, and the metal liquid with too high speed will cause great impact on the sand mold wall, which is easy to destroy the mold and produce sand holes, etc Casting defects and casting speed also have an effect on the exhaust sequence of the cavity.
The control of pouring speed is based on pouring time constraint. The calculated theoretical pouring time is 2.38s, and the corresponding pouring speed is 1m / s. However, there is a deviation between the theoretical pouring time and the actual pouring time, and the calculation formula is also derived based on the actual production experience. The spiral bevel gear is a small steel casting with complex structure, which is rarely used in actual casting production. Therefore, this paper studies the influence of this factor on the forming quality of the spiral bevel gear casting with the pouring speed (corresponding to the pouring time) as a variable.
The simulation results show that, due to the strong feeding ability of the insulating riser, the influence of pouring speed on the shrinkage cavity defects of the spiral bevel gear casting studied in this paper is relatively small; moreover, when the central top injection pouring scheme is adopted, the metal liquid in the cavity is filled stably, and the air and slag can float to the upper surface of the gear blank; but the air pressure distribution on the upper surface of the casting is not uniform at different pouring speeds In the same way, if the air pressure value is too large, it means that there is a lot of residual air, which is easy to cause casting defects such as porosity.
The figure shows the air pressure distribution on the upper surface of the casting at different pouring speeds. It can be seen from the observation of the figure that the air pressure value and distribution on the upper surface of the casting vary greatly with the pouring speed. As shown in Figure 5.11 (E), when the pouring speed reaches 1.1m/s, the air in the gear blank mold is not all squeezed into the insulating riser, but a considerable part of the air remains in the mold cavity, resulting in a very serious air pressure distribution on the upper surface of the casting and a large local pressure value, which will seriously affect the metal structure state of the upper surface of the casting. When v = 0.8m/s, the air pressure distribution on the top surface of the casting is the smallest, and the residual air has the least influence on the quality of the casting. Therefore, the best pouring speed and time of the central top pouring of the driven spiral bevel gear casting are 0.8m/s and 2.97s respectively.
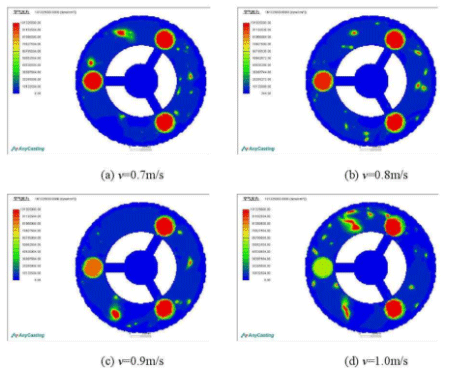
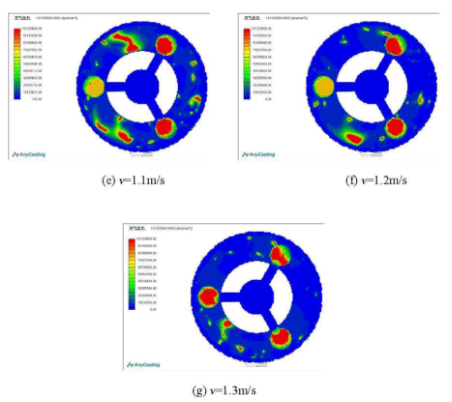