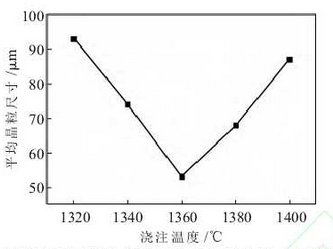
Figure 1 shows the average grain size curve of Superalloy samples prepared at different pouring temperatures. It can be seen from the figure that with the increase of pouring temperature, the microstructure of the sample is improved, and the average grain size first decreases and then increases. When the pouring temperature is 1320 ℃, the average grain size of the sample is the largest, which is 93 μ m; when the pouring temperature continues to increase, the average grain size of the sample decreases continuously; when the pouring temperature is 1360 ℃, the average grain size of the sample is the smallest, which is 53 μ m, which is 43% less than that of the sample prepared at 1320 ℃; When the pouring temperature continues to increase, the grain coarsens and the average grain size increases compared with that at 1360 ℃.
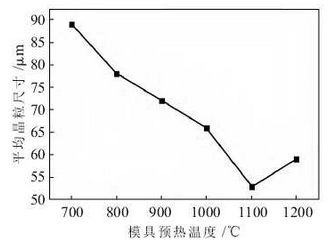
Figure 2 shows the average grain size curve of Superalloy samples prepared at different mold preheating temperatures. It can be seen from the figure that with the increase of die preheating temperature, the microstructure of the new superalloy used for automobile turbocharger turbine is improved, and the average grain size first decreases and then increases. When the mold preheating temperature is 700 ℃, the average grain size of the sample is the largest, which is 89 μ m; when the mold preheating temperature continues to increase, the average grain size of the sample decreases continuously; when the mold preheating temperature is 1100 ℃, the average grain size of the sample is the smallest, which is 53 μ m, which is 40.4% less than that when the mold preheating temperature is 700 ℃, The average grain size of the sample is larger than that of the mold prepared at 1100 ℃.
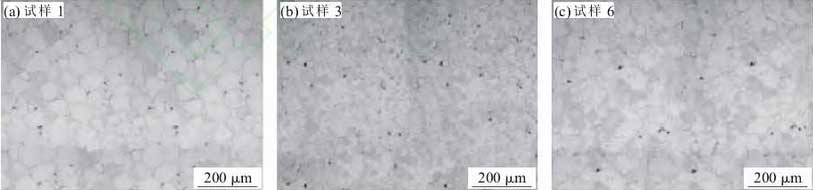
Figure 3 shows the microstructure of three different samples. According to Fig. 3, the microstructure of the three superalloys has white dendrite structure and black solute, but the grains in Fig. 3 (a) (sample 1) are the coarsest, and there are a lot of black solute enriched phases. In Fig. 3 (b) (sample 3), the dendrite spacing and dendrite arm are significantly reduced, and the grains are greatly refined. However, the grain size of Fig. 3 (c) (sample 6) is between sample 1 and sample 3, and the dendrite arm is smaller than that of sample 1 and larger than that of sample 3. In a word, in order to improve the wear resistance and high temperature oxidation resistance of superalloy for automobile turbocharger turbine, the casting process parameters are optimized as pouring temperature 1360 ℃ and mold preheating temperature 1100 ℃.