The pump casing is the main part of the water pump, which is mostly made of dual-phase steel. Different grades of water pumps have huge differences in the structure of the pump casing. The single suction pump casing is the research object, and the casting process of the pump casing is designed. At present, the output rate of the mainstream casting process of the pump casing is less than 50%. Although it has a good yield, the low output rate seriously raises the manufacturing cost, and further damages the competitiveness of the product, The new pump casing casting process aims to improve the process yield and help customers gain cost and profit advantages.
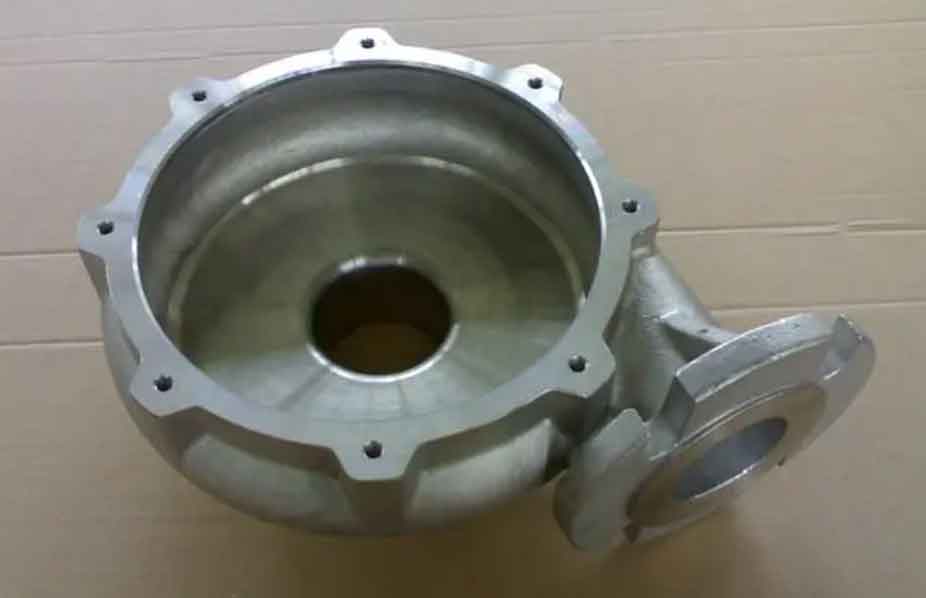
The following achievements have been achieved in the process development of single-stage pump casing:
(1) The yield of the process is greatly improved. The process yield of the original process is 47%, while the new process reaches 68%, which means that the cost of a single piece of material is reduced by 44%.
(2) The working hours of grinding and processing have been greatly reduced. Since a large number of subsidies are abolished, and the risers are all set on the processing surface, the residual of the risers after air gouging and cutting is very small, which reduces the cleaning and grinding workload by about 60% and reduces the processing hours by 3h.
(3) The application prospect of simulation technology in the field of pump casing casting is proved. In the past, the casting process design of pump casing often relied on the experience of process technicians to predict the defect location of pump casing castings and design water risers and cold irons, which often required years or even decades of accumulation and limited accuracy. Relying on simulation technology, now technicians can intuitively observe the mold filling and solidification process of pump casing castings, accurately predict air entrainment, slag inclusion, shrinkage porosity, cold shut and other defects, and take measures to avoid them in advance. For example, in this paper, it is difficult to find the critical point by relying on trial and error method, and the purpose of eliminating defects can not be achieved.
(4) Mechanized core making means. In the past, the company used manual core making for cylinder heads, and the molding materials included Hezhi sand and Baozhu sand. Hezhi sand needs 2 sets of molds and 4 workers to produce 14 cylinder heads per day, while Baozhu sand needs 4 sets of molds and 8 workers. At the same time, due to the randomness and error of manual operation, the precision of sand cores is low, and defects such as air holes, sand sticking and core breaking occur from time to time. Under the condition of mechanized core making, only 2 workers are needed to complete the same output, and the quality of sand cores is stable.
The above achievements have effectively reduced the production cost, explored the technical route of sustainable development, and greatly enhanced the competitiveness of the company in the field of pump casing castings.