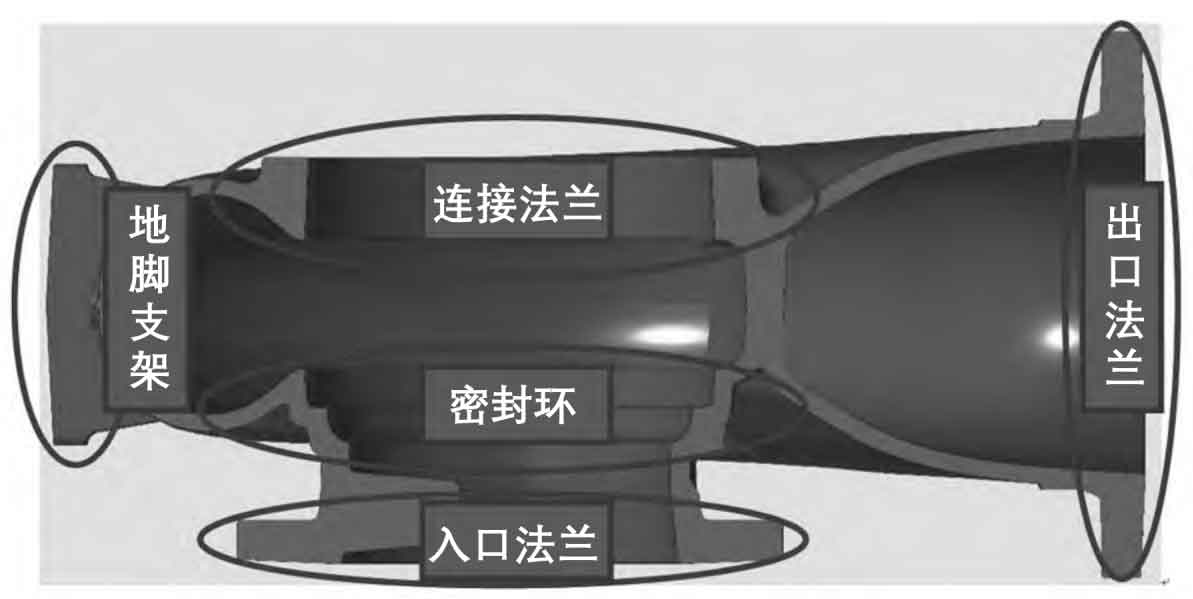
The dual-phase steel pump casing has the common characteristics of cast steel: high melting point, poor fluidity, large shrinkage, easy oxidation and inclusion. Generally speaking, it is a material with poor casting process. The design of the pouring system of the pump casing steel castings has the following requirements:
(1) Low temperature rapid casting process should be adopted. On the one hand, the lower pouring temperature of the pump casing steel casting can reduce the overall shrinkage of the pump casing casting, which is beneficial to the internal quality, crack tendency and scale control of the pump casing casting; On the other hand, the faster pouring speed of pump casing steel castings can effectively reduce the temperature loss of molten steel and reduce the probability of fire and inclusion problems.
(2) The design of the pouring system of the pump casing steel castings shall be open. According to the author’s experience, the closed gating system should not be adopted for the pump casing steel casting products. The closed gating system cooperates with the leaky ladle. Excessive mold filling pressure will increase the flow rate of the core of the choke section, but the flow rate of the cavity surface of the choke section will decrease, which will easily lead to the solidification of the molten steel near the cavity surface of the choke section layer by layer and eventually block the gating system. Therefore, for the pump casing steel castings, especially the materials with poor fluidity such as dual-phase steel, Open gating system shall be selected.
(3) Disperse water. The pump casing has a complex structure and a large size span. Concentrated water inflow can easily lead to overheating in the inner nozzle area, increase the crack tendency, and increase the possibility of fire formation due to rapid temperature loss at the distal end. Therefore, it is advisable to disperse water inflow.