Wheel is one of the important parts of mining flat car. It needs to bear large alternating stress and bending stress when working. This special working condition often leads to bending, cracks, wear and other problems. Therefore, higher requirements are put forward for the wheel casting process, and the castings are not allowed to have casting defects such as shrinkage porosity, shrinkage cavity, cold shut and so on. Traditional casting production mainly depends on the actual work experience of technicians, which is lack of theoretical basis. By combining computer technology with casting technology and using numerical simulation technology, the defects of castings can be visually displayed, so as to optimize casting process parameters, reduce production costs and shorten production cycle.
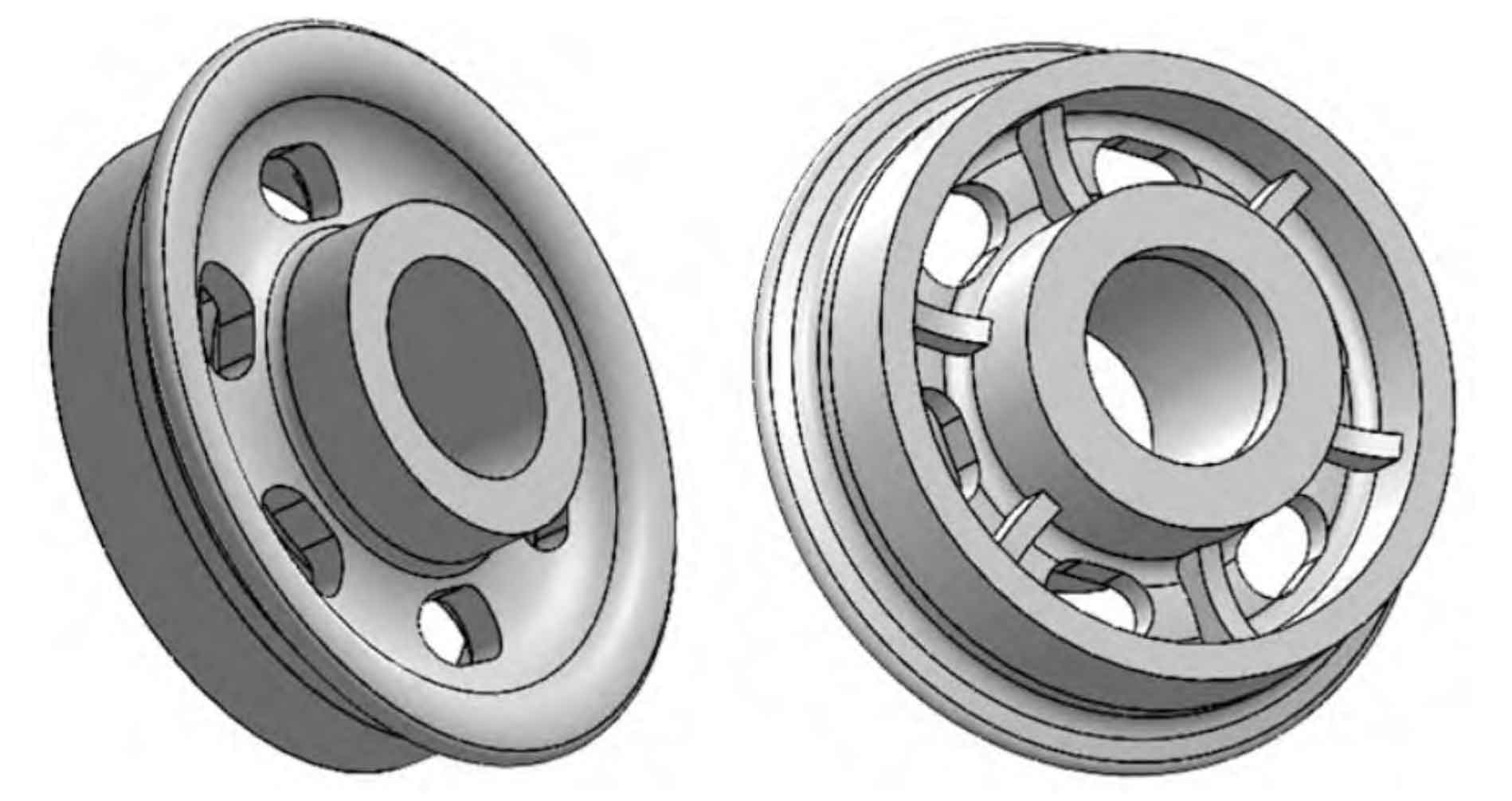
Tang Guiji and others conducted finite element analysis on the structure of aluminum alloy wheel hub, studied the influence of natural frequency and vibration mode on the fatigue life of wheel hub, and verified the most vulnerable part of wheel hub. Zhou Zheng [5] et al. Studied the wheel hub forging and analyzed the changes of microstructure at three different points. Wang Wei [6] et al. Conducted numerical simulation on the wheel hub and studied the influence of shrinkage porosity, shrinkage cavity, temperature field and other factors on the quality of wheel hub castings. The wheel casting process was improved by adding chill and insulation ring. Zhou Jie et al. Conducted numerical simulation of aircraft hub, proposed the forming process of gross pressing, pre pressing and final pressing, and analyzed the forming defects of the process test results.
(1) On the basis of the original pouring system of mining flat car wheels, risers and external chill are added to effectively avoid the generation of hot spots in wheel castings. By feeding the molten metal of the wheel casting in time through the riser, the casting defects of shrinkage cavity and shrinkage porosity are eliminated, and the compactness of the wheel casting is effectively improved. The joint action of riser and chill realizes the sequential solidification of Wheel Castings from bottom to top, from outside to inside, and improves the production quality of wheel castings.
(2) Through the production verification of the improved scheme, the microstructure and mechanical properties of the castings meet the requirements, which proves that the scheme is effective and feasible.
ProCAST software is used to simulate the filling and solidification process of wheel castings. The simulation results are used to predict the location and size of defects in Wheel Castings and analyze the causes. The gating system is optimized to improve the mechanical properties of Wheel Castings and improve the quality of wheel castings.