Water hammer relief valve is the core product to prevent the occurrence of water hammer hazards, and is often used in the long-distance transportation, storage and transportation industry of liquid media. This type of valve has the characteristics of large discharge capacity and high pressure. The valve needs to be opened instantaneously when it is open to release a large amount of overpressure medium to ensure the safe and stable operation of the entire pipeline.
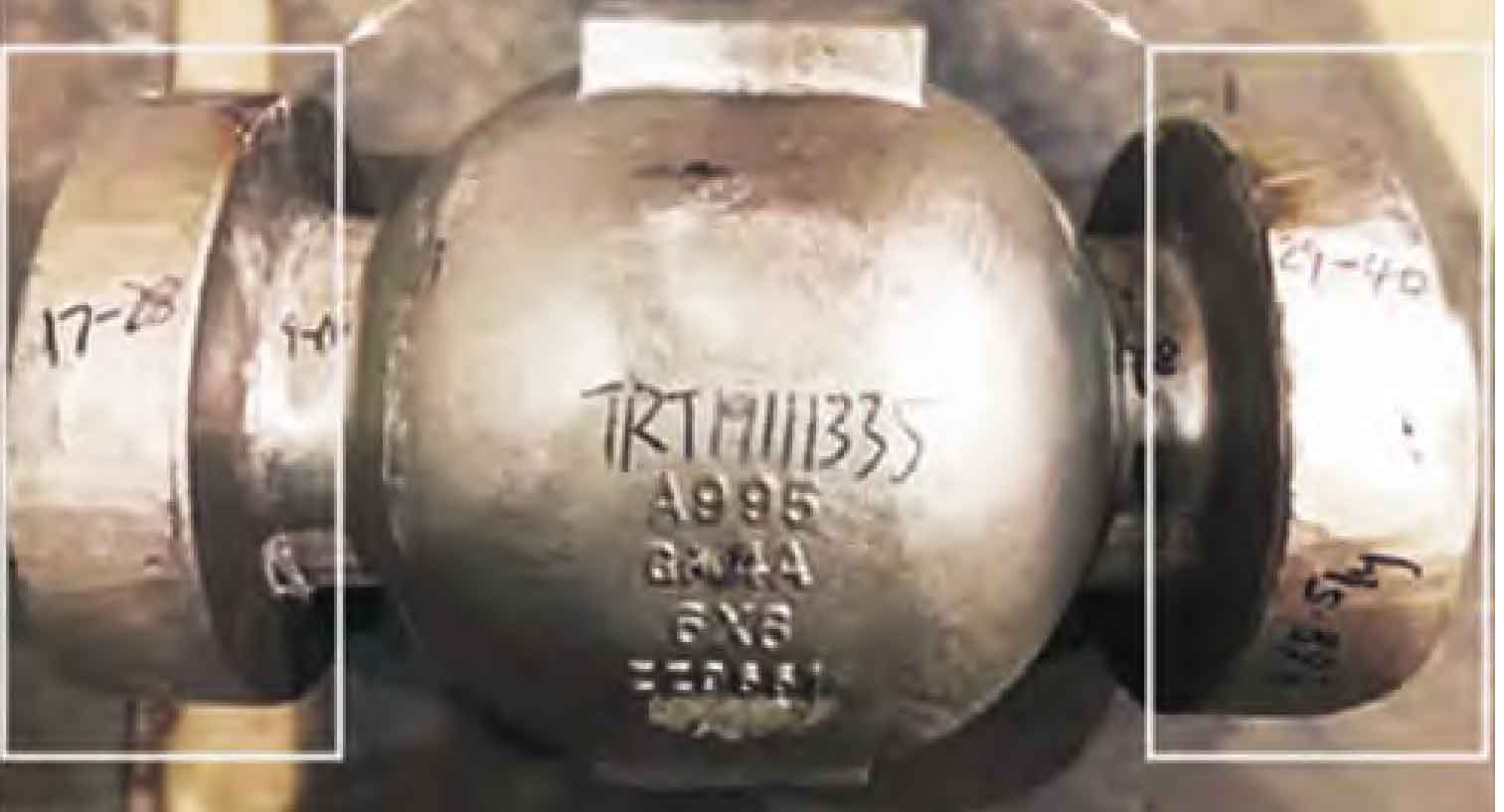
(1) For the existing high pressure special material castings, the MAGMA casting simulation results show that under the existing casting process, there are many shrinkage cavities and porosity defects in the valve body inner cavity, with the defect rate of about 20%.
(2) The MAGMA casting simulation results show that the inner cavity defects can be basically eliminated after optimization, and the defect rate is reduced by about 20%, which greatly improves the bearing capacity of the casting.
(3) The trial production of castings was carried out according to the improved process, and no pressure leakage occurred. At the same time, the position of the inlet and outlet flanges were subject to radiographic inspection according to ASMEB16.34 standard, and the inspection results met the standard requirements.
The medium used by the water hammer relief valve is usually corrosive. When it is used under medium and high pressure conditions, the nominal pressure is about 26 MPa and the nominal diameter is more than 150 mm. Therefore, its pressure bearing performance is higher than that of conventional valves. In order to meet the requirements of its instantaneous discharge capacity, the valve is usually designed into three parts: front, middle and rear. Due to the different functions of these three parts, the structural design is different, and the wall thickness requirements at the inlet and outlet are also different. The valve body is of non-uniform and equal wall thickness, which leads to large differences in the wall thickness at the front, middle and rear of the valve. In addition, there is a special interlayer with pressure-bearing structure inside the middle cavity, which brings greater difficulties to the traditional conventional casting process. At present, there are few articles about the casting process of this kind of valve at home and abroad, and the casting experience in relevant fields can not be used for reference. The common casting process can not fully adapt to the structure, and the one-time casting pass rate is low. Therefore, it is urgent to optimize the casting process of such valves. The existing casting process is simulated by using the MAGMA casting simulation software, and the casting process system and cooling process system are optimized to provide reference for further improving the casting process stability of the water hammer relief valve body.