The casting properties of ductile iron have the following characteristics
① The content of sulfide and oxide in molten iron is high. In addition, oxides are easily produced if exposed to air and gas.
② Graphitization expansion is easy to cause casting swell, and the dimensional accuracy is easily affected.
③ Slag inclusion is easy to occur in thick wall.
④ The riser is easy to produce shrinkage cavity.
⑤ It is troublesome to clean the casting.
⑥ The quality of exhaust gas from mold and core has a great influence on whether the sound casting can be obtained.
⑦ The casting is easy to produce slag hole, shrinkage cavity, air hole, pinhole and inclusion.
- Material requirements
The material meets the requirements of en-fhs-700-2 pearlite ductile iron; the material properties of single cast test bar meet the minimum requirements of iso1083-2004 national standard, that is, tensile strength 700 MPa, yield strength 420 MPa, elongation 2%.
Because of the slow cooling, the tensile strength of the thick part of the casting is usually low. The material properties of bulk sampling must reach the minimum values, which are tensile strength 630 MPa, yield strength 360 MPa and elongation 1%。
- Chemical composition
C. Si, Mn, s and P are the five basic elements of cast iron, which are proportioned according to the requirements of national standard QT700-2. Considering the particularity of piston, it is necessary to increase alloy elements which can enhance material strength and refine microstructure.
Cu is an element that promotes the graphitization of eutectic phase, and its graphitization ability is equivalent to 1 / 10 ~ 1 / 5 of that of silicon. When Cu exceeds its solid solubility limit, it is often distributed in cast iron as micro or ultramicro particles. Cu makes the structure compact, refines and improves the uniform distribution of graphite, which can not only reduce the white cast tendency of cast iron, but also reduce the critical temperature of austenite transformation, refine and increase pearlite, which has a favorable effect on the section sensitivity. Cu has the tendency to strengthen ferrite and pearlite of cast iron, which can increase the strength of cast iron. The tensile strength and bending strength of cast iron are directly proportional to the content of Cu, especially in low carbon cast iron. In general cast iron, the hardness can be increased when the mass fraction of Cu is between 3.0% and 3.5%, but when the cast iron has the tendency to form white cast iron or there is hard spot of free carbide, the hardness will be reduced by adding Cu. Therefore, the commonly used amount of Cu is less than 1.0%.
- Smelting process
The chemical composition of nodular iron piston should be proportioned in strict accordance with the composition requirements, and the material should be weighed according to the calculation value of proportioning, and then the charge of each heat should be placed separately for standby.
Melting process is an important part of casting process and the premise of casting process. The quality of casting is directly determined by the quality of melting process. The specific smelting process is as follows:
① 500 kg medium frequency induction furnace is used.
② The furnace charge shall be stacked according to the composition, and the type and heat number of the returned material shall be indicated.
③ When the charge is put into the furnace, the excessive flash burr shall be removed, and the charge shall be cut into pieces ≤ 40 mm × 60 mm × 80 mm.
④ The furnace charge with serious corrosion, sand sticking and oil pollution shall be put into the furnace after passing the treatment.
⑤ Check the furnace before charging.
⑥ When charging, small pieces are put into the lower part, large pieces are put into the upper part, and the middle part is filled with broken materials. The carburized graphite is evenly loaded into the furnace.
⑦ Melting is carried out at maximum power. With the melting of the charge, iron bars are often used to push the charge to prevent bridging.
⑧ According to the melting degree, the remaining metal charge shall be added, and all alloy furnace charges shall be baked above 400 ℃.
⑨ The melting temperature is 1 540 ℃ and the outlet temperature is 1 500 ℃.
- Spheroidization
The hot metal was spheroidized by the method of flushing. Add 7.5 kg spheroidizing agent; preheat the treatment ladle to 700 ℃ and control the hot metal temperature at 1 450-1 500 ℃; put the block spheroidizing agent into the pit at the bottom of the treatment ladle; flush 2 / 3 of the molten iron into the treatment ladle, and then flush the remaining molten iron when the boiling of the molten iron is finished; after the spheroidizing treatment, add the slag collector to thoroughly remove the slag.
- Inoculation
Due to the addition of spheroidizing agent, the supercooling tendency of ductile iron increases. In order to avoid carbide precipitation and promote the precipitation of a large number of fine and round graphite balls, the hot metal is inoculated after spheroidizing treatment. 75fe Si was used to inoculate the molten iron in the ladle, the remaining inoculant was poured into the ladle, the molten iron was fully stirred, and the slag was completely removed by adding straw ash after standing for a certain time, and the amount of inoculant was 5 kg.
- Metallographic examination of nodular iron piston
Metallographic examination of as cast test bar is shown in the figure. The graphite morphology with spheroidization rate > 90% and > 80% is 5 ~ 7 grade, which meets the design requirements. The result of non-metallic inclusion detection is no non-metallic inclusion.
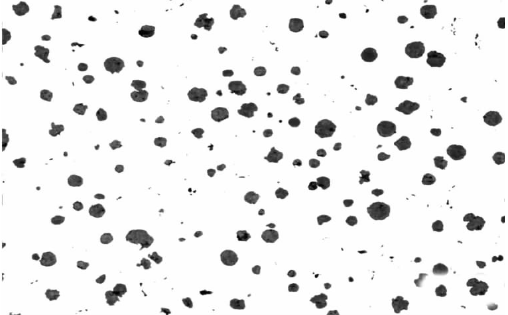