The proportion of raw materials for smelting is scrap: recycled material = 4:6, and the composition of molten iron after spheroidizing treatment.
The pouring temperature is 1493 ℃, the actual pouring time is 8.5 s, the pouring temperature of the first mold is 1417 ℃, and the pouring temperature of the tail mold is 1382 ℃. After pouring, the marks are made, and the box is taken out separately and sent to the laboratory to test the size, internal defects and mechanical properties. Record the performance of molding sand during the test period.
After 70 minutes, the casting is unpacked and offline. The temperature is 550 ℃, which is lower than the phase transformation temperature, which will not affect the matrix structure. The state of the casting after passing through the on-line shot blasting machine is shown in the figure below. It can be seen that the fit clearance of the mold is very small, so there is no burr left on the parting line after shot blasting, and the residual height after riser neck is broken is less than The surface roughness is less than 20, the casting characters are clear and recognizable, and the weight deviation of each cavity casting is less than 50g.
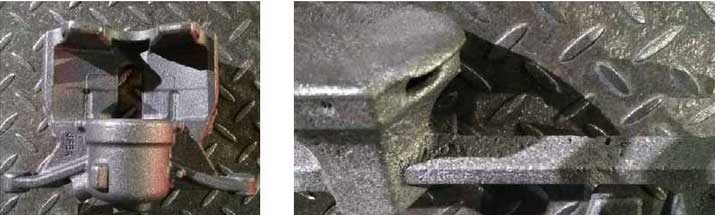
As shown in the figure, there is a lot of scum accumulated on the upper surface of the runner and the lap joint, which indicates that the gating system has a significant slag avoidance effect. The top of the riser outside the template is fully shrunk, realizing the feeding function. Most of the common risers in the middle have no shrinkage. Further inspection of the casting is required to verify the feeding effect of the riser.