After sampling the casting defect location, the scanning electron microscope was used for analysis. After ultrasonic cleaning, the casting defect was observed and analyzed by electron microscope (as shown in the figure). It was determined that the casting defect was a shrinkage casting defect. The basic reason for the formation of shrinkage porosity and shrinkage cavity is mainly due to the wide crystallization temperature range of the alloy, the developed dendrites, and the small and dispersed holes formed by liquid and solidification shrinkage can not be supplemented by external liquid metal.
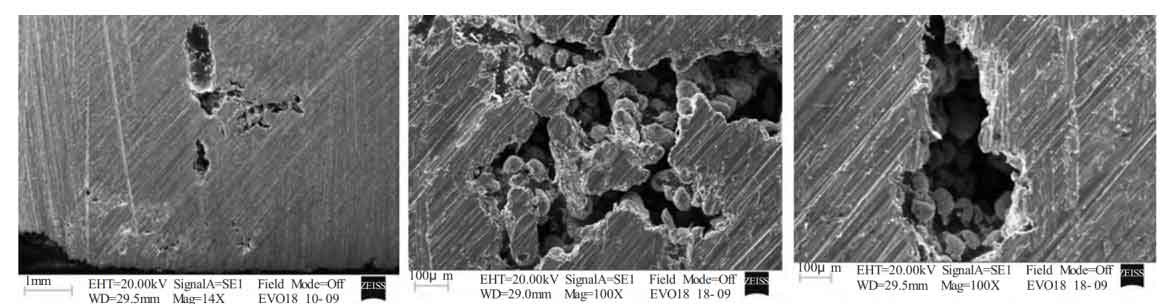
The cylinder head itself is a thin-wall casting with complex internal cavity. The hot spots of the casting are surrounded by sand cores. When their solidification shrinkage is not supplemented by molten iron, it is easy to form shrinkage porosity. The casting defects are located at the joint between the runner and the casting in the gating system, where the casting is thick, the cooling conditions are poor, there are hot spots, and shrinkage casting defects such as shrinkage porosity and shrinkage cavity are easy to occur.