Since there are certain limitations and uneconomies in increasing metal subsidies, it is necessary to consider a process scheme that can achieve effective feeding without structural changes. Dark subsidy is a subsidy form that is not integrated with the casting. There is a thin sand layer between it and the casting. Through heat transfer in the sand layer, the local area of the casting is insulated and heated, and the solidification time of the feeding channel is extended. The casting is fed to form sequential solidification.
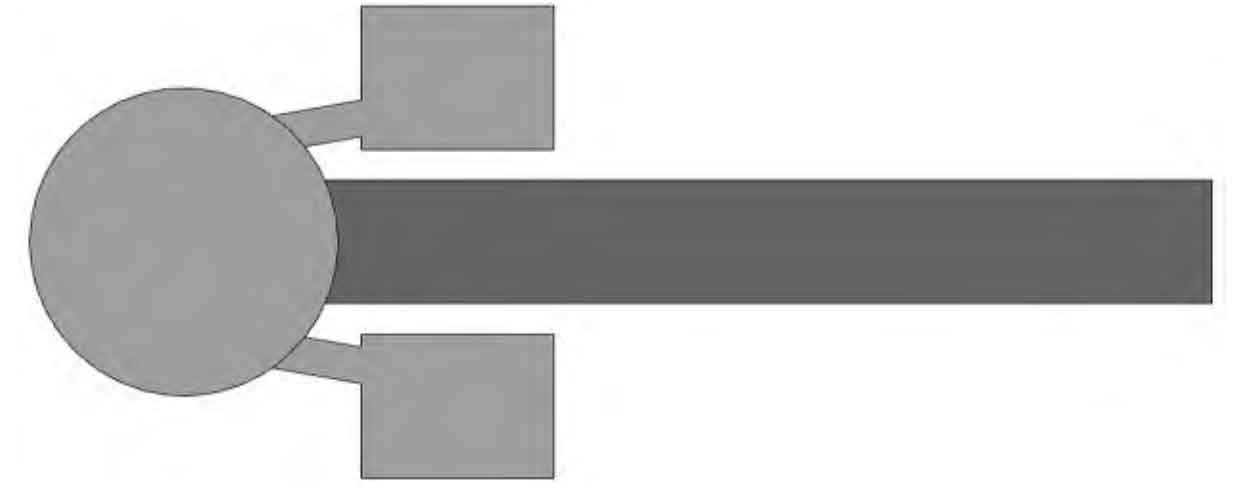
The dark subsidy can also be called non-direct contact subsidy. Taking the simple model in this paper as an example, the dark subsidy is added to the sand separation on both sides of the casting. The simulation results are shown in Fig. 1. On both sides of the casting, it can be found through simulation that the casting solidification realizes sequential solidification and there is no risk of shrinkage porosity. See Fig. 2.
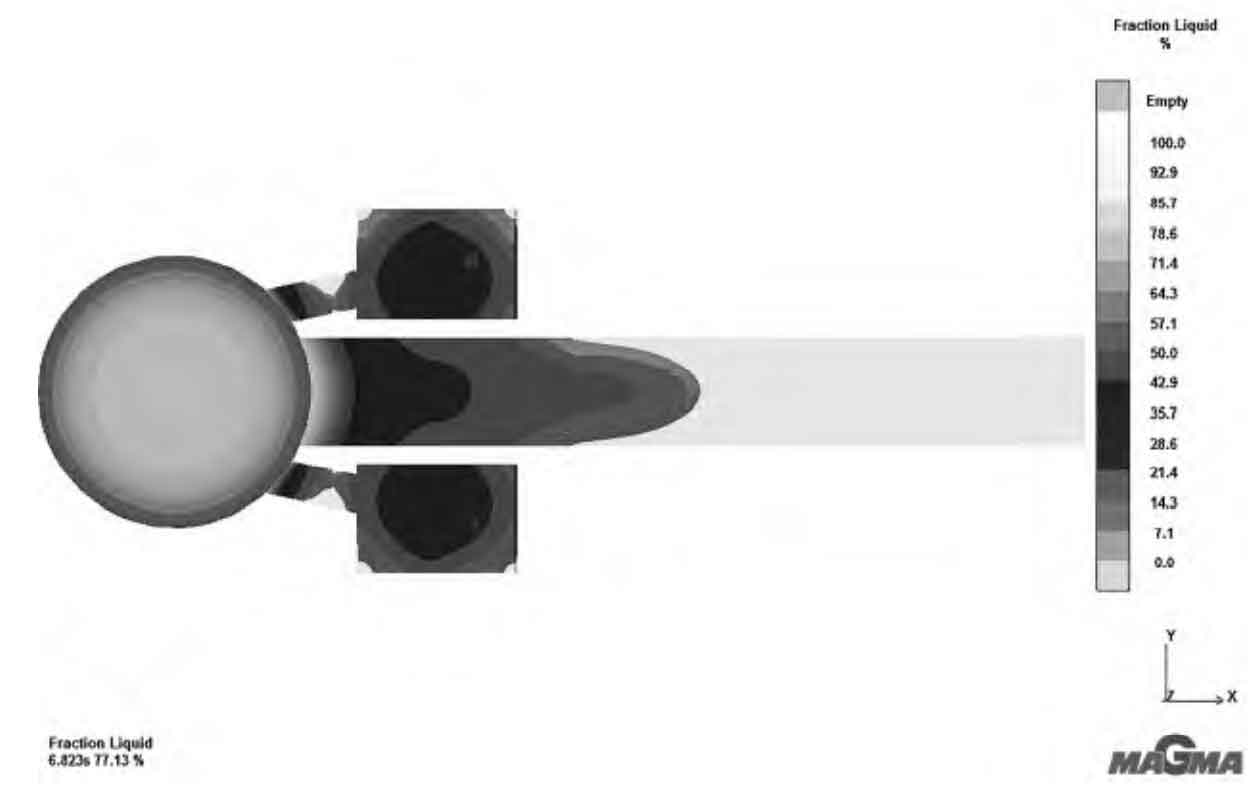
In the sand mold design of increasing the dark subsidy, it may be necessary to add sand blocks or inserts due to parting, which is relatively not a difficult operation. The hidden patch can be separated from the gating system when cutting and removing the riser, which will not increase the difficulty of subsequent cleaning and grinding, and will not increase the weight of the casting. The hidden patch can be used in the furnace, which has little impact on the yield, so it will not increase additional costs.
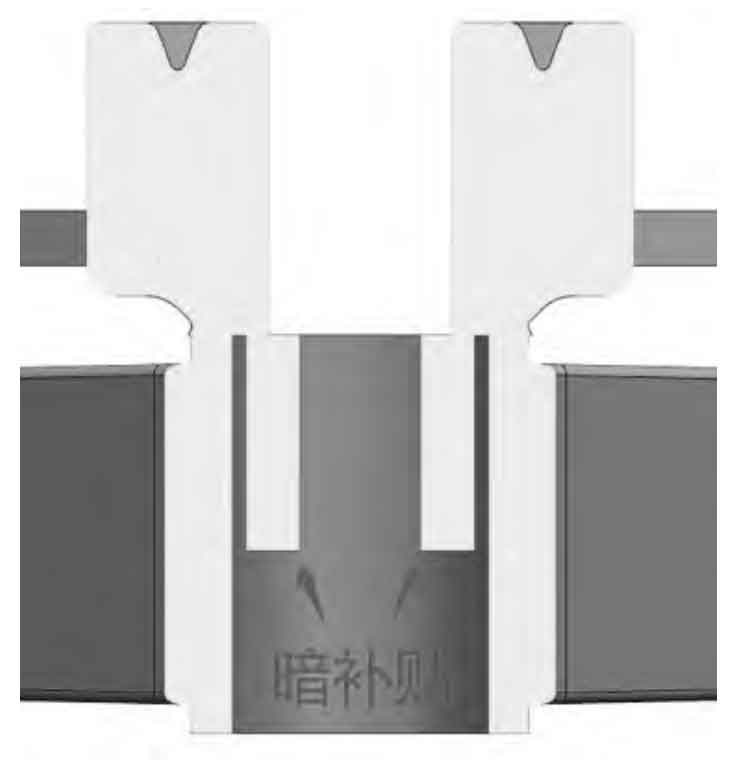
Taking the above support seat products as an example, the process optimization can also be carried out by using the dark subsidy scheme. As shown in Fig. 3, the dark subsidy is separated from the casting by 4-6mm sand layer.
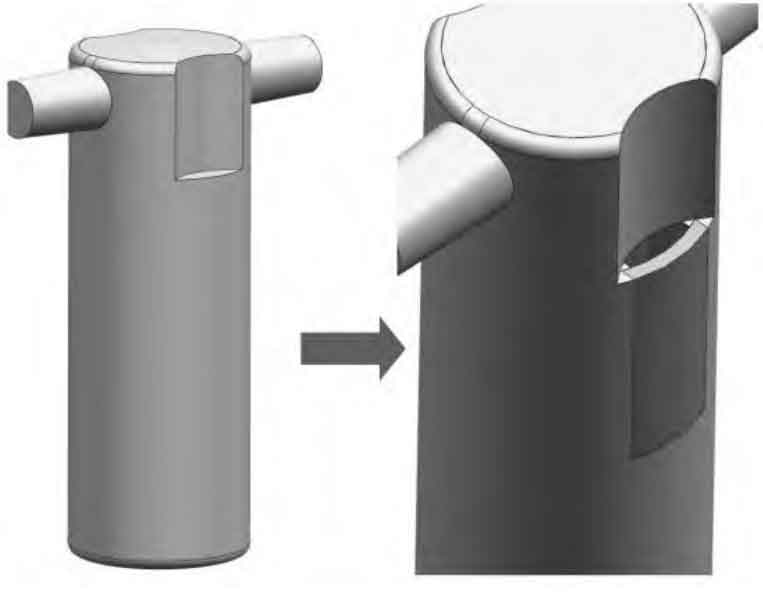
After adding the concealed patch, it is necessary to make a thin sand block on the sand core and bond it with the main sand core to form the cavity of the concealed subsidy, and reserve the water inlet so that the concealed subsidy can be filled during pouring and play a role in the solidification and shrinkage of the casting, as shown in Fig. 4.
In the use of dark subsidies, there are two more important parameters that need to be paid attention to. The thickness of sand barrier and the size of the patch of dark subsidies: the thickness of sand barrier is too large, the effect of dark subsidies on the heat effect of castings is small, and the dark subsidies do not work; The sand separation thickness is too small, and it is difficult to form and lift the sand separation; The size of the dark subsidy is too small, and the cooling of the dark subsidy is faster, which may speed up the cooling of the casting; If the dark subsidy is too large, the surface of the casting will overheat, which may lead to shrinkage cavities on the surface of the casting. In practical application, readers need to explore and summarize according to the types of their products and processes.