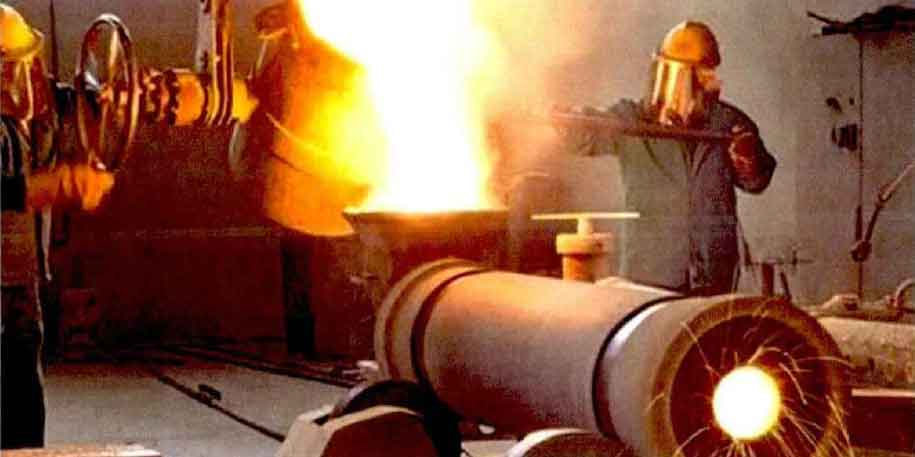
As a key structural member in mining, metallurgy, coal, electric power and other industries, the composite seamless pipe is just opposite to the working surface of the composite roll. Its working surface is the inner surface. The manufacturing principle roughly includes two aspects: the base layer (outer layer) should meet the allowable stress of the pipe, and the composite layer (inner layer) should have high corrosion resistance and wear resistance. Different from the high hardness of the outer layer required by the bimetallic composite roll, the outer layer of the bimetallic composite pipe only needs to meet the requirements of hardness, wear resistance, etc., while the inner layer, as the working surface, must have high toughness and corrosion resistance at the same time, which will inevitably greatly affect its centrifugal casting process. The typical horizontal centrifugal casting process is usually used for bimetal composite pipes. As shown in the figure, the centrifugal casting machine generates centrifugal force during high-speed rotation, so that the outer and inner metal liquid poured into the mold in turn are evenly distributed along the length of the mold, realizing the flow filling and solidification of two metal components, so as to form a bimetal composite pipe with close interface. However, the liquid metal solidifies under the strong centrifugal force field, For the alloy structure prone to specific gravity segregation in static casting, it will cause more serious specific gravity segregation. In the centrifugal casting process of composite pipes, the casting process of gradually increasing mold speed can not only reduce the development of columnar crystals of small tube billets and obtain better equiaxed crystal structure, but also control the loose layer on the inner surface with inclusions and pores within the machining range as far as possible, so as to obtain a sleeve with excellent inner surface quality. At the same time, in order to eliminate the influence of outer layer crack, surface roughness and element segregation on the performance of composite pipe, it can be realized by controlling the mold speed and the continuous rotation time of the mold after the pouring of inner layer liquid metal, that is, if the speed is too high and the continuous rotation time is too long, it is easy to produce outer layer crack, element segregation and uneven thickness of bonding layer; If the rotating speed is too low and the continuous rotating time is too short, the metal liquid will be rained, and the inner layer of the tube blank will be loose, inclusions and uneven concave convex defects on the inner surface will also be caused. The introduction of electromagnetic stirring can also affect the heat and mass transfer process at the crystallization front during the centrifugal casting of cylinder liner, so as to refine the grains after solidification, reduce the axial segregation in continuous casting, and deflect the dendritic structure after directional solidification. That is, increasing the magnetic field strength will reduce the degree of alloy element segregation, significantly reduce the difference between the inner and outer layers, and improve the tensile strength. Fuhanguang et al. Studied in detail the segregation degree of W, Mo and V elements in centrifugal casting high-speed steel rolls by using electromagnetic stirring technology. Because the electromagnetic field produces electromagnetic force in the molten metal, its tangential component is opposite to the direction of molten metal movement, forcing the molten liquid in front of the solid-liquid boundary to flow, causing the change of element distribution coefficient and reducing element segregation, In addition, the electromagnetic force will also promote the metal melt to have a strong scouring effect on the solid-liquid interface and the dendrite end, causing the crystal to fall off from the mold wall and the dendrite to break, promoting the formation of equiaxed crystal, which is conducive to reducing element segregation. During centrifugal casting, Zhang Wei and others adopted double head pouring technology to obtain wear-resistant high chromium cast iron in the inner layer and Q235 steel bimetal pipe in the outer layer. After Re Si Ca Mg composite modification, the impact toughness α K value is from 13 4 j/cm2 to 67 8 j/cm2, greatly improving the toughness of the composite pipe; At the same time, the determination methods of the average angular velocity of the fan-shaped ladle and the initial pouring temperature of the outer metal liquid are also given:
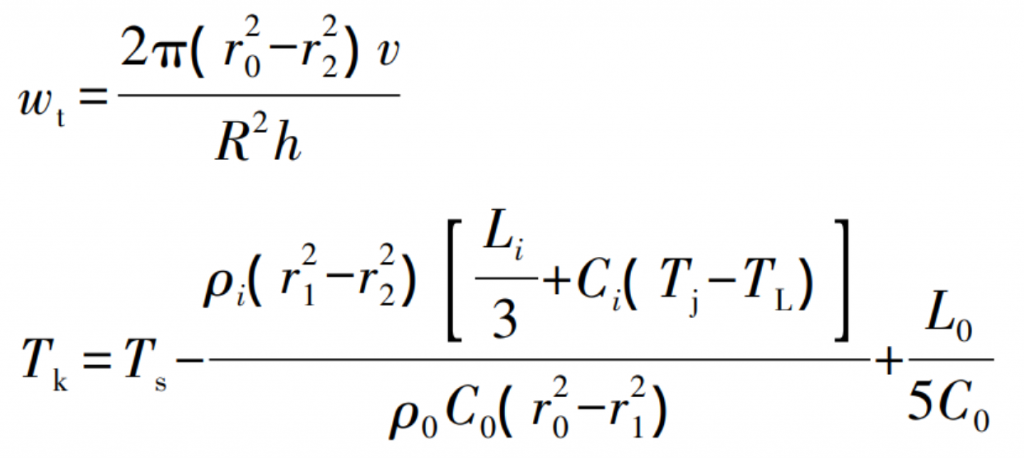
Where: R is the radius of sector envelope, mm; H is the width of fan-shaped bag, mm; W is the average angular velocity of sector packet, RAD /s; R1 is the inner diameter of outer metal pipe, mm; R2 is the inner diameter of inner metal pipe, mm; R0 is the outer diameter of outer metal pipe, mm; TK is the inner surface temperature of the outer metal pipe when pouring the inner layer, ℃; TS is the solidus temperature of outer metal, ℃; ρ i、 ρ 0 is the density of inner and outer metal, kg /m3; Ci and C0 are specific heat capacities of inner and outer metal, j/ (kg ·℃); TJ and TL are the casting temperature and liquidus temperature of the inner metal, ℃; Li and l0 are solidification latent heat of inner and outer metal, j/kg.
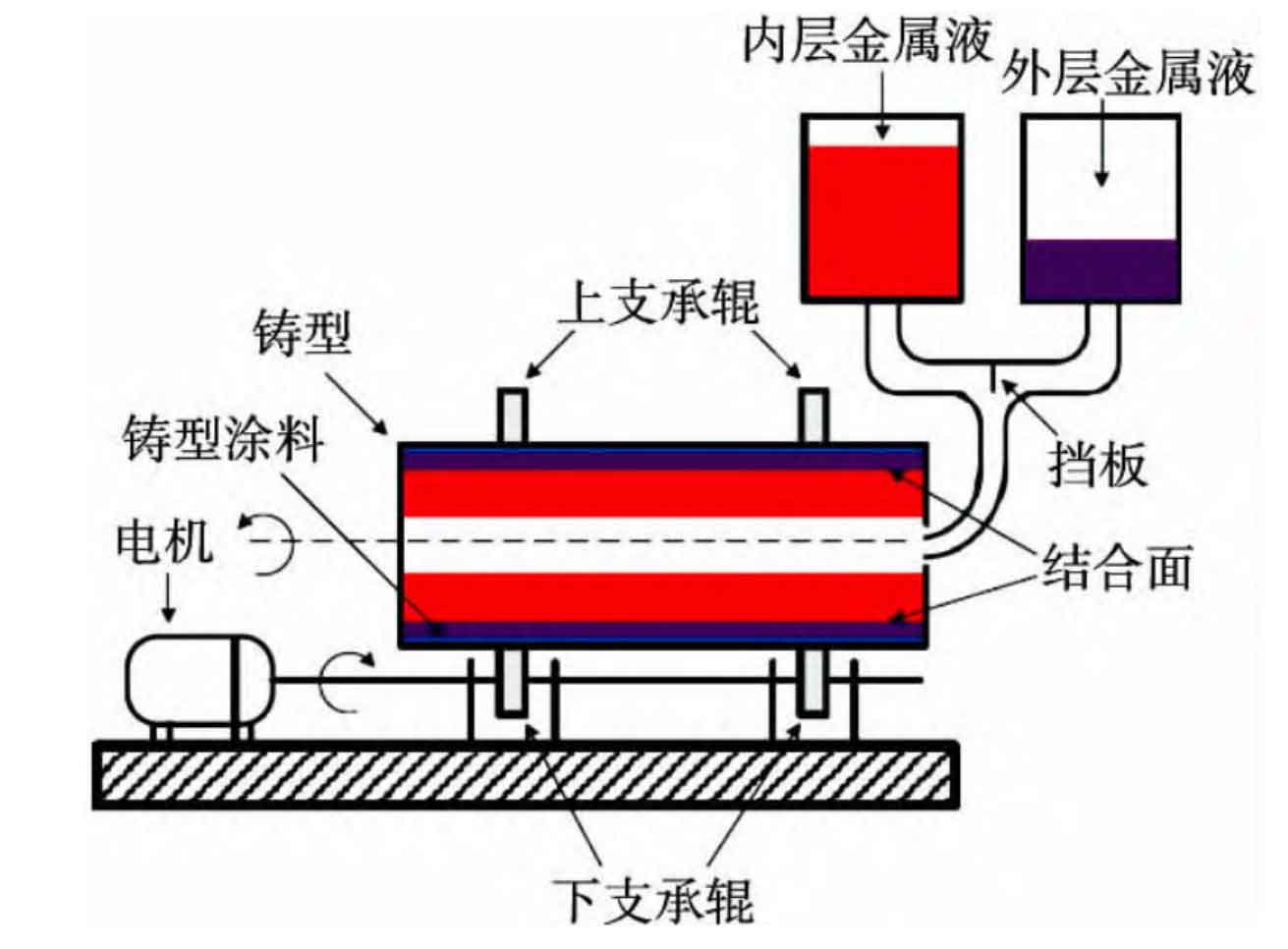
In addition, the combination of the finite element simulation technology and the centrifugal casting process of composite pipe has also been a research hotspot in the past 20 years. The simulation of the centrifugal casting process of bimetal pipe can provide a more reliable process parameter basis for the test. Baoyan et al. Used ANSYS software to simulate and compare the rolling process of bimetallic composite pipe and common single metal pipe. It was found that the cold rolling deformation behavior of the outer Q235 steel / inner 316L stainless steel composite pipe prepared by centrifugal casting is more complex, but the diameter and dimensional accuracy is slightly lower than that of the single metal pipe. After rolling, the outer wall thickness changes greatly, while the inner wall thickness changes slightly. Fangdacheng et al. Studied the centrifugal casting process parameters of outer 45 steel / inner Cr20 white cast iron sleeve, pointed out that inclusion is a main defect of bimetal centrifugal components, mainly concentrated in the bonding interface and inner layer, and put forward the methods to prevent inclusion defects, that is, purifying the metal solution and not adding flux on the interface. Gaojianzhong et al. Concluded that the low casting speed is the main reason for the quality problems such as uneven wall thickness and base crack of bimetal composite pipe blank with ordinary carbon steel as the outer layer and nickel base alloy as the inner layer. On this basis, the centrifugal casting, hot extrusion and heat treatment processes of bimetallic composite pipe with plain carbon steel as the outer layer and nickel base alloy as the inner layer are analyzed. When the mold speed is 950 ~ 1050 r/min, the heating temperature is 1180 ℃, the mold preheating temperature is 460 ℃, the extrusion force is 35 Mn, and the extrusion speed is 65 mm/s, the wall thickness non-uniformity of the pipe blank can be greatly reduced and the defects such as pits and cracks on the inner surface of the pipe blank can be avoided. The key to manufacturing bimetallic composite pipe by centrifugal casting process is to control the pouring interval between inner and outer layers. The interval is too short, the inner and outer alloy liquid are easy to mix, and the regular and stable transition layer cannot be formed; If the interval time is too long, the inner and outer metals are not firmly bonded, forming inclusions, pores and other defects. Dengchuanjie et al. Studied the mold filling and solidification behavior of the outer metal liquid under different centrifugal casting processes with the help of ProCAST simulation software, and gave a method to determine the pouring interval between the inner and outer layers of the composite pipe, that is, when t ≤ TS (t is the temperature of the metal at this point, TS is the solidus temperature of the outer metal), the inner metal liquid can be poured, but this result is only based on the good metallurgical combination of the inner and outer layers, Casting cracks and other defects are not considered. On this basis, Liu Jing et al. Simulated the centrifugal casting process of bimetallic composite pipe with 20 steel as the outer layer and high chromium cast iron as the inner layer, and found that only when the pouring interval between the inner and outer layers is not less than 9 s, can a regular and stable transition layer be formed, Cr diffuses at the interface, and the interface achieves metallurgical bonding. This conclusion has also been verified by other researchers. At the same time, the mechanical properties of the composite pipe were tested. The tensile strength was 223 MPa and the yield strength was 199 MPa. Compared with the tensile strength of 410 MPa specified in gb/t699-1999, the as cast composite pipe had poor tensile properties, and fracture occurred quickly during the tensile process. The fracture morphology showed that the tensile properties of the bimetal composite pipe were mainly determined by the outer 20 steel.