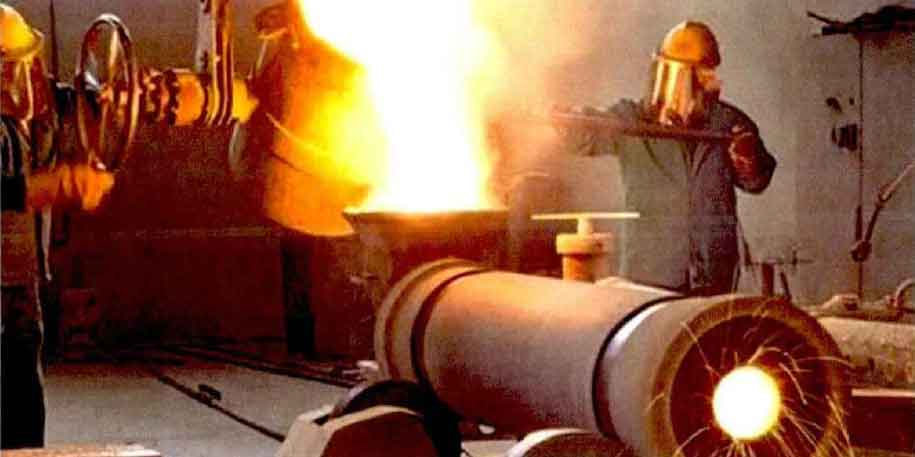
China’s iron and steel industry has developed rapidly, and its output has ranked first in the world for many years. With the increase of iron and steel output, the total demand for steel rolling equipment and its rolls has also increased significantly. The working surface of the composite roll is the outer surface, which needs to meet the requirements of high hardness and high wear resistance. Its common manufacturing processes are mainly liquid-solid compound method and liquid-liquid compound method, such as centrifugal casting compound method, electroslag casting method, continuous casting method, insert casting method, hot isostatic pressing method and spray casting method. Centrifugal casting composite method has become the most important method for manufacturing composite roll because of its simple equipment, compact structure and high production efficiency. The outer layer of bimetallic composite roll is usually made by horizontal centrifugal casting, while the inner layer is made by gravity filling casting. During centrifugal casting, the outer layer determines the strength and hardness of the roll. Low strength leads to weak resistance to damage and shortened service life of the roll; Low hardness will cause roll deformation and affect normal use. In recent years, researchers have done a lot of research on the pouring process, material composition and element diffusion of the working layer of the composite roll. The composite roll sleeve with Cr15, Cr20 and Cr28 high chromium cast iron as the outer layer and gray cast iron as the inner layer is taken as the research object. The effects of different outer materials on the performance of the roll sleeve are analyzed. It is found that the hardness of the roll sleeve with Cr20 high chromium cast iron as the outer layer is the highest, up to 55 75HRC。
On this basis, taking high chromium cast iron with different contents as the outer layer of the composite roll, the chemical composition (mass fraction,%) of the outer high chromium cast iron which is most conducive to improving the mechanical properties of the roll is obtained: 3 11C、20. 19Cr、2. 05Mo、0. 62Si、0. 69Mn、1. 05Ni、0. 024S、0. 035P。 By simulating the centrifugal casting process of the composite roll, wangjianbin et al. Concluded that the factors affecting the outer layer thickness of the composite roll are the casting temperature of the intermediate layer > the heat transfer coefficient of the inner surface > the thickness of the intermediate layer > the coating thickness > the end cover sand material, and the factors affecting the centrifugal casting time of the outer layer are the heat transfer coefficient of the inner surface > the casting temperature of the intermediate layer > the coating thickness > the thickness of the intermediate layer, The results have important guiding significance for the control of process parameters in the preparation of composite rolls by centrifugal casting technology.
In addition, the control of chemical composition and centrifugal casting process parameters is the prerequisite to ensure the performance of the composite roll. Xiapengju et al. Took the high nickel chromium cast iron / gray cast iron composite roll sleeve as an example, through the study of the chemical composition and process parameters of the inner and outer layers, determined that when the outer layer pouring temperature is 1300 ~ 1320 ℃, the pouring time is 30 s, the inner layer pouring temperature is 1280 ~ 1300 ℃, the pouring time is 4 min, and the mold speed is 640 r/min, the The outer interval is 6 At 5 min, the outer surface quality of the roll is significantly improved, and the hardness reaches more than 58hrc, fully meeting the requirements of Yb 4052-91. Wangzhicheng et al. Proposed the method of adding a transition layer in the middle part of the high-speed steel ductile iron composite roll. The chemical composition of the transition layer is similar to that of the core layer. The outer layer is poured first, and then the middle layer is poured. When the temperature drops to 3 ~ 4 Min below the solidus line of the middle layer, the roll core and roll neck are assembled, and finally the pouring is carried out. This unique “three-layer composite process” effectively solves the problem of punching and mixing, and ensures the uniformity of the thickness of the working layer of the roll. At the same time, since the outer and outer surfaces of the working layer have solidified during the bonding process with the intermediate layer, the hardness of the outer layer is also guaranteed. After heat treatment, the hardness of the roll body reaches 78hs (≈ 58hrc). The adoption of the “three-layer composite process” can not only solve the problem of the diffusion of Cr elements in the outer layer, but also overcome the problem of abnormal carbides that are easy to peel off on the joint surface during casting, so that the rolling volume per millimeter of the roll can reach more than 5200 T, and the work efficiency can be significantly increased.
It can be seen that by analyzing the influence of process parameters on the stability and deformation uniformity of centrifugal casting process, the macro plastic deformation of roll and the hardness of working layer can be controlled, which can meet the use requirements under most working conditions. However, the above research only involves the control of process parameters, and has not yet clarified the corresponding microstructure evolution law and mechanism, which can not provide systematic theoretical support for the process control of centrifugal casting bimetal composite roll. Therefore, it is necessary to strengthen the research on the metal flow behavior, grain size, morphology and evolution during pouring, so as to provide a theoretical basis for further study on the mechanical properties of centrifugal casting composite rolls.