Ductile cast iron is widely used in manufacturing components that require high strength, toughness, and ductility. However, machining ductile cast iron poses several challenges due to its unique microstructure and material properties. This article explores the common challenges encountered in machining ductile cast iron components and presents effective solutions to overcome these obstacles.
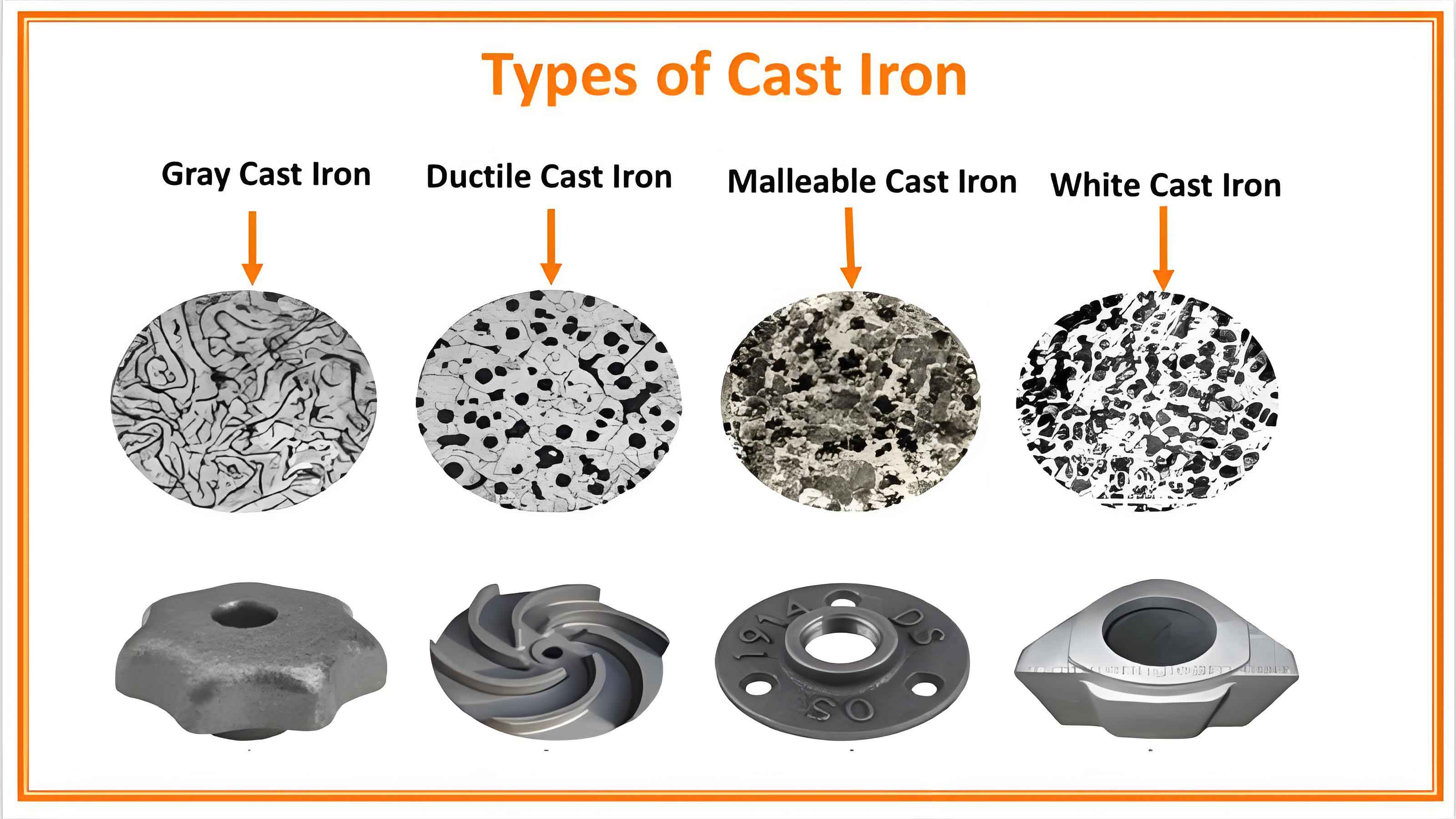
Introduction
Ductile cast iron, also referred to as nodular cast iron or spheroidal graphite iron, contains graphite in the form of nodules. This microstructural feature imparts superior mechanical properties compared to traditional cast irons. Despite its advantages, machining ductile cast iron can be challenging due to factors such as tool wear, heat generation, and surface finish requirements. Addressing these challenges is crucial for improving the efficiency and quality of machined components.
Challenges in Machining Ductile Cast Iron
Tool Wear
One of the primary challenges in machining ductile cast iron is accelerated tool wear. The presence of hard carbides and the abrasive nature of the material contribute to rapid wear of cutting tools.
Table 1: Factors Contributing to Tool Wear
Factor | Description |
---|---|
Hard Carbides | Presence of carbides increases tool wear rate |
Abrasive Nature | Graphite nodules and matrix hardness cause abrasion |
Heat Generation | High cutting temperatures accelerate tool wear |
Heat Generation
High cutting speeds and feed rates required for machining ductile cast iron result in significant heat generation. Excessive heat can adversely affect tool life and dimensional accuracy.
Surface Finish
Achieving a high-quality surface finish on ductile cast iron components can be difficult due to the material’s tendency to form built-up edges and irregularities during machining.
Table 2: Surface Finish Challenges
Challenge | Description |
---|---|
Built-up Edge Formation | Material adhesion to the cutting tool |
Surface Irregularities | Inconsistent surface texture due to material removal |
Dimensional Accuracy | Difficulty maintaining tight tolerances |
Vibration and Chatter
Machining ductile cast iron can induce vibrations and chatter, negatively impacting surface quality and tool life.
Cutting Forces
The high mechanical strength of ductile cast iron results in increased cutting forces, posing additional challenges for machining operations.
Solutions for Machining Ductile Cast Iron
Tool Material and Coatings
Selecting appropriate tool materials and coatings is essential for improving tool life and performance. Carbide tools with wear-resistant coatings, such as titanium nitride (TiN) or diamond-like carbon (DLC), can significantly reduce tool wear.
Table 3: Recommended Tool Materials and Coatings
Tool Material | Coating Type | Benefits |
---|---|---|
Carbide | Titanium Nitride (TiN) | Enhanced wear resistance |
Ceramic | Aluminum Oxide (Al2O3) | Improved heat resistance |
Polycrystalline Diamond | Diamond-like Carbon (DLC) | Reduced abrasion and longer tool life |
Optimized Cutting Parameters
Optimizing cutting parameters, such as cutting speed, feed rate, and depth of cut, can minimize heat generation and improve surface finish.
Table 4: Optimized Cutting Parameters
Parameter | Recommended Value |
---|---|
Cutting Speed | 100 – 200 m/min |
Feed Rate | 0.1 – 0.3 mm/rev |
Depth of Cut | 0.5 – 2 mm |
Coolant Usage | Use of high-pressure coolant systems |
Coolant and Lubrication
Using high-pressure coolant systems and appropriate lubricants can effectively dissipate heat, reduce tool wear, and improve surface finish.
Vibration Control
Implementing vibration control techniques, such as using rigid tool holders, dampening devices, and optimizing machine tool rigidity, can minimize chatter and improve machining stability.
Advanced Machining Techniques
Adopting advanced machining techniques, such as high-speed machining (HSM) and computer numerical control (CNC) machining, can enhance precision and efficiency in machining ductile cast iron components.
Regular Tool Maintenance
Regular inspection and maintenance of cutting tools are essential to ensure consistent performance and prolong tool life.
Case Studies
Case Study 1: Automotive Component Manufacturing
A manufacturer of automotive components faced challenges with tool wear and surface finish when machining ductile cast iron crankshafts. By switching to carbide tools with TiN coatings and optimizing cutting parameters, the manufacturer achieved a 25% increase in tool life and a significant improvement in surface finish.
Case Study 2: Heavy Machinery Parts
In the production of heavy machinery parts, a company experienced excessive heat generation and vibration issues. The implementation of high-pressure coolant systems and vibration dampening techniques resulted in improved machining stability and reduced thermal distortion.
Conclusion
Machining ductile cast iron presents several challenges, including tool wear, heat generation, surface finish, vibration, and high cutting forces. By selecting appropriate tool materials and coatings, optimizing cutting parameters, using effective coolant and lubrication, controlling vibrations, and adopting advanced machining techniques, these challenges can be effectively addressed. Implementing these solutions not only enhances the efficiency and quality of machined ductile cast iron components but also contributes to cost savings and increased productivity in the metallurgical industry.