1. Introduction
1.1 Background
Magnesium aluminum alloy, as a new type of material with excellent comprehensive properties, has been widely used in various fields such as aerospace, automotive, electronics, and architecture due to its characteristics of high strength, low density, good corrosion resistance, and small thermal expansion coefficient. However, the preparation methods of magnesium aluminum alloy are limited, and the cost is relatively high. Casting is one of the main methods for preparing magnesium aluminum alloy at present, which can quickly and efficiently transform the metal liquid into solid products. But in the casting process, there are also many difficulties due to the special characteristics of magnesium aluminum alloy, such as easy generation of bubbles and uneven sintering.
1.2 Research Significance
The study of casting defects in magnesium aluminum alloy and the exploration of corresponding solutions are of great significance for improving the quality and performance of magnesium aluminum alloy castings, reducing production costs, and ensuring production safety. By understanding the defect formation mechanism and taking effective preventive and corrective measures, the utilization rate of magnesium aluminum alloy can be improved, and its application range can be further expanded.
1.3 Research Objectives and Methods
This article mainly focuses on analyzing the casting defect mechanism of magnesium aluminum alloy and proposing corresponding countermeasures. The research methods mainly include literature research, experimental analysis, and data comparison. Through the collection and analysis of relevant literature, the basic knowledge and research status of magnesium aluminum alloy casting are understood. Through experimental research, the influence of different factors on the casting defect of magnesium aluminum alloy is explored, and the effectiveness of the proposed countermeasures is verified.
2. Magnesium Aluminum Alloy Casting Defect Analysis
2.1 Magnesium Aluminum Alloy Overview
Magnesium aluminum alloy is an important high-strength and lightweight metal material. Its main components are magnesium (Mg) and aluminum (Al). The magnesium content is generally between 30% and 60%, and the aluminum content is relatively low, usually not exceeding 20%. The characteristics of magnesium aluminum alloy include high strength, high toughness, corrosion resistance, and good heat treatment performance, so it is widely used in aerospace, automotive manufacturing, electronic devices, and other fields. The casting technology of magnesium aluminum alloy mainly includes melt casting method and extrusion forming method. The following table summarizes the main properties of magnesium aluminum alloy:
Properties | Description |
---|---|
Chemical Composition | Mainly Mg and Al, with specific content ranges |
Physical Properties | High strength, low density, small thermal expansion coefficient |
Mechanical Properties | Good tensile strength, hardness, and toughness |
Application Fields | Aerospace, automotive, electronics, architecture |
2.2 Casting Defect Types
In the casting process of magnesium aluminum alloy, common defects include pores, cracks, inclusions, and residual slag.
Defect Type | Description |
---|---|
Pores | Caused by factors such as too fast pouring speed or too high temperature, affecting the quality of the casting seriously |
Cracks | Mainly due to too slow or excessive cooling rate, also related to thermal damage on the metal surface |
Inclusions | The phenomenon of other substances mixed in the melt, reducing the quality of the casting |
Residual Slag | Unmelted solid particles remaining inside the casting, leading to low hardness and poor strength |
2.3 Casting Defect Causes
2.3.1 Gas Evolution
When the metal liquid is poured, it will expand under the action of external pressure. If the flow speed and temperature of the melt are not well controlled at this time, the gas cannot be discharged smoothly, resulting in the formation of bubbles or pores. The main reasons for gas evolution are insufficient melt fluidity and too high cooling rate.
2.3.2 Crack Formation
Cracks are mainly caused by too fast or improper cooling rate. When the cooling rate is too fast, the internal stress of the casting is too large, which is easy to cause cracks. In addition, factors such as material quality and mold design also have an impact on crack formation.
2.3.3 Other Defects
Residual inclusions and oxide layers are also common casting defects. Residual inclusions are mainly caused by the poor fluidity of the melt, while oxide layers are formed due to the oxidation reaction of the metal surface during the casting process.
2.4 Casting Defect Hazards
Casting defects can be divided into surface defects, internal defects, and mechanical defects. Surface defects such as cracks, crazing, and sand holes will damage the appearance of the product and shorten its service life. Internal defects such as pores, inclusions, and residues will affect the strength and durability of the product. Mechanical defects caused by improper casting process or uneven material will directly affect the use effect and safety performance of the product.
2.5 Casting Defect Prevention Measures
2.5.1 Prevention of Pore Defects
To avoid the formation of pores, the pouring speed and temperature should be controlled during the pouring process, and sufficient cooling time should be maintained to reduce the impact of pressure fluctuations. In addition, vacuum extraction technology can be used to reduce the gas content. Adjusting the pouring method, such as using stratified pouring or spray pouring, can also help reduce pressure fluctuations.
2.5.2 Prevention of Crack Defects
To prevent cracks, high-quality raw materials should be selected, and the operation process should be strictly followed. At the same time, the mold design and manufacturing work should be strengthened. Reasonable mold design can ensure uniform cooling of the casting and reduce internal stress.
2.5.3 Prevention of Inclusion Defects
To avoid inclusions, the shape of the molten pool can be optimized, and the fluidity of the melt can be improved. For example, adding appropriate fluxes can help remove impurities in the melt and improve the quality of the casting.
2.5.4 Prevention of Residual Slag Defects
To avoid residual slag, it is necessary to ensure that the melt is fully dissolved before starting the pouring process. Regular inspection and cleaning of the melting equipment can also help prevent the formation of residual slag.
3. Magnesium Aluminum Alloy Casting Defect Prevention and Control Measures
3.1 Improving the Pouring Process
3.1.1 Increasing the Cooling Rate
Increasing the cooling rate during the pouring process can reduce the internal stress distribution of the casting. This can be achieved by using cooling devices such as water-cooled molds or air-cooled systems. The following table shows the effect of different cooling rates on the casting quality:
Cooling Rate | Effect on Casting Quality |
---|---|
Low Cooling Rate | May lead to large grain size and poor mechanical properties |
Moderate Cooling Rate | Can improve the microstructure and mechanical properties of the casting |
High Cooling Rate | May cause cracks due to excessive internal stress |
3.1.2 Optimizing the Pouring Speed and Pressure
Optimizing the pouring speed and pressure can make the pouring process more stable and uniform. This can be achieved by using advanced pouring equipment with precise control functions. The following table shows the relationship between pouring speed, pressure, and casting quality:
Pouring Speed | Pouring Pressure | Effect on Casting Quality |
---|---|---|
Too Fast | High | Easy to generate bubbles and inclusions, affect the surface quality of the casting |
Moderate | Moderate | Can obtain good casting quality |
Too Slow | Low | May lead to incomplete filling and porosity |
3.1.3 Using Special Additives
Using special additives can enhance the strength and hardness of the casting. For example, adding elements such as titanium (Ti) and zirconium (Zr) can refine the grain structure of the casting and improve its mechanical properties. The following table shows the effect of different additives on the casting properties:
Additive | Effect on Casting Properties |
---|---|
Titanium (Ti) | Grain refinement, improved strength and hardness |
Zirconium (Zr) | Similar to Ti, also has a certain effect on improving corrosion resistance |
Strontium (Sr) | Modifies the eutectic structure, improves the fluidity and mechanical properties of the alloy |
3.2 Optimizing the Alloy Composition
3.2.1 Adjusting the Proportion of Magnesium and Aluminum
Increasing the magnesium content can improve the strength and hardness of the alloy, while appropriately reducing the aluminum content can ensure the fluidity and formability of the casting. The following table shows the influence of different magnesium and aluminum contents on the alloy properties:
Mg Content (%) | Al Content (%) | Effect on Alloy Properties |
---|---|---|
High | Low | High strength and hardness, but may reduce fluidity |
Moderate | Moderate | Balanced properties, good comprehensive performance |
Low | High | Good fluidity, but relatively low strength |
3.2.2 Adding Other Elements
Adding a small amount of other elements such as copper (Cu) and zinc (Zn) can enhance the comprehensive properties of the alloy. For example, copper can improve the heat treatment performance of the alloy, and zinc can improve the corrosion resistance. The following table shows the effect of different alloying elements on the alloy properties:
Alloying Element | Effect on Alloy Properties |
---|---|
Copper (Cu) | Improves heat treatment response, increases strength |
Zinc (Zn) | Enhances corrosion resistance |
Manganese (Mn) | Increases strength and hardness, improves hot workability |
3.3 Improving Material Properties
3.3.1 Controlling the Pouring Speed and Temperature
Controlling the pouring speed and temperature can control the crystallinity and microstructure of the casting. Appropriate pouring speed and temperature can ensure uniform cooling of the casting and improve its mechanical properties. The following table shows the influence of different pouring speeds and temperatures on the casting microstructure and properties:
Pouring Speed | Pouring Temperature | Effect on Casting Microstructure and Properties |
---|---|---|
Fast | High | Fine grains, high strength, but may cause cracks |
Moderate | Moderate | Good microstructure, balanced mechanical properties |
Slow | Low | Coarse grains, relatively low strength |
3.3.2 Using Heat Treatment Technology
Using heat treatment technology can change the microstructure and morphological characteristics of the casting, thereby enhancing its strength and hardness. Common heat treatment methods include solution treatment and aging treatment. The following table shows the effect of different heat treatment processes on the casting properties:
Heat Treatment Process | Effect on Casting Properties |
---|---|
Solution Treatment | Dissolves precipitates, homogenizes the microstructure, improves plasticity |
Aging Treatment | Precipitates fine particles, increases strength and hardness |
Solution + Aging Treatment | Combines the advantages of the two, obtains good comprehensive mechanical properties |
3.3.3 Using Additives or Modification Methods
Using additives or modification methods can increase the toughness and corrosion resistance of the casting. For example, adding rare earth elements can refine the grain structure and improve the mechanical properties and corrosion resistance of the alloy. The following table shows the effect of different additives and modification methods on the casting properties:
Additive/Modification Method | Effect on Casting Properties |
---|---|
Rare Earth Elements | Grain refinement, improved mechanical properties and corrosion resistance |
Surface Modification | Forms a protective layer on the surface, improves corrosion resistance and wear resistance |
Composite Reinforcement | Adds reinforcing materials such as fibers or particles to improve mechanical properties |
3.4 Improving the Microstructure
3.4.1 Adjusting the Pouring Speed and Temperature
Reducing the pouring speed can reduce the generation rate of bubbles, and increasing the cooling rate can accelerate the solidification process and improve the organizational stability of the casting. The following table shows the influence of different pouring speeds and cooling rates on the casting microstructure:
Pouring Speed | Cooling Rate | Effect on Casting Microstructure |
---|---|---|
Fast | Slow | Coarse grains, possible porosity and cracks |
Moderate | Moderate | Fine and uniform grains, good microstructure |
Slow | Fast | Fine grains, improved organizational stability |
3.4.2 Using Other Methods
Using methods such as spraying technology and vacuum casting can improve the performance of the casting. Spraying technology can improve the surface quality of the casting, and vacuum casting can reduce the gas content in the casting and improve its density. The following table shows the characteristics of different casting improvement methods:
Casting Improvement Method | Characteristics |
---|---|
Spraying Technology | Improves surface finish, can form special surface textures |
Vacuum Casting | Reduces porosity, improves density and mechanical properties |
Semi-solid Casting | Combines the advantages of liquid and solid forming, good formability and mechanical properties |
4. Magnesium Aluminum Alloy Casting Defect Treatment
4.1 Optimizing the Pouring Temperature
The pouring temperature has a significant impact on the casting quality. Too high a pouring temperature can cause gas evolution and cracks, while too low a temperature can lead to increased porosity. The following table shows the influence of different pouring temperatures on the casting defects:
Pouring Temperature | Effect on Casting Defects |
---|---|
High | Gas evolution, cracks |
Moderate | Good casting quality |
Low | Increased porosity |
To optimize the pouring temperature, methods such as adjusting the pouring rate, using additives to inhibit bubble formation, and using vacuum pumping technology to remove impurities can be adopted.
4.2 Optimizing the Pouring System
The design and commissioning of the pouring system are crucial for improving the casting quality. Traditional pouring systems may have problems such as oil leakage, which can lead to casting defects. Using a solenoid valve-controlled nozzle pouring method can improve the pouring effect. In addition, attention should be paid to factors such as pouring speed and temperature to ensure the maximum quality and performance of the casting. The following table shows the comparison between the traditional and improved pouring systems:
Pouring System | Advantages | Disadvantages |
---|---|---|
Traditional (Hydraulic Pump-driven Nozzle) | Simple operation | Oil leakage, possible casting defects |
Improved (Solenoid Valve-controlled Nozzle) | Precise control, better pouring effect | Higher cost, requires more maintenance |
4.3 Reasonable Design of Pouring Speed
Reasonable pouring speed can effectively reduce casting defects. The pouring speed should be selected according to the influence factors such as melt fluidity and the cooling rate and crystallinity distribution of different parts. The following table shows the relationship between pouring speed and casting quality:
Pouring Speed | Effect on Casting Quality |
---|---|
Too Fast | Bubbles, inclusions, poor surface quality |
Moderate | Good casting quality |
Too Slow | Incomplete filling, porosity |
5. Conclusion
In the casting process of magnesium aluminum alloy, due to factors such as its high melting point and easy oxidation, common defects such as bubbles and cracks are prone to occur. To avoid these defects, effective measures need to be taken, such as adjusting the pouring speed, temperature, and pressure, using vacuum or inert gas technology to reduce the gas content, and strengthening the selection and formulation design of materials. Magnesium aluminum alloy has high strength and corrosion resistance and can be widely used in practical applications. However, in different production conditions, there may be some special problems that need to be further solved. Future research can focus on further optimizing the casting process, exploring new alloy compositions and additives, and improving the performance and quality of magnesium aluminum alloy castings.
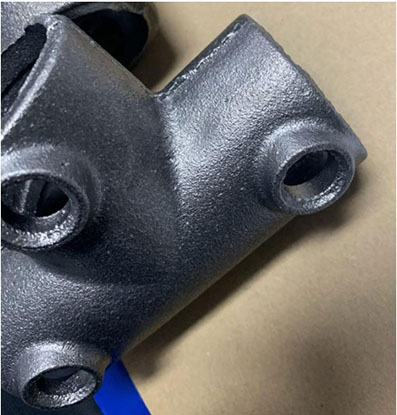